All horn is
keratin -- basically compact hair. Because of the fibrous nature it is strong and resists breaking or bending. That is good for the mountain goat but creates a problem for the knifemaker.
Cow horn and buffalo horn (which is really a water buffalo horn) shape easier than goat and sheep horn.
They are rather soft, and best used for decorative frontier crafts. It was used on cheap pocketknives before synthetics. Those knives were not meant to last long.
Sheep/Ram/Goat horn is tougher. Along with tortoise shell, it was a popular material for folder handles long ago. Synthetics replaced them.
It needs to be flattened by heating and pressing flat in clamped plates. Warping is a big issue in preparing them.
I asked Ed Fowler how he did his horn scales about 25 years ago, and he gave me the phone number of a friend of his who he said was the "Ram's Horn Whisperer".
His friend told me several methods, including boiling, heating in sand, and heating in clamps ... and said, "Try 'em all and see what works for you."
I eventually came up with this procedure:
Cut the horn up into suitable size pieces.
Bil the horn for 2 to 4 hours.
P Immediately put the horn between clamped plates, tighten just enough to flatten a bit hold things firmly in place. Don't try to flatten all the way yet. Set the assembly in the oven at 250°F.
After an hour, tighten the clamps every 15 minutes for a couple more hours. Again, just tighten until snug each time. Don't do too much per heat. When it is flat and doesn't snug down anymore, take out of the oven and let sit clamped overnight to cool.
Take the horn slabs out of the plates and let sit for several days to a couple weeks. If they warp again, repeat the clamping/heating. It may take a higher temperature for some onery material. (I have gone as high as 300°F.)
Sand the scales to thickness from the back side first, avoiding heat. Clamp between flat boards when storing or not currently working on the knife.
Use headed pins or bolts and strong glue. Sand slowly in the final shaping/fitting of the top side ... avoid heat!
This works well for Sheep and Goat horn as well as Musk Ox.
Cow and Watter Buffalo horn can be softened by boiling in water for a couple hours and clamping between metal or wooden boards. It may need a couple boil/clamp cycles to stay flat. While soft it can be shaped into utilitarian objects by clamping in wooden molds and forms. You can make bowls, spoons, drinking cups with shaped handles, combs, bracelets and jewelry, etc. this way. There are many books on buckskinner and pioneer crafts that show the possibilities and some techniques.
Another trick I have read but not tried is soaking the cut up horn pieces in household ammonia for a couple weeks before boiling. It supposedly softens the keratin, making it more pliable.
Fun trivia fact:
Some older people grow one or more little curved horns on their face and other places on the body. These are often around the eyes, and sometimes on the forehead. These are called cutaneous horns, and are true horns are made from keratin. They normally grow out of a large wart, making it look even more horrible. They are not usually over 10mm long, but occasionally grow over 200mm. You can imagine how people in the dark ages felt about an old lady/man who had a horn on his/her head.
Some people have had dozens of horns, even hundreds, that regrow just like a cow horn does and need constant yearly trimming.
Look up "Tree man of Indonesia" for how bad a similar form of this can get in the extreme. He had gigantic tree bark hands.
Below is one of these horns on an old Chinese lady's forehead (real medical photo)
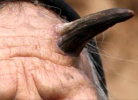