- Joined
- Mar 20, 2008
- Messages
- 165
Hey guys hows it going?
I'm Miles and I'm 19 years old from Ontario Canada, i used to be really into knives and knifemaking and then i kind of lost interest for a little while. I had always wanted to make a knife and recently ive put pen to paper and started. Ive never worked with steel before and aside from a dremel, i only have hand tools.
This is my first knife ever made and it's a shiv compared to some of the knives that people make on this site but Im gunna post pictures as I go and hopefully get some feedback.
I started with this saw blade that i bought off a guy in toronto from kijiji for 5$
Got rid of some of the rust
Drew out my plans and tracers
Started cutting with the dremel! (Safety first, definitely recommend having a plexiglass shield, it saved me from a huge potential injury)
Started an arm workout with the hand files!
It's still very far from being finished.
I'm Miles and I'm 19 years old from Ontario Canada, i used to be really into knives and knifemaking and then i kind of lost interest for a little while. I had always wanted to make a knife and recently ive put pen to paper and started. Ive never worked with steel before and aside from a dremel, i only have hand tools.
This is my first knife ever made and it's a shiv compared to some of the knives that people make on this site but Im gunna post pictures as I go and hopefully get some feedback.
I started with this saw blade that i bought off a guy in toronto from kijiji for 5$

Got rid of some of the rust

Drew out my plans and tracers


Started cutting with the dremel! (Safety first, definitely recommend having a plexiglass shield, it saved me from a huge potential injury)
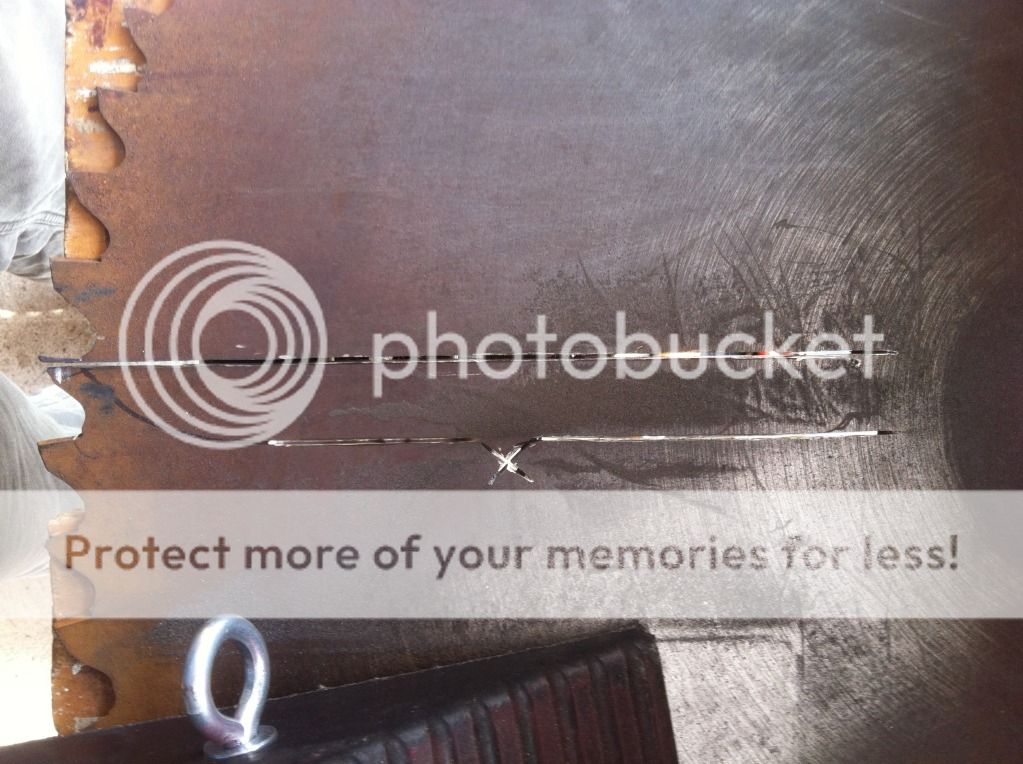


Started an arm workout with the hand files!
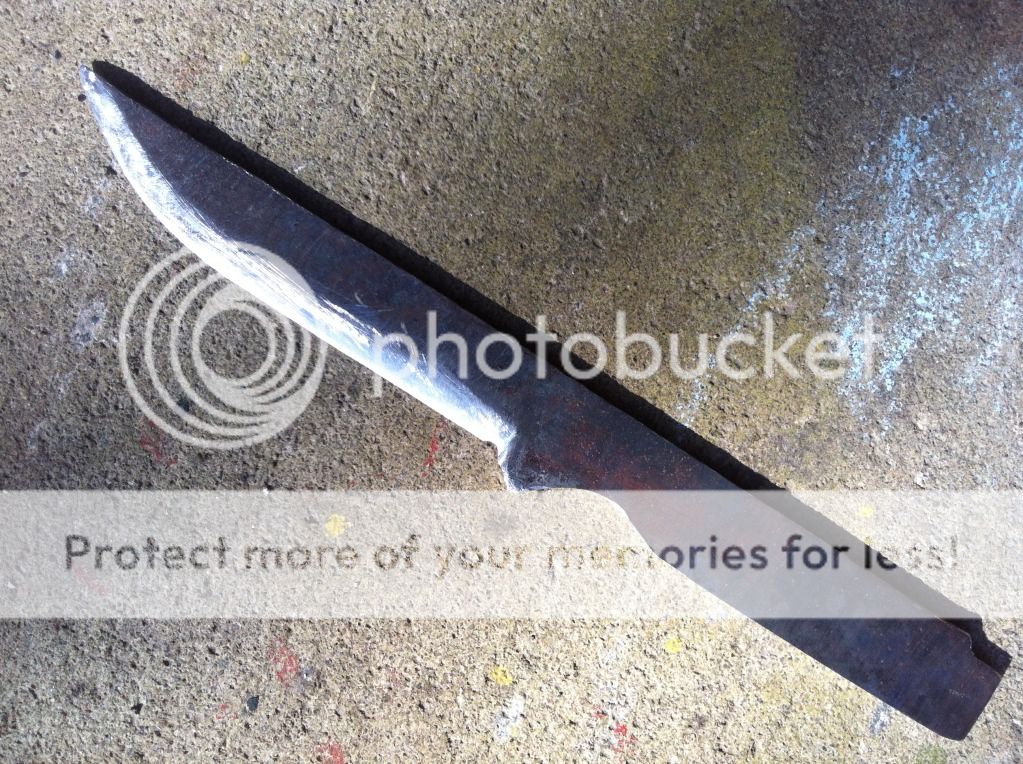

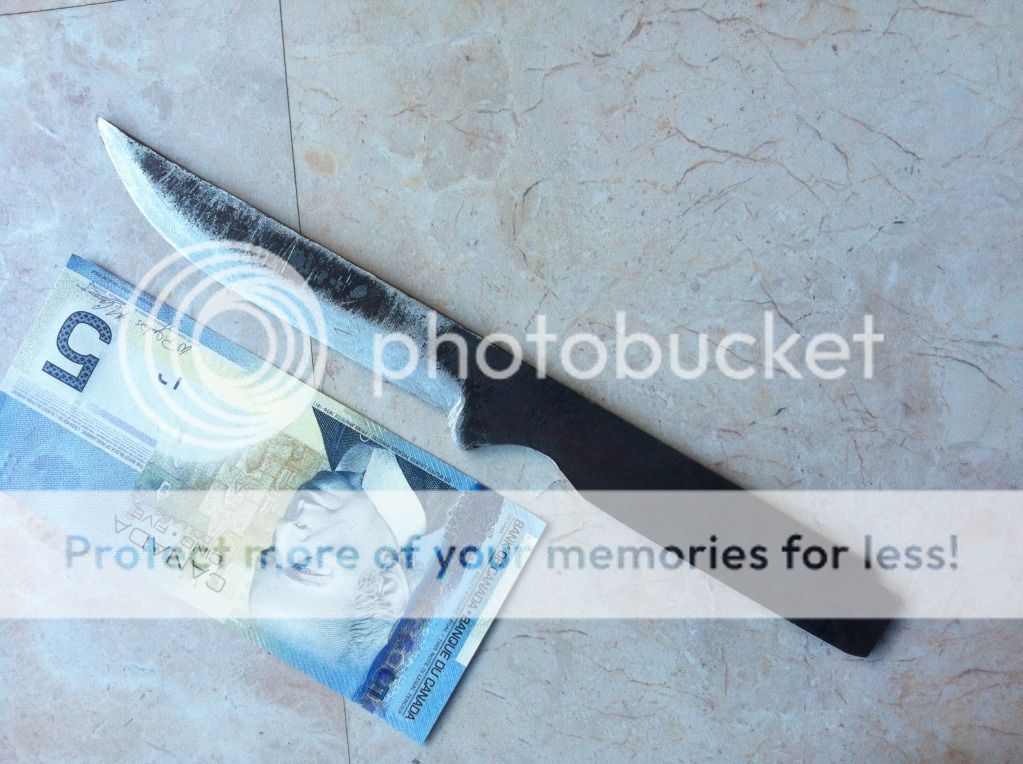
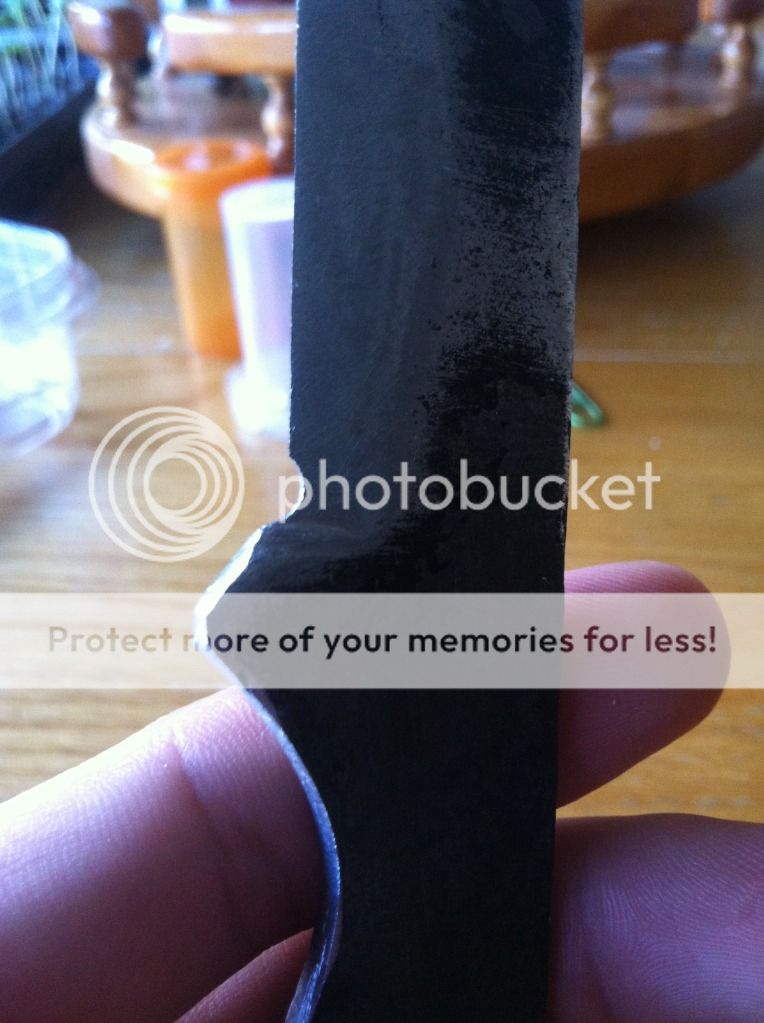
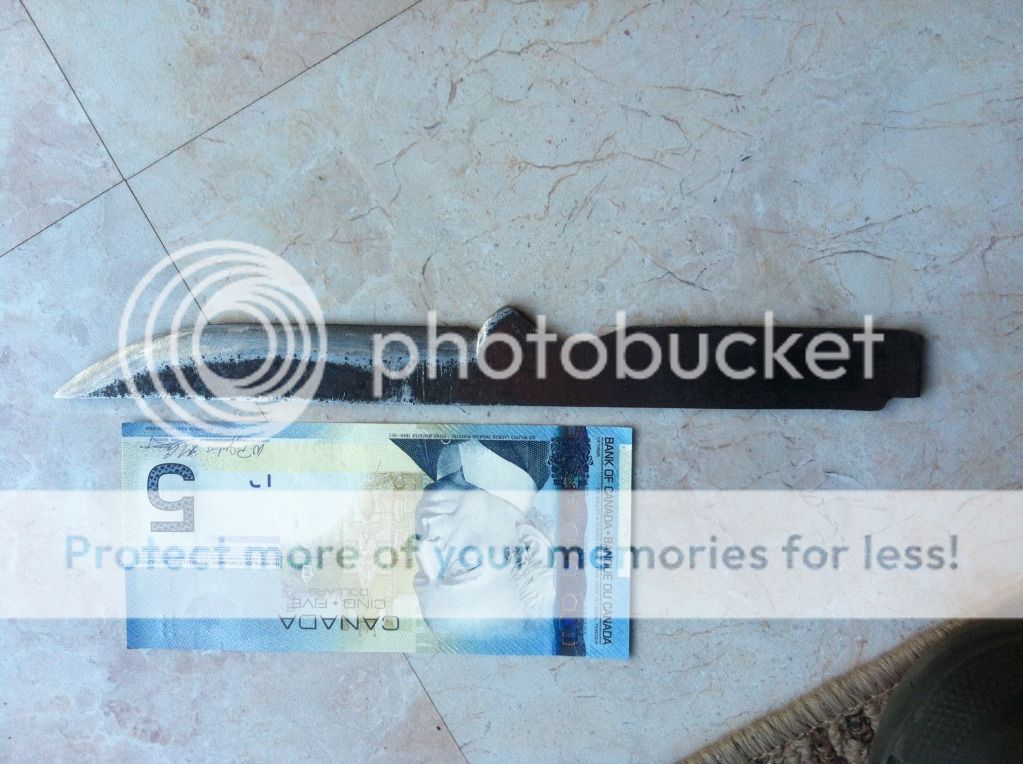
It's still very far from being finished.