- Joined
- Jun 6, 2008
- Messages
- 1,574
I had wanted one of these for a long time. Being a big fan of the Skookum Bush Tool the Terassaur was a must have when I found out that Andy and Joe had teamed up on a design. Think I waited over a year checking the forum to find one I liked when I had the cash.
I had started making my own sheaths some time ago so I put the extra $30 from the blade only purchase into materials. This is my first dangler with a lot of influence from JRE/BHK and other makers. It has a lot of drop to clear the wide waist belt on my Arc'Teryx backpack. 9oz. tooling leather, Fiebing's Chocolate dye, solid brass hardware, artificial sinew and a Bees' wax coating.
The knife came with a rounded off spine that wouldn't touch a ferro rod. I flattened out the spine to give it a crisp edge but it still doesn't really throw good sparks. Acts like it is differentially heat treated compared to my other full hard blades.
The edge is stout and bites good into wood. Handle is super comfortable with a lot of room for different holds. I beveled the crisp edge on the front of the handle to reduce the wear on the stitching of the sheath.
I think I'll leave the edge somewhat thick on it for durability. With a 5/32" thick spine, low blade height and the edge bevel it isn't the best slicer but that's not how I plan on using it. It carves, notches, pierces and batons great. After saying that I must also say it can hang with most of my other outdoor knives in the kitchen as well.
I like the overall design. Especially the low blade height. Makes for a stout but streamlined tool that doesn't have a lot of rotational torque transferred to the hand during heavy cutting. Only negative to that is there isn't much of an aggressive contour for the sheath to hold the blade tight but a good application of Bees' wax stiffened it up and helps a lot.
Overall I really like it and Andy did a great job on it. It has some stiff competition with some of the other blades that I have but think we'll have many adventures together!
I had started making my own sheaths some time ago so I put the extra $30 from the blade only purchase into materials. This is my first dangler with a lot of influence from JRE/BHK and other makers. It has a lot of drop to clear the wide waist belt on my Arc'Teryx backpack. 9oz. tooling leather, Fiebing's Chocolate dye, solid brass hardware, artificial sinew and a Bees' wax coating.
The knife came with a rounded off spine that wouldn't touch a ferro rod. I flattened out the spine to give it a crisp edge but it still doesn't really throw good sparks. Acts like it is differentially heat treated compared to my other full hard blades.
The edge is stout and bites good into wood. Handle is super comfortable with a lot of room for different holds. I beveled the crisp edge on the front of the handle to reduce the wear on the stitching of the sheath.
I think I'll leave the edge somewhat thick on it for durability. With a 5/32" thick spine, low blade height and the edge bevel it isn't the best slicer but that's not how I plan on using it. It carves, notches, pierces and batons great. After saying that I must also say it can hang with most of my other outdoor knives in the kitchen as well.
I like the overall design. Especially the low blade height. Makes for a stout but streamlined tool that doesn't have a lot of rotational torque transferred to the hand during heavy cutting. Only negative to that is there isn't much of an aggressive contour for the sheath to hold the blade tight but a good application of Bees' wax stiffened it up and helps a lot.
Overall I really like it and Andy did a great job on it. It has some stiff competition with some of the other blades that I have but think we'll have many adventures together!
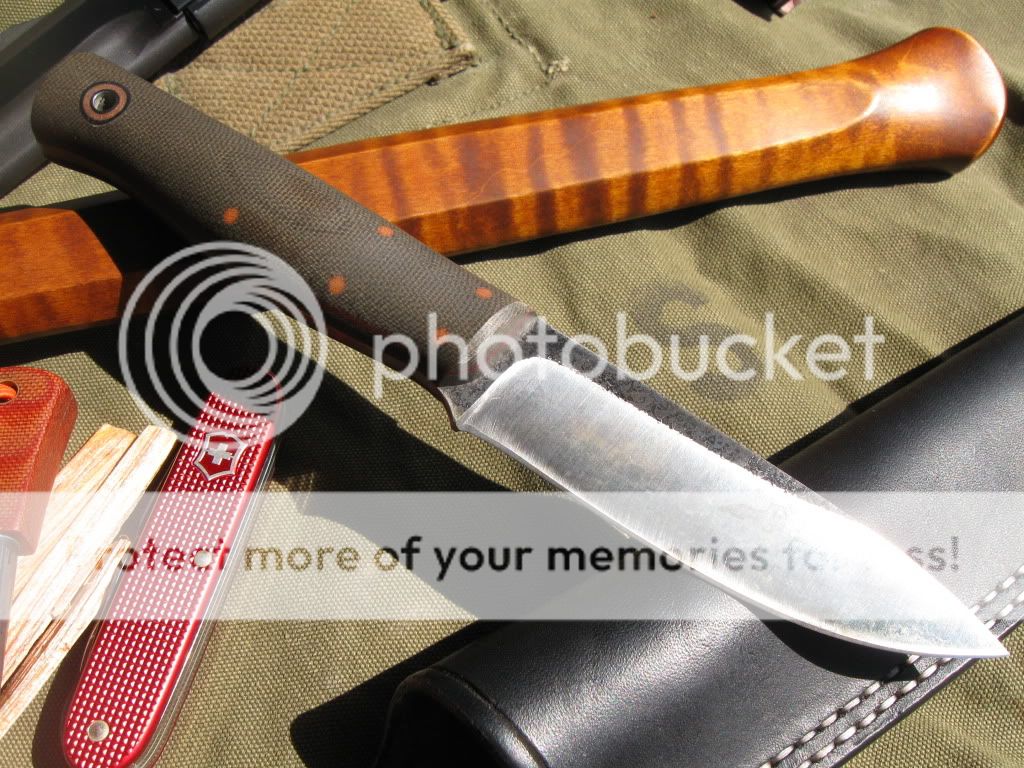





