- Joined
- Jun 3, 2019
- Messages
- 2,714
A recent thread commenting that spark bongs can be effectively made from plastic buckets started me off on making one (which I have wanted to do for a while, but procrastinated because I thought I needed to use a metal can). so .... a Home Depot bucket with hole cut out in the lid for a length of 5" steel duct:
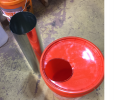
Said duct inserted into bucket with 6" heat register and reducer down to 5"(I will add a big pipe clamp later around the pipe to maintain appropriate height relative to the grinder and bottom of the bucket, and to make it adjustable
):
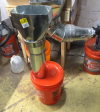
The outlet, to be added later on the right side of the bucket will be 2" PVC with a run to the dust deputy just visible on the right of the photo.
HERE IS THE QUESTION: previous plans call for a divider between the inlet and outlet running from the bottom of the bucket to within a few inches of the top. Previous comments have been to make that divider out of sheet metal. Probably stupid question, but.... ==> where on earth do you get a small quantity of sheet metal like that????? I have looked at my local hardware store, and Home depot, and see none at all. Any ideas???
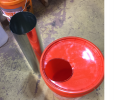
Said duct inserted into bucket with 6" heat register and reducer down to 5"(I will add a big pipe clamp later around the pipe to maintain appropriate height relative to the grinder and bottom of the bucket, and to make it adjustable
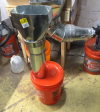
The outlet, to be added later on the right side of the bucket will be 2" PVC with a run to the dust deputy just visible on the right of the photo.
HERE IS THE QUESTION: previous plans call for a divider between the inlet and outlet running from the bottom of the bucket to within a few inches of the top. Previous comments have been to make that divider out of sheet metal. Probably stupid question, but.... ==> where on earth do you get a small quantity of sheet metal like that????? I have looked at my local hardware store, and Home depot, and see none at all. Any ideas???