- Joined
- Dec 24, 2016
- Messages
- 3,380
A local guy has a couple Paragon electric kilns that he is looking to sell. He knows NOTHING about them(I honestly don't much more than him). He got them cleaning out a couple buildings. He does not I know if they are in working order. I may be able to bring them to my shop and plug them in.
I'm a hobbiest bladesmith at best and have been heat treating in my forge on a wing and a prayer. I've had grain growth issues before and hoping to fine tune that some what.
If you have any thoughts suggestions on these kilns and a working & non working value would be greatly appreciated. Also any recommendations on what might need to be added to them.
Thank you
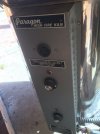
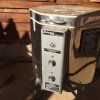
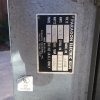
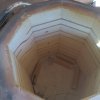
I'm a hobbiest bladesmith at best and have been heat treating in my forge on a wing and a prayer. I've had grain growth issues before and hoping to fine tune that some what.
If you have any thoughts suggestions on these kilns and a working & non working value would be greatly appreciated. Also any recommendations on what might need to be added to them.
Thank you
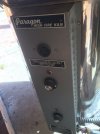
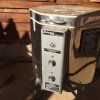
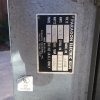
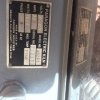
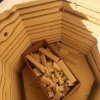
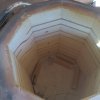