I just ran a "test" and something isn't wired right, so I have a few more questions:
First off, I noticed that ASCO NC valves got warm as they were opened. I think this is normal because of the current running through them to keep them open, but just checking if this is somethin
You might also try reversing the polarity on your thermocouple, as a test. I wired mine up the wrong way and the PID just wouldn't turn on.
Thanks for the suggestion, but I don't think it's the thermocouple, because it seemed to read the temp correctly. (According to the instruction manual, if one wires the thermocouple backwards, the reading will go down as the temp increases.)
Here's what I did for a test: I used a space heater in the forge to modify the temps to see if I could get the high flow valve to click on/off when on AUTO. The temp in the garage this morning was 51 degrees. Following the instruction manual, I set the following parameters:
Proportional Constant : 0.1 (Type K control range is 1500 C, so 0.1 should be 1.5 C or 2.7 F)
Integral time : 2 sec
Derivative time: 20 sec (factory setting)
Damp constant: 0.2 (factory setting)
Cycle rate: 2 sec (factory setting)
Digital filter: 0 (factory setting)
Target Temp: 65
I turned the space heater on and the temp got up to 100deg and nothing happened with high flow valve. I then put the thermocouple between a couple of ice pack to get it back down to 50 degrees, and still nothing.
In the alarm setting instructions, it says: "The J1 relay is controlled by parameters AH1 and AL1 and the J2 relay is controlled by parameter AH2 and AL2." Also the terminal wiring diagram says that J1 terminals are 3,4,5 and the J2 terminals are 11, 13, 14. I have nothing connected to either of these, and think that's the problem, but I'd like some input before re-wiring.
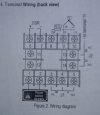
If you look back to the wiring diagram, I have the DPDT wired to the SSR which is what I was told, (that didn't and still doesn't make sense to me) but I'm wondering if this should be connected to the J1 terminals...