- Joined
- Jul 3, 2014
- Messages
- 357
I started machining my hoddy knives. I work at a small machine shop that is nice enough to let me jump on the 2 axis cnc once in a while.
About 4 years ago I made a 23.5 inch cpm3V chopper called the grinch. It was 0.220 thick and 2.3 wide. The handle could be handled two handed but was shorter.
Long and the short is I started to explore making a faster, lighter and backpackable grinch.
I drew up a design in bobcad and made it. I recently finished it and have been testing. I live up north and it was 0 degrees this morning. I had it hardened a 58 59RC because it the lower temps it will endure.
When i go winter camping i have a 24inch saw and a cutting impliment. Mainly cutting 5 to 6 inch and under wood.
Well it is handling as expected. 0.150 stock. 1lb 6 oz. 23.5 inches overall.
About 4 years ago I made a 23.5 inch cpm3V chopper called the grinch. It was 0.220 thick and 2.3 wide. The handle could be handled two handed but was shorter.
Long and the short is I started to explore making a faster, lighter and backpackable grinch.
I drew up a design in bobcad and made it. I recently finished it and have been testing. I live up north and it was 0 degrees this morning. I had it hardened a 58 59RC because it the lower temps it will endure.
When i go winter camping i have a 24inch saw and a cutting impliment. Mainly cutting 5 to 6 inch and under wood.
Well it is handling as expected. 0.150 stock. 1lb 6 oz. 23.5 inches overall.


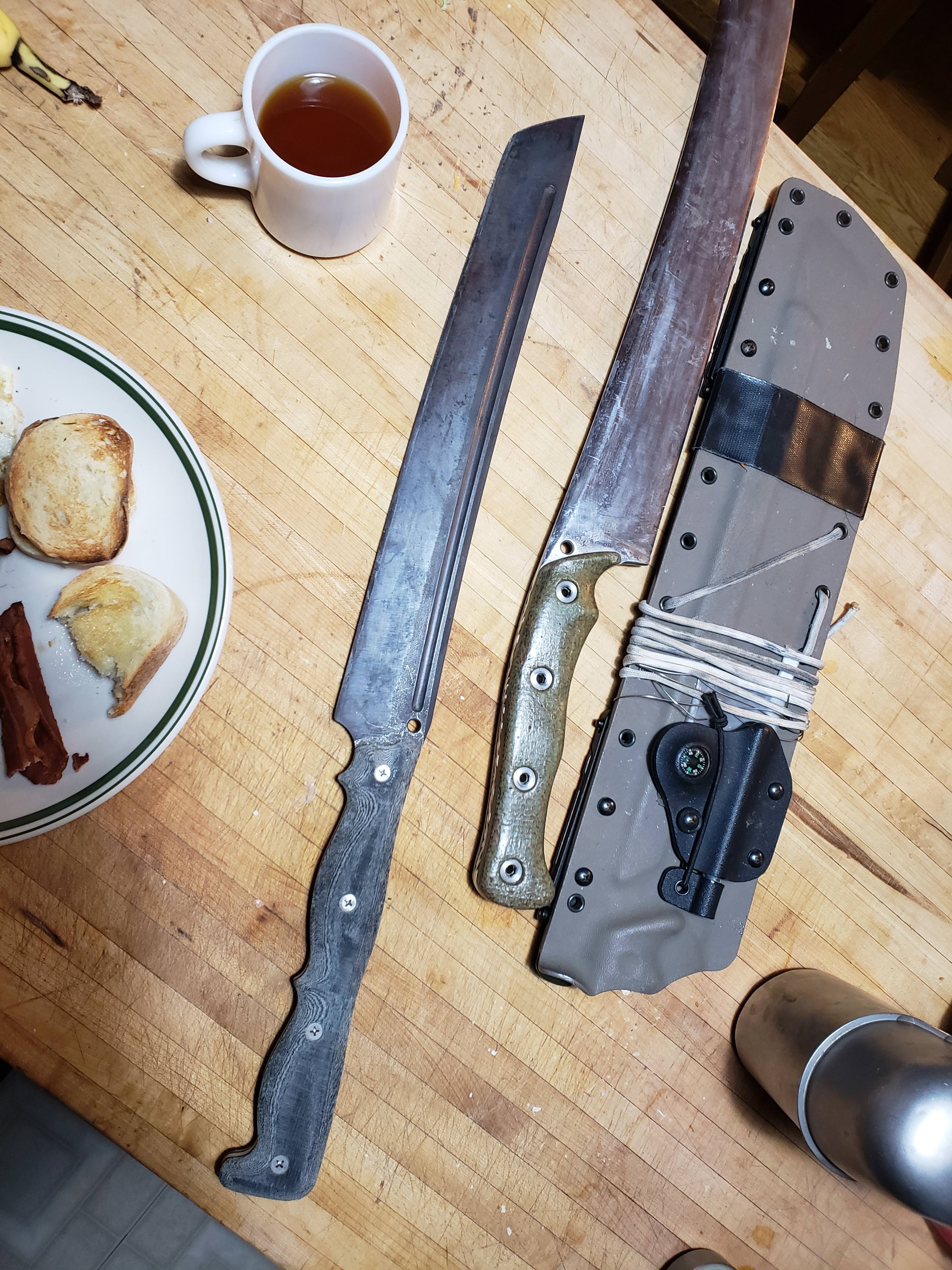