I'm a total newbie to making knives, just finished my first and working on the second. Posting pics because a question I had in the forum, figure this will be a good way to show how much I'm struggling, LOL!
First knife, a little kitchen utility knife in Aldo's 1084, quilted maple handle with red G10 spacers. 9 3/4" OAL, 5 3"/8 blade. I learned a lot and made a lot of mistakes. I already was a fan of rustic looking knives, so now I made one!
Wanting to get better at this means practice and learning more! Second knife I'm working on is a curvy bunkabocho in 1084. First I worked the design in pencil on paper then glued it to thin balsa to make a template and guesstimate how it felt in hand and on cutting board.
It seemed okay, so then I traced the profile onto the 1/8" thick 1084 steel (actual measures more like 0.135-0.140" it seems), rough cut with an 18 tpi bimetal hacksaw blade, then profiled on my 1x30 belt sander with 50 grit zirconia belt except for hard to reach curvy areas which were done by hand filing.
Wanted to have a maker's mark and easiest thing without spending extra money was a file pattern on the handle spine. Colored with sharpie to see what it might look like. As you can see, also sharpied the edges and scribed a center line with 1/8" drill bit.
Drilled out slightly bigger than 1/8" pin holes ("30" size drill bit) and 1/4" weight reduction and epoxy "pin" holes in the tang, maybe should've planned out where the big holes go ahead of time. You can see where I got two of them overlapped. Probably could've done more but the bit is dull and I got impatient. Hand cut wood for the planned handle, walnut for the main part and black palm for the "bolsters". Wavy cuts with a coping saw, LOL.
What got me started on this was a question about gluing up multipart spacers between wood bolster to the rest of the scales. I was almost going to just skip the spacers because I was confident Titebond would make a great bond between the two woods directly, but figured I would learn more if I went for my original vision: metal and G10 spacers inbetween the woods. I hand cut strips of copper and black G10, roughed up the surfaces with the lowest grit sandpaper I had on hand (80? grit). Since I was worried about clamping many pieces up at a time, I decided to try gluing just the spacers together first using epoxy. I used wax paper to because I get epoxy everywhere and didn't want to glue the pieces to the clamps.
The copper and G10 seemed to stick together okay so I planned the scale glue up. More sandpaper roughing then figured a way to clamp everything with the stuff I have on hand. I wrapped wax paper around a 1/4" poplar board I was saving for making sayas then clamped the black palm with angle such that it would hold the other pieces down (because I don't have enough clamps tall enough to clamp the other pieces). The angle would otherwise make the pieces slide with the pressure from the clamps on the side. If I had thought about it enough, I would've made the wood the same height so I could've just clamped everything between a couple of boards top and bottom instead of this convoluted setup.
I do everything at my little breakfast bar table or front porch, so I had my coffee and Sunday brunch around this stuff today.
First knife, a little kitchen utility knife in Aldo's 1084, quilted maple handle with red G10 spacers. 9 3/4" OAL, 5 3"/8 blade. I learned a lot and made a lot of mistakes. I already was a fan of rustic looking knives, so now I made one!
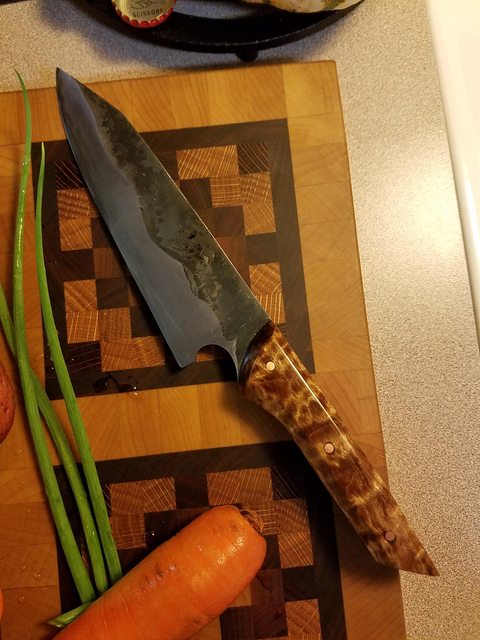
Wanting to get better at this means practice and learning more! Second knife I'm working on is a curvy bunkabocho in 1084. First I worked the design in pencil on paper then glued it to thin balsa to make a template and guesstimate how it felt in hand and on cutting board.






It seemed okay, so then I traced the profile onto the 1/8" thick 1084 steel (actual measures more like 0.135-0.140" it seems), rough cut with an 18 tpi bimetal hacksaw blade, then profiled on my 1x30 belt sander with 50 grit zirconia belt except for hard to reach curvy areas which were done by hand filing.
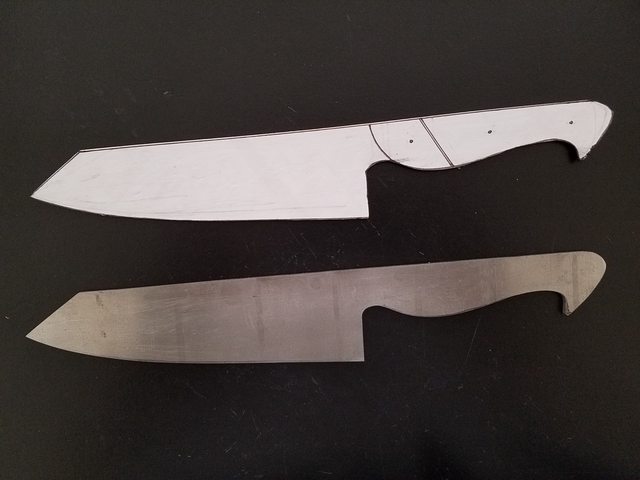
Wanted to have a maker's mark and easiest thing without spending extra money was a file pattern on the handle spine. Colored with sharpie to see what it might look like. As you can see, also sharpied the edges and scribed a center line with 1/8" drill bit.

Drilled out slightly bigger than 1/8" pin holes ("30" size drill bit) and 1/4" weight reduction and epoxy "pin" holes in the tang, maybe should've planned out where the big holes go ahead of time. You can see where I got two of them overlapped. Probably could've done more but the bit is dull and I got impatient. Hand cut wood for the planned handle, walnut for the main part and black palm for the "bolsters". Wavy cuts with a coping saw, LOL.
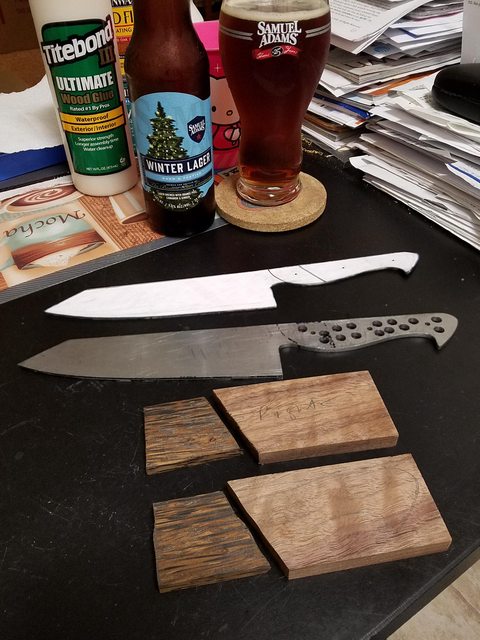
What got me started on this was a question about gluing up multipart spacers between wood bolster to the rest of the scales. I was almost going to just skip the spacers because I was confident Titebond would make a great bond between the two woods directly, but figured I would learn more if I went for my original vision: metal and G10 spacers inbetween the woods. I hand cut strips of copper and black G10, roughed up the surfaces with the lowest grit sandpaper I had on hand (80? grit). Since I was worried about clamping many pieces up at a time, I decided to try gluing just the spacers together first using epoxy. I used wax paper to because I get epoxy everywhere and didn't want to glue the pieces to the clamps.
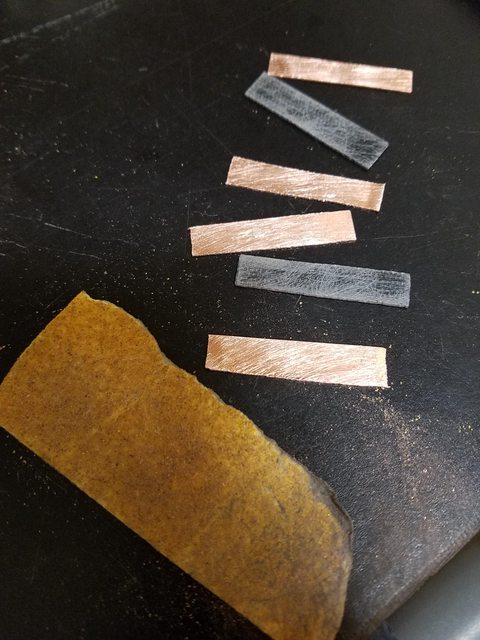
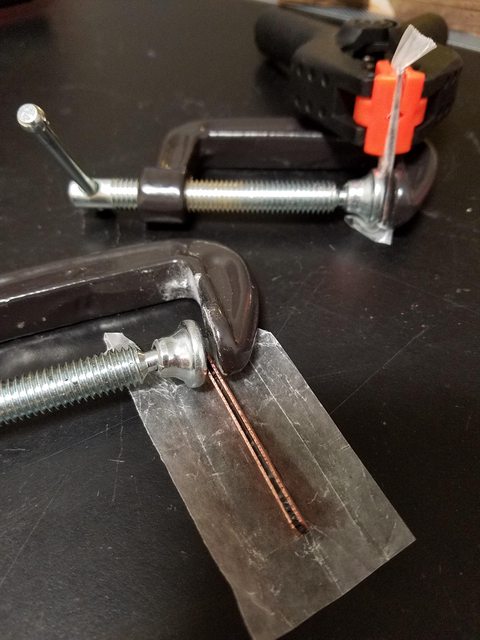
The copper and G10 seemed to stick together okay so I planned the scale glue up. More sandpaper roughing then figured a way to clamp everything with the stuff I have on hand. I wrapped wax paper around a 1/4" poplar board I was saving for making sayas then clamped the black palm with angle such that it would hold the other pieces down (because I don't have enough clamps tall enough to clamp the other pieces). The angle would otherwise make the pieces slide with the pressure from the clamps on the side. If I had thought about it enough, I would've made the wood the same height so I could've just clamped everything between a couple of boards top and bottom instead of this convoluted setup.
I do everything at my little breakfast bar table or front porch, so I had my coffee and Sunday brunch around this stuff today.

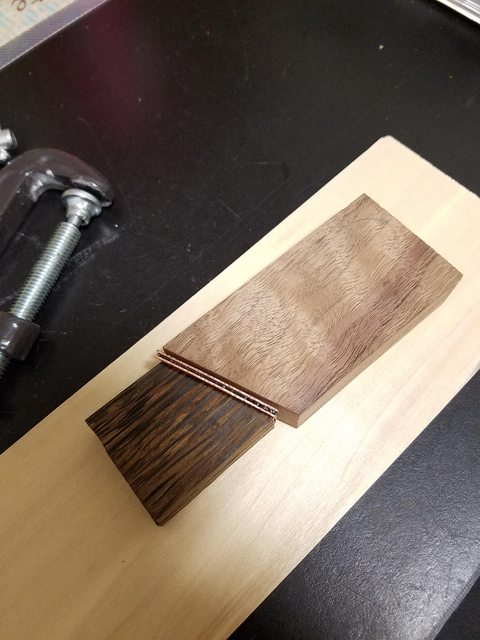
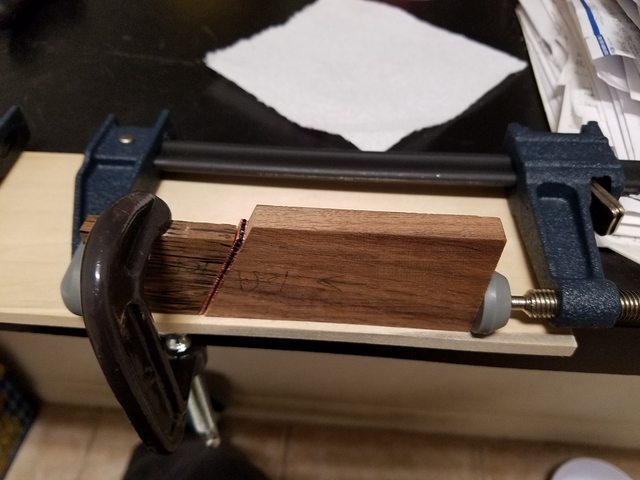

Last edited: