I hope everybody had a great Easter! I'm really glad you guys enjoy the process, there is still a long way to go but hopefully things will start make sense as I go along.
I've decided to work on all five knives at the same time or at least for most of the steps. I will not post each step from each knife because it will be repetitive. I will try however to capture all the steps of the way. I'm pointing this out because you may notice different knives from one step to another or different finishes written on the blades and might be confusing.
Since I've began the final grind on all the blades, I decided to sand the flats a little bit. Not a lot, just enough with 180grit to remove the surface grinder 120grit scratches.
Ever since I got a laptop with netflix into the workshop , sanding has been a joy.
So far, all of them have a sanded 180grit finish on the flats and a 60grit on the bevels. I'm trying a new process for the final grind and I think I will stick with it.
This is my new process:
1) 60grit to remove the bulk of the material.
2) 120grit to refine the scratch pattern and get close to my final thickness.
3) 240grit to take off all the deep scratches
4) insert a carbide file guide and with a 120grit on my waterfall platen even up the plunge lines.
5) refine the scratch pattern and plunges with a 400grit.
This is my waterfall platen, I wil definitely need a better motor on my grinder because mine has no torque and it's really easy to stop it with this configuration. Luckily, slowly but surely it works for now.
With the table square to the platen, I can check whether the plunges are indeed even. The two little tabs make it really easy to spot any unevenness.
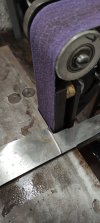
And here it is with the choil compeltely ground. I'm pretty happy with the result on the plunges. As a point of reference, the edge in the zoomed picture bellow is a little less than 20thou. Other than a very zoomed in view, there is another way to check for symmetry later on.
The first knife I decided to work on was a small-ish fighter/big chonky EDC. I quickly took it to a dirty 400grit and set it aside to work on the next one.
The next one was a fighter. I pretty much followed the same steps as the previous one.
A major step I forgot to mention earlier was to check the tip centricity and that my distal taper is even (yes, you may have a centered tip but an uneven distal taper)
There are many ways to check the tip centricity, a dirty and easy way is with a 123 block and a stable can.
Lay the blade flat on the ricasso on a 123 block, scratch the can, flip and scratch again, the two scratches should line up.
A more accurate way is with a height gauge.
Same as before, lay the blade on a 123block and with the height gauge go until it barely glazes over the tip. Once there, zero the dial and flip the blade.
A perfectly centered tip should glaze the same way on both sides without any adjustments on the height gauge. If it's not centered, the dial will show how off the tip is and which side should be ground to fix it.
Here is a video of this process from an older knife, as you can see this one was 0.1mm off center.
A flat and parallel ricasso is a must for both to work, if the ricasso is not parallel, the measurements will be all over the place.

For the taper, things are much easier. Three scribe lines on the spine will reveal any uneveness.
My picture does not capture correctly what I want to show, therefore I made one in paint.
A center line and two more near the edge of the spine are all that it's required. With an even taper, the two outer scribe lines end in the same plane (cyrcled areas).
If you notice closely, you can see the two scribe lines terminating at the same plane.
That's it for today's update. I will have more to show within the week.