- Joined
- Apr 19, 2012
- Messages
- 8,099
Greetings BF!
I, thanks to advise here, can now sharpen a knife reasonably well. However, I have a couple of questions and have found only conflicting information.
1. Is there a benefit in terms of edge holding to take a knife to a polished edge?
2. What is the point of "diminishing returns" where you are just further refining an edge but really not getting any sharper, instead you are only wasting time and metal. Or....making the knife lose its edge holding length of time for really keen cutting for a short amount of time.
Here is the reason I am asking, with pictures to help.
Here is a knife that I sharpened to 600 grit, then stropped the burr off. Quite sharp and I really like the matte finish the edge has.
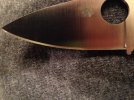
Below is a knife that I just sharpened to about 8000 grit (3 micron). It is razor sharp but I really don't like the hazy look to the edge. (The pic does not really show well but the edge looks like a fogged mirror)
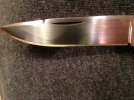
* so here is my real question I guess: Should I leave my knives at 600 grit and burr free or go up to about 1 micron where I can get a more polished looking edge? If there is a benefit I don't have a problem buying the additional materials and going up through more grits, but I don't want to waste time, money, and metal for little benefit. If it is better to go for the polished edge, where do I stop? 1 micron, .5 micron?
any and all help/links are greatly appreciated!
I, thanks to advise here, can now sharpen a knife reasonably well. However, I have a couple of questions and have found only conflicting information.
1. Is there a benefit in terms of edge holding to take a knife to a polished edge?
2. What is the point of "diminishing returns" where you are just further refining an edge but really not getting any sharper, instead you are only wasting time and metal. Or....making the knife lose its edge holding length of time for really keen cutting for a short amount of time.
Here is the reason I am asking, with pictures to help.
Here is a knife that I sharpened to 600 grit, then stropped the burr off. Quite sharp and I really like the matte finish the edge has.
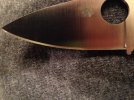
Below is a knife that I just sharpened to about 8000 grit (3 micron). It is razor sharp but I really don't like the hazy look to the edge. (The pic does not really show well but the edge looks like a fogged mirror)
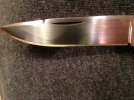
* so here is my real question I guess: Should I leave my knives at 600 grit and burr free or go up to about 1 micron where I can get a more polished looking edge? If there is a benefit I don't have a problem buying the additional materials and going up through more grits, but I don't want to waste time, money, and metal for little benefit. If it is better to go for the polished edge, where do I stop? 1 micron, .5 micron?
any and all help/links are greatly appreciated!