Hengelo_77
Basic Member
- Joined
- Mar 2, 2006
- Messages
- 6,221
I want to learn to solder bolsters on to liners (slipjoints)
I've made several test pieces and as you can see without good result.
It is stainless steel, the solder I have is 4%Ag and I have special stainless flux.
I've sanded the steel to either 180/240/400 grit and cleaned with alcohol or acetone.
I put a layer of flux on the steel, either as much as the brush leaves behind or half that.
I flatten the solder, clean it with a fine file, clean it with acetone and even clean the tweezers I use to put the solder on the steel with acetone. I use as much(or little) as Steve Culver shows in his slip joint book.
A few times I put a little flux over the pieces of solder but not always.
I try to heat slowly from below with a small flame (crème brûlée burner) have 4" to 6" distance between the burner and the steel and I move it around.
The flux bubbles and creates a foam like substance before the solder melts.
I have a piece of sharpened Ti roundstock to try and spread the liquid solder.
I just don't get it to flow properly.
Sometimes it forms small balls. That means it preferst to adhere to itself over adhering to the steel.
Other times it melts but hardly spreads. I try not to burn the flux then but sometimes it turns brown.
Here are some photo's of my test pieces.
What am I doing wrong?
Am I using to little solder? Is my flux bad?
My flux is a few years old but all shops are closed today over here.
I also tried a paintstripper but I don't get it hot enough to melt the solder.
I've made several test pieces and as you can see without good result.
It is stainless steel, the solder I have is 4%Ag and I have special stainless flux.
I've sanded the steel to either 180/240/400 grit and cleaned with alcohol or acetone.
I put a layer of flux on the steel, either as much as the brush leaves behind or half that.
I flatten the solder, clean it with a fine file, clean it with acetone and even clean the tweezers I use to put the solder on the steel with acetone. I use as much(or little) as Steve Culver shows in his slip joint book.
A few times I put a little flux over the pieces of solder but not always.
I try to heat slowly from below with a small flame (crème brûlée burner) have 4" to 6" distance between the burner and the steel and I move it around.
The flux bubbles and creates a foam like substance before the solder melts.
I have a piece of sharpened Ti roundstock to try and spread the liquid solder.
I just don't get it to flow properly.
Sometimes it forms small balls. That means it preferst to adhere to itself over adhering to the steel.
Other times it melts but hardly spreads. I try not to burn the flux then but sometimes it turns brown.
Here are some photo's of my test pieces.
What am I doing wrong?
Am I using to little solder? Is my flux bad?
My flux is a few years old but all shops are closed today over here.
I also tried a paintstripper but I don't get it hot enough to melt the solder.
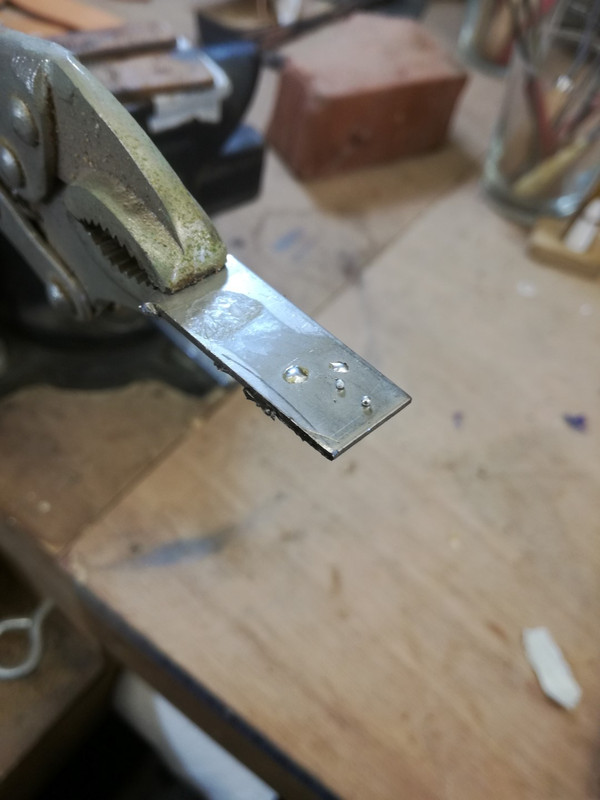
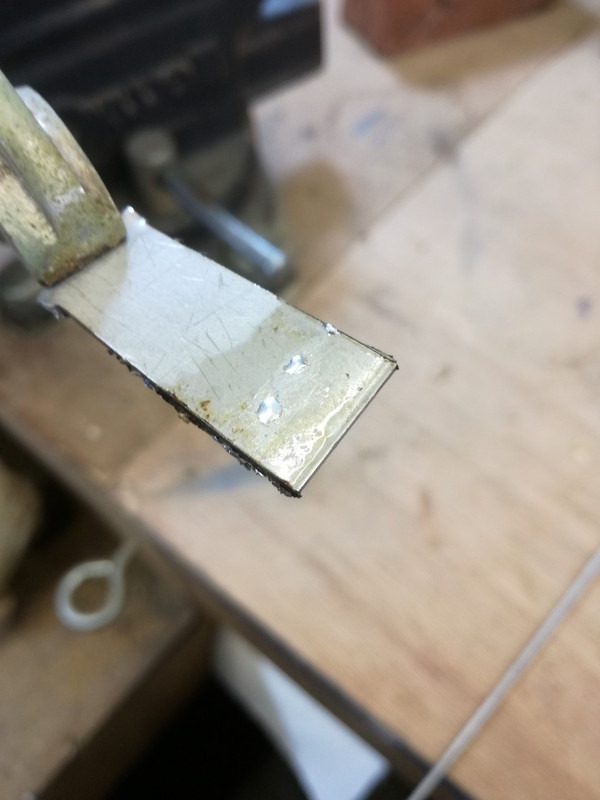
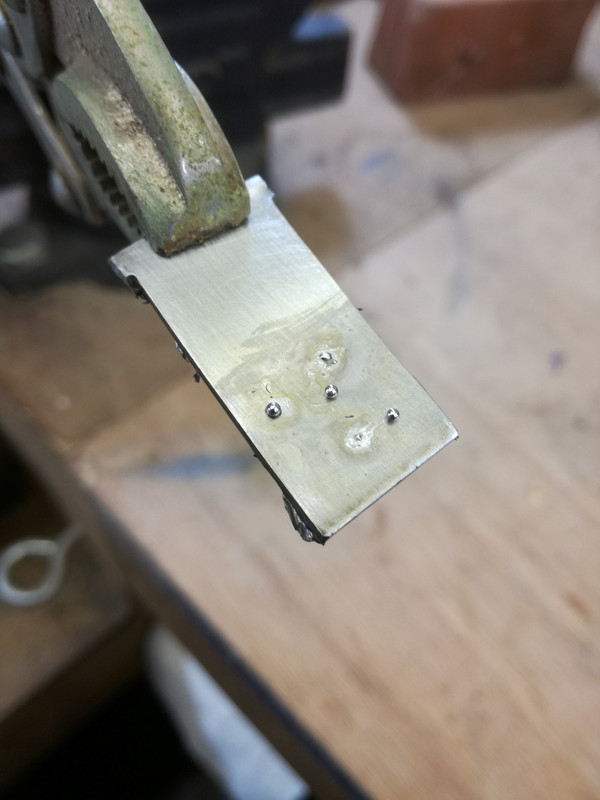
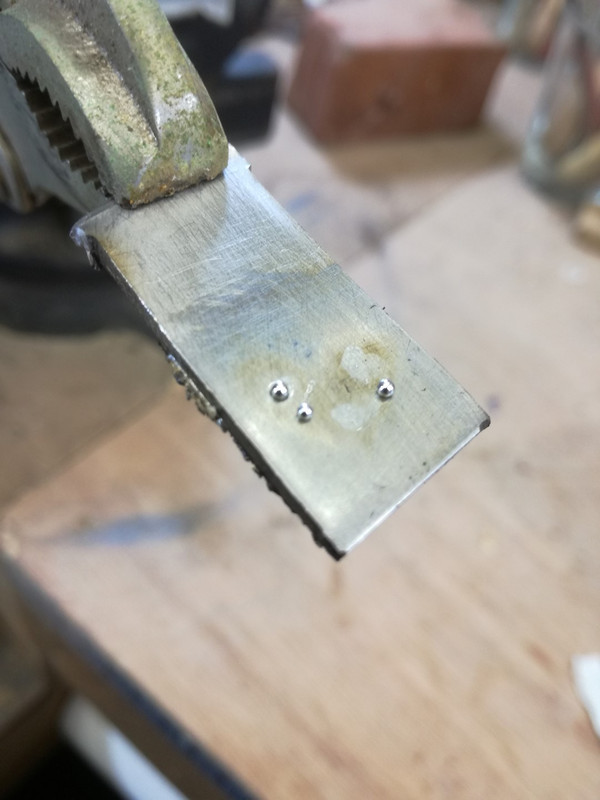
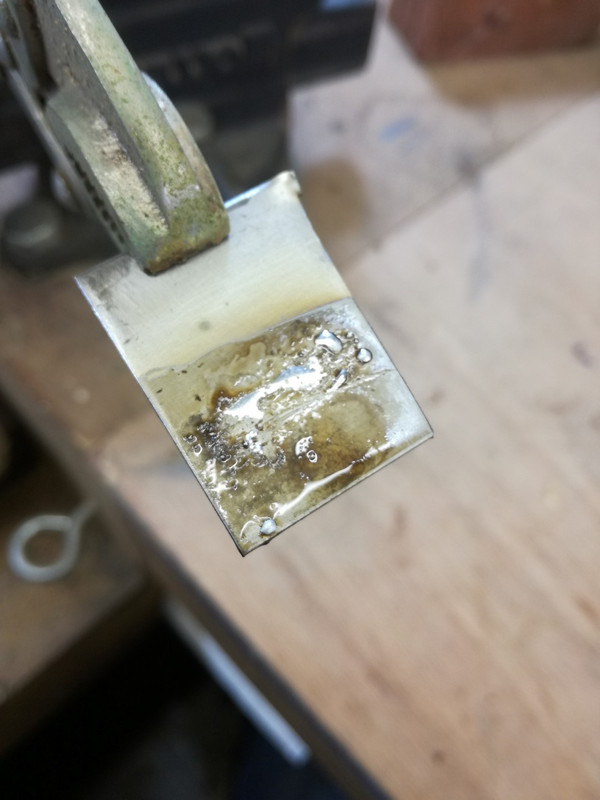

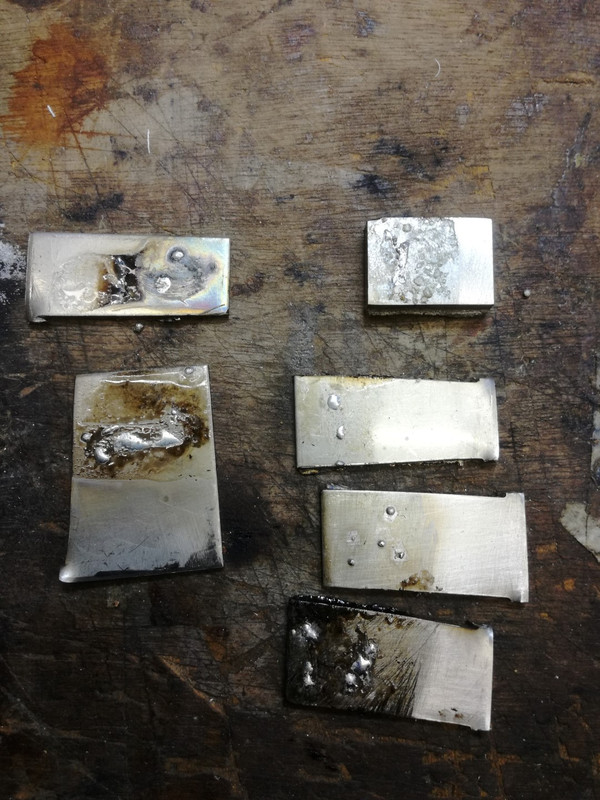