- Joined
- Jul 6, 2024
- Messages
- 18
Hey everyone! I’ve been a long time lurker and finally joined up. I just started bladesmithing literally 3 weeks ago but have been a long time welder, fabricator, and custom chopper motorcycle builder for the past 7 years. I’m not gonna lie, The TV show Forged in Fire is a favorite of mine and I started bladesmithing after years of watching it and just being into metal fabrication in general. Being a natural metal fabricator, bladesmithing just interests the hell out of me so I decided to give it a try.
Of course being the metal fabricator that I am, I decided for my first knife I was going to do a low count Damascus (which I know, is not a starter technique but I’m a go big or go home kind of guy lol) with only 9 layers of 1095 and 15N20.
I also fabricated a press out of a 6 1/2 ton log splitter because even hammering 9- 1/8”thick layers of Damascus is a mother f’er.
So anyways, I built my first knife and here it is. I used 20 mule team borax as flux and a rounded head hammer to set the welds and they welded like I hoped they would. The knife, after grinding, ended up being about only 5 to 6 layers because I got too excited and started grinding it way too thick before I drew it out to the thickness I actually should’ve needed.
Anyways, this is my first knife so take it easy on me. But at the same time I’m here for advice so if you have some for me, please, let er’ rip!
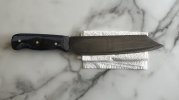
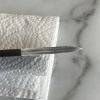
Of course being the metal fabricator that I am, I decided for my first knife I was going to do a low count Damascus (which I know, is not a starter technique but I’m a go big or go home kind of guy lol) with only 9 layers of 1095 and 15N20.
I also fabricated a press out of a 6 1/2 ton log splitter because even hammering 9- 1/8”thick layers of Damascus is a mother f’er.
So anyways, I built my first knife and here it is. I used 20 mule team borax as flux and a rounded head hammer to set the welds and they welded like I hoped they would. The knife, after grinding, ended up being about only 5 to 6 layers because I got too excited and started grinding it way too thick before I drew it out to the thickness I actually should’ve needed.
Anyways, this is my first knife so take it easy on me. But at the same time I’m here for advice so if you have some for me, please, let er’ rip!
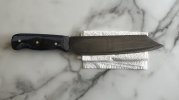
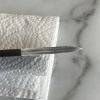