I purchased this anvil locally. Its dimensions are 24x 4.5x11 and weighs 167 pounds. It rings very well and rebound appears good as well (although I have never felt other anvils). I built the stand, added the chain and put some silicone under the anvil to help reduce noise. I also used a sanding block on the face with 150 grit paper for a few strokes and removed some rust with a wire brush on my hand drill. Now for the questions:
Anyone know what the maker may be? There are faint markings on the side but I really cannot make anything out.
Does the face look good enough to forge with or should I try to have it surface ground?
What can I do to make it look cleaner? Continue with wire brush, paint, or any other suggestions.
I can more pics if they would be helpful.
A propane forge will be here Wednesday and I can wait to try this out.
Thanks
John
Anyone know what the maker may be? There are faint markings on the side but I really cannot make anything out.
Does the face look good enough to forge with or should I try to have it surface ground?
What can I do to make it look cleaner? Continue with wire brush, paint, or any other suggestions.


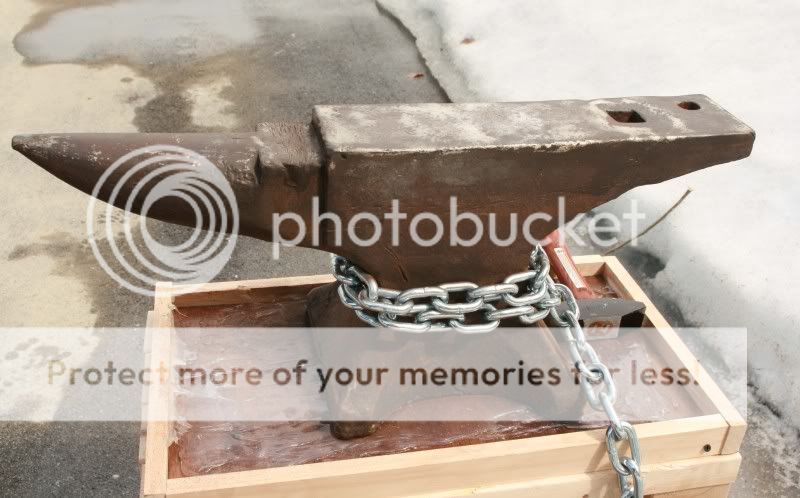

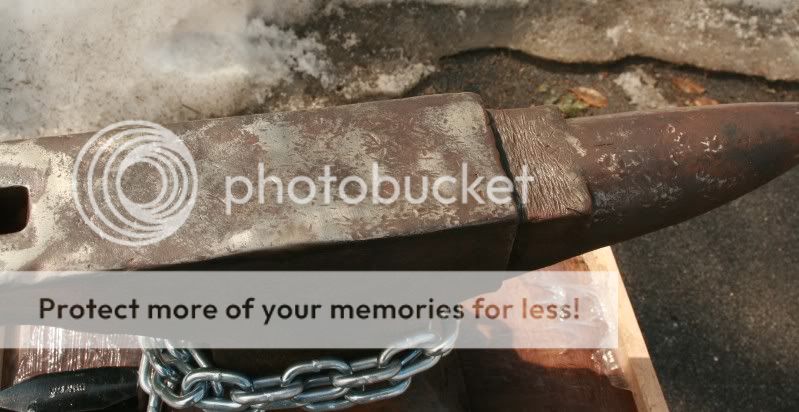

I can more pics if they would be helpful.
A propane forge will be here Wednesday and I can wait to try this out.
Thanks
John