- Joined
- Sep 28, 2014
- Messages
- 693
Howdy Y’all,
I am working on my very first sheath project, and I figured that, before I start cutting leather, I would ask some of you who have a lot more experience to look over my shoulder in the design phase.
The knife is a Nessmuk that I made a few months back from a Green River buffalo skinner blank. My plan is to make the sheath from 7/8 oz. Hermann Oak veg tan, rough out. (I intend to really take this knife into the woods and use it, and I like how a rough out sheath shows less wear with hard use.)
I made a pattern from craft foam. (Don’t judge my pink foam, it was on hand!) I realized, after looking at it, that I need to extend the welt up to the top of the pouch (duh). Also, the belt loop will need to be longer, but I ran out of foam.
Other than that, I would really appreciate any critiques on the design, to help me avoid any unanticipated road blocks.
Do I assume correctly that 7/8 oz., being thicker than craft foam, will “come up short” when folded over on this pattern? I figure I can use my divider to scratch the pattern out a little “fat” and then trim as needed. I started to glue two sheets of foam together, but I didn’t have enough, and I’m snowed in today (hence the leather project.)
Thanks in advance for your help!
I am working on my very first sheath project, and I figured that, before I start cutting leather, I would ask some of you who have a lot more experience to look over my shoulder in the design phase.
The knife is a Nessmuk that I made a few months back from a Green River buffalo skinner blank. My plan is to make the sheath from 7/8 oz. Hermann Oak veg tan, rough out. (I intend to really take this knife into the woods and use it, and I like how a rough out sheath shows less wear with hard use.)
I made a pattern from craft foam. (Don’t judge my pink foam, it was on hand!) I realized, after looking at it, that I need to extend the welt up to the top of the pouch (duh). Also, the belt loop will need to be longer, but I ran out of foam.
Other than that, I would really appreciate any critiques on the design, to help me avoid any unanticipated road blocks.
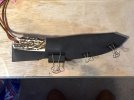
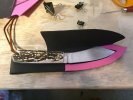
Do I assume correctly that 7/8 oz., being thicker than craft foam, will “come up short” when folded over on this pattern? I figure I can use my divider to scratch the pattern out a little “fat” and then trim as needed. I started to glue two sheets of foam together, but I didn’t have enough, and I’m snowed in today (hence the leather project.)
Thanks in advance for your help!