- Joined
- Dec 27, 2013
- Messages
- 10,043
A few years back, I was tasked with making a big blade out of the titanium turbine blade from the engine of a C5 Galaxy. The blade was made, then sent back with a welded pommel piece. It was then heat-treated and left with oxide intact. It seems this unique blade will now be further modified with engraving work.
Here's the story for those who haven't seen it.
https://www.bladeforums.com/threads/turbine-blade.1422717/
Hello knife fans,
Here's an unusual long-term project that's recently been "finished," a chopper made from a jet turbine engine's titanium alloy intake blade.
OAL is about 29"
This was one of those projects where I didn't know what to expect, and it never seemed to be done. Only when I was finishing wrapping the grip, did it become apparent how I could have really completed it. Gonna have to put some more attention into this piece in the future.
It all began when a suspicious and ominous package arrived, containing this:
A cast titanium fan blade from a C-5 Galaxy. According to my sources, this is alpha-beta titanium alloy 6-4-2-4, similar to Ti6Al2Sn4Zr2Mo, but more juiced up. This is basically 6al4v (grade 5) on steroids and pounding protein shakes. Hooray, a new titanium alloy to try, and it's even sort of flat already! What could go wrong?
The metallurgists who designed the alloy did a good job - its properties are just what you would want in a turbine blade: very rigid but able to flex, slick and hard-surfaced, yet gummy and resistant to crack propagation. If a bird was going to get sucked into a turbine engine, I'd hope the blades are like this one.
It took NINE German-made reinforced cut-off wheels to get through this blade. It is tough.
The twisted blade piece needed to be flattened. This metal was just obscenely, staggeringly hard to forge. I threw everything I had at it, and eventually it became impossible to continue until I got a real trip hammer running.
Drawing out the boss end into a tang was surprisingly quick once I got it under a Little Giant 50#.
Grinding was a pretty much normal ti pain in the ass. However, this alloy releases a ghastly, poisonous-smelling gas when it's ground. Even a full-on charcoal gas mask couldn't block it out all the way. It makes me appreciate the non-poisonous ti-nb beta alloy I normally work with even more.
Straightening.
The blade was convex-ground to zero along its length. It is quite thick by the guard, and tapers rapidly toward the tip.
Apparently it looks like a "falkri," or falcata-kukri, haha.
Thanks for looking.
It was quite a project, and much was learned.
-------
"Update! Just got it back from Sam, heat treated/pommel added/balance adjusted...and it's freaking awesome!" -WValtakis
~Chip
------
Looking forward to seeing how it looks after engraving.
Here's the story for those who haven't seen it.
https://www.bladeforums.com/threads/turbine-blade.1422717/
Hello knife fans,
Here's an unusual long-term project that's recently been "finished," a chopper made from a jet turbine engine's titanium alloy intake blade.
OAL is about 29"

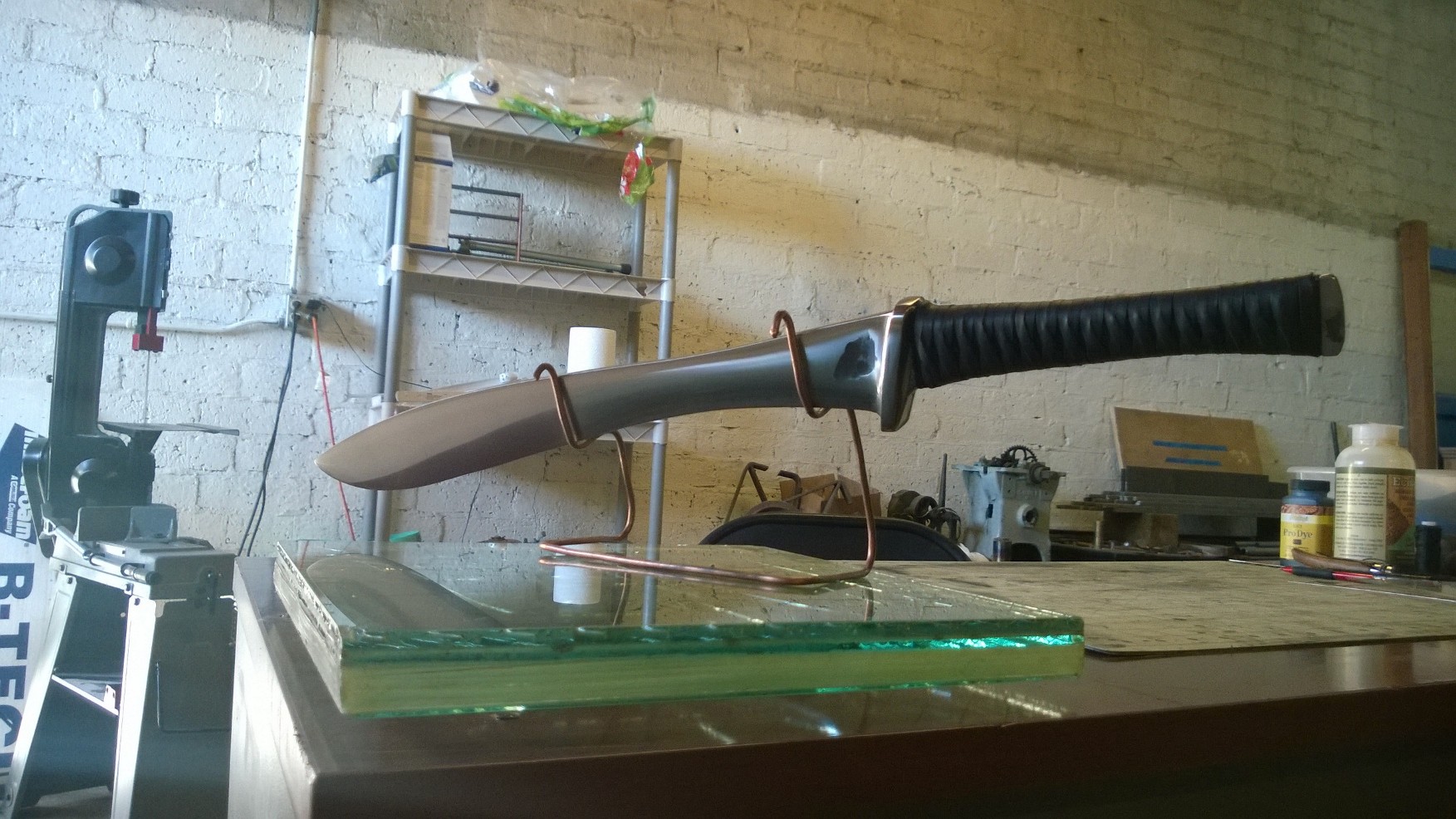
This was one of those projects where I didn't know what to expect, and it never seemed to be done. Only when I was finishing wrapping the grip, did it become apparent how I could have really completed it. Gonna have to put some more attention into this piece in the future.
It all began when a suspicious and ominous package arrived, containing this:
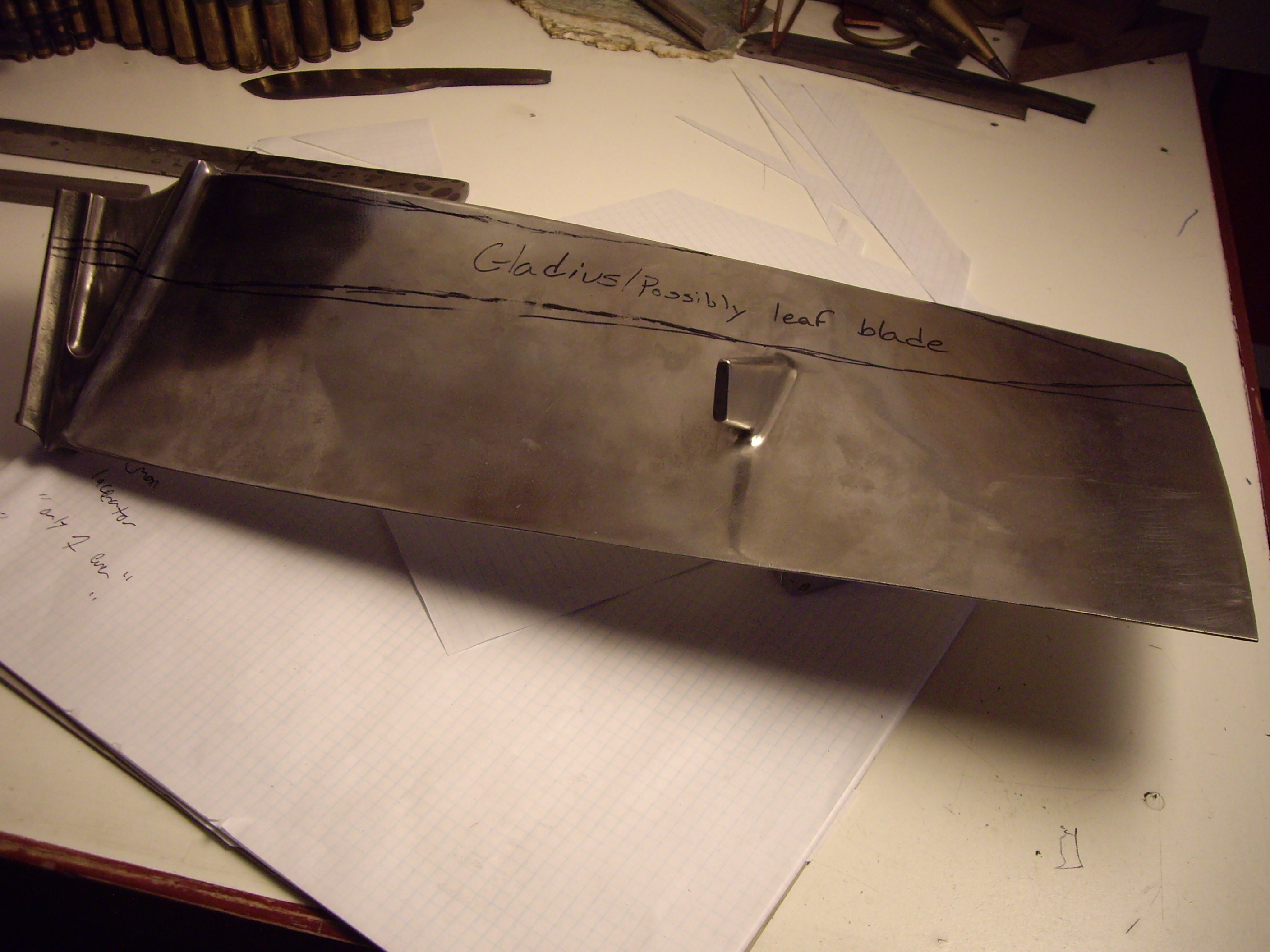
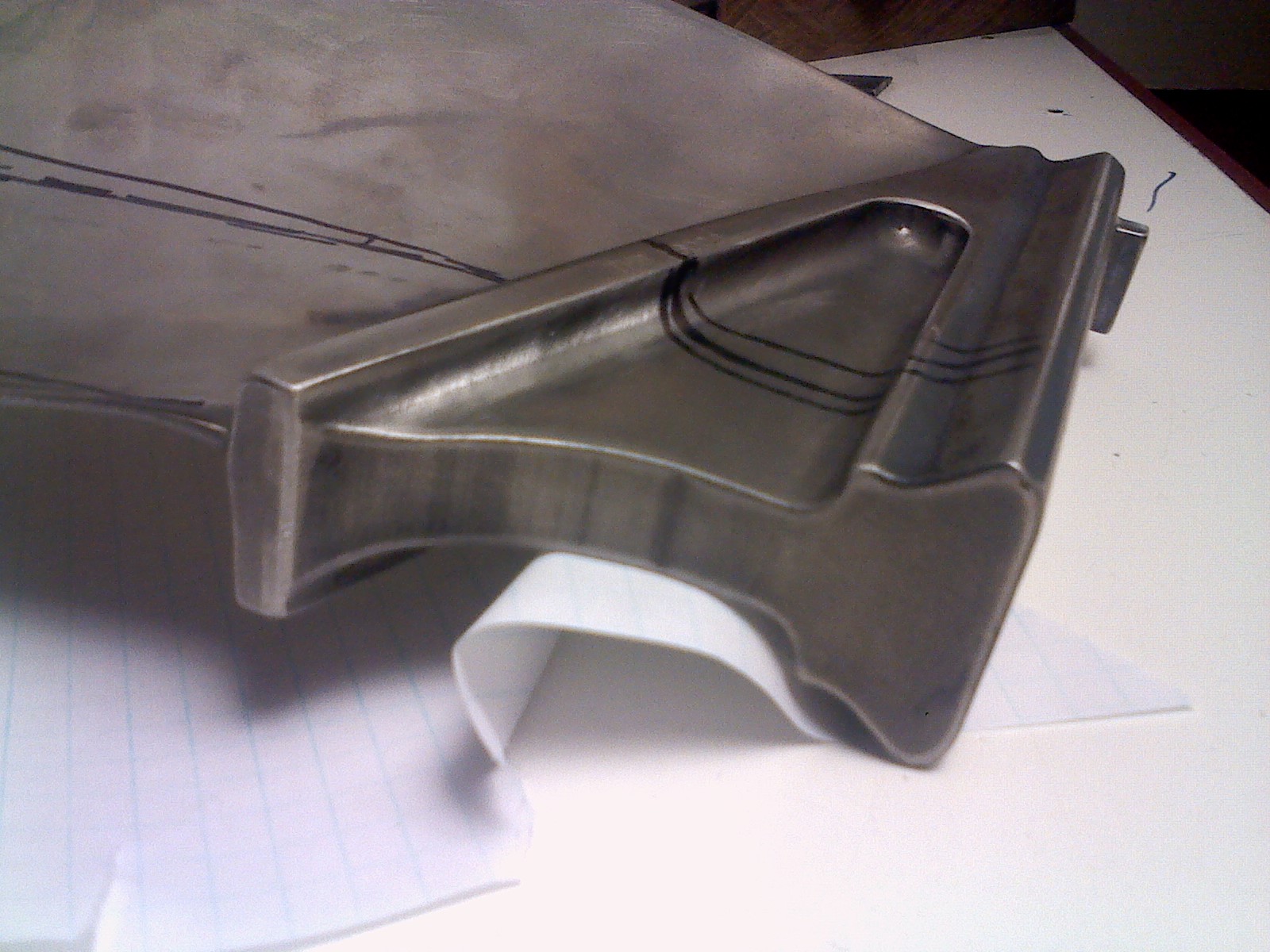
A cast titanium fan blade from a C-5 Galaxy. According to my sources, this is alpha-beta titanium alloy 6-4-2-4, similar to Ti6Al2Sn4Zr2Mo, but more juiced up. This is basically 6al4v (grade 5) on steroids and pounding protein shakes. Hooray, a new titanium alloy to try, and it's even sort of flat already! What could go wrong?

The metallurgists who designed the alloy did a good job - its properties are just what you would want in a turbine blade: very rigid but able to flex, slick and hard-surfaced, yet gummy and resistant to crack propagation. If a bird was going to get sucked into a turbine engine, I'd hope the blades are like this one.
It took NINE German-made reinforced cut-off wheels to get through this blade. It is tough.
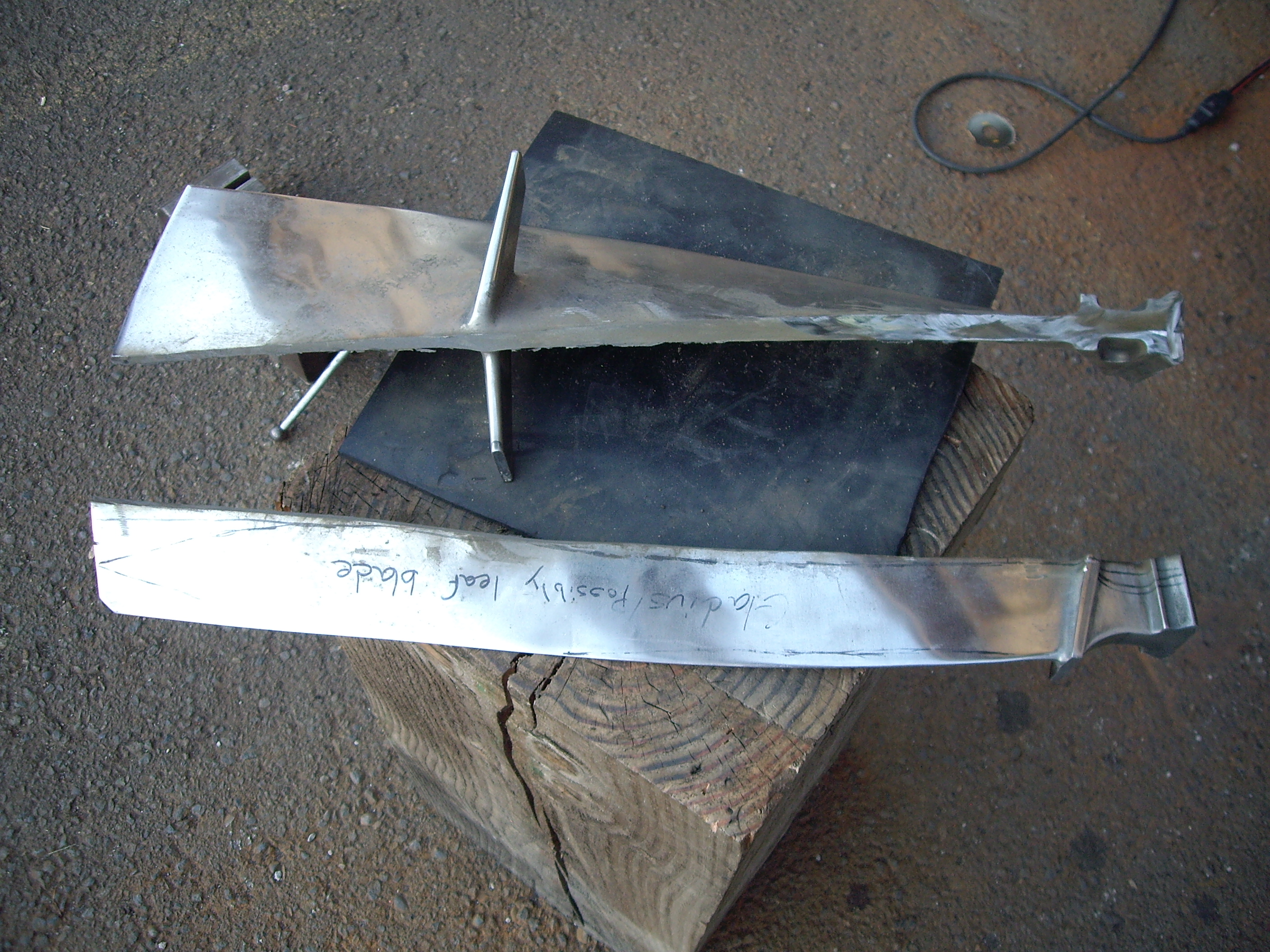
The twisted blade piece needed to be flattened. This metal was just obscenely, staggeringly hard to forge. I threw everything I had at it, and eventually it became impossible to continue until I got a real trip hammer running.
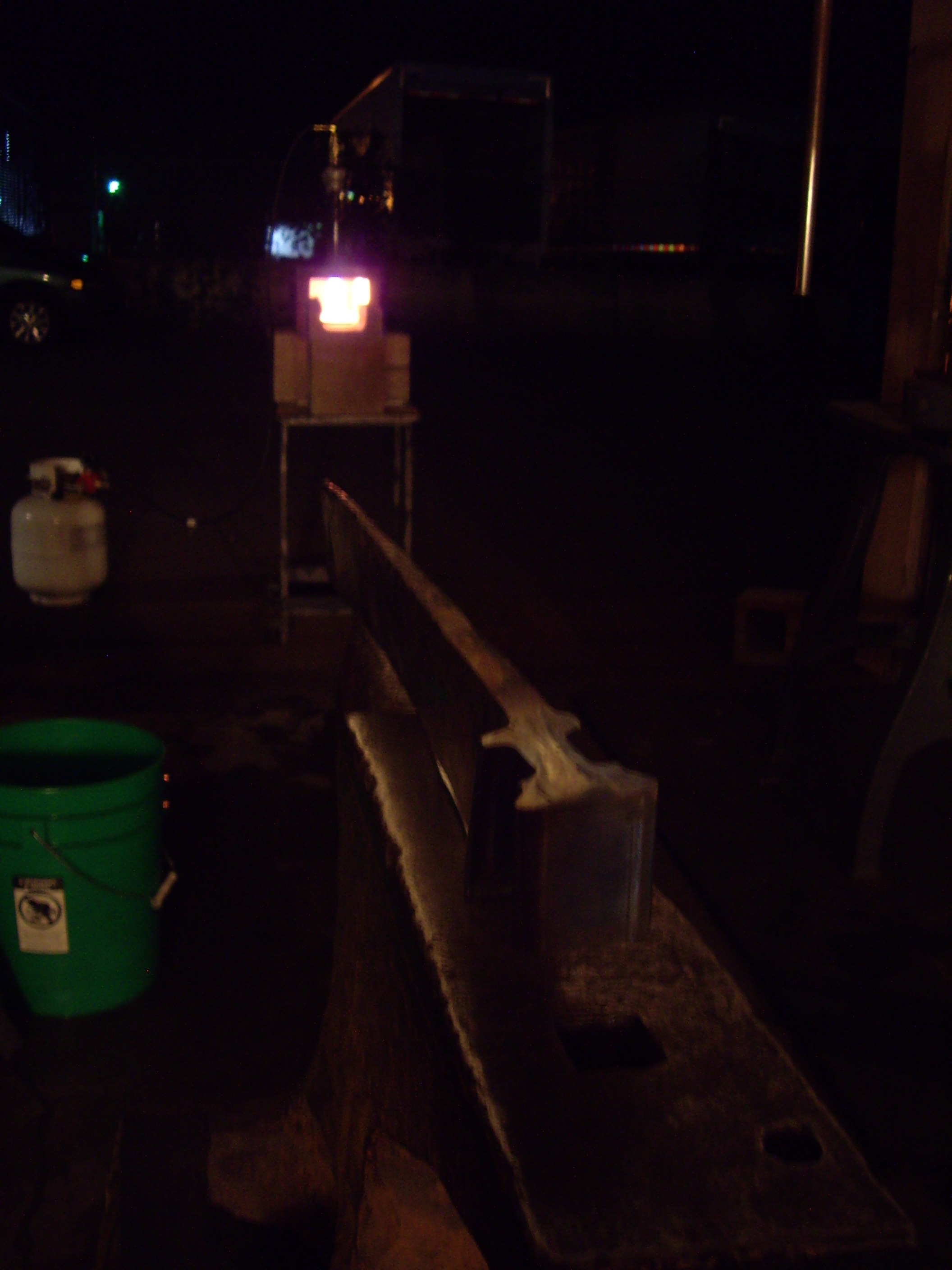
Drawing out the boss end into a tang was surprisingly quick once I got it under a Little Giant 50#.
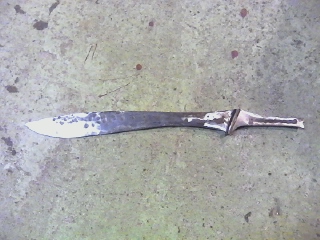
Grinding was a pretty much normal ti pain in the ass. However, this alloy releases a ghastly, poisonous-smelling gas when it's ground. Even a full-on charcoal gas mask couldn't block it out all the way. It makes me appreciate the non-poisonous ti-nb beta alloy I normally work with even more.
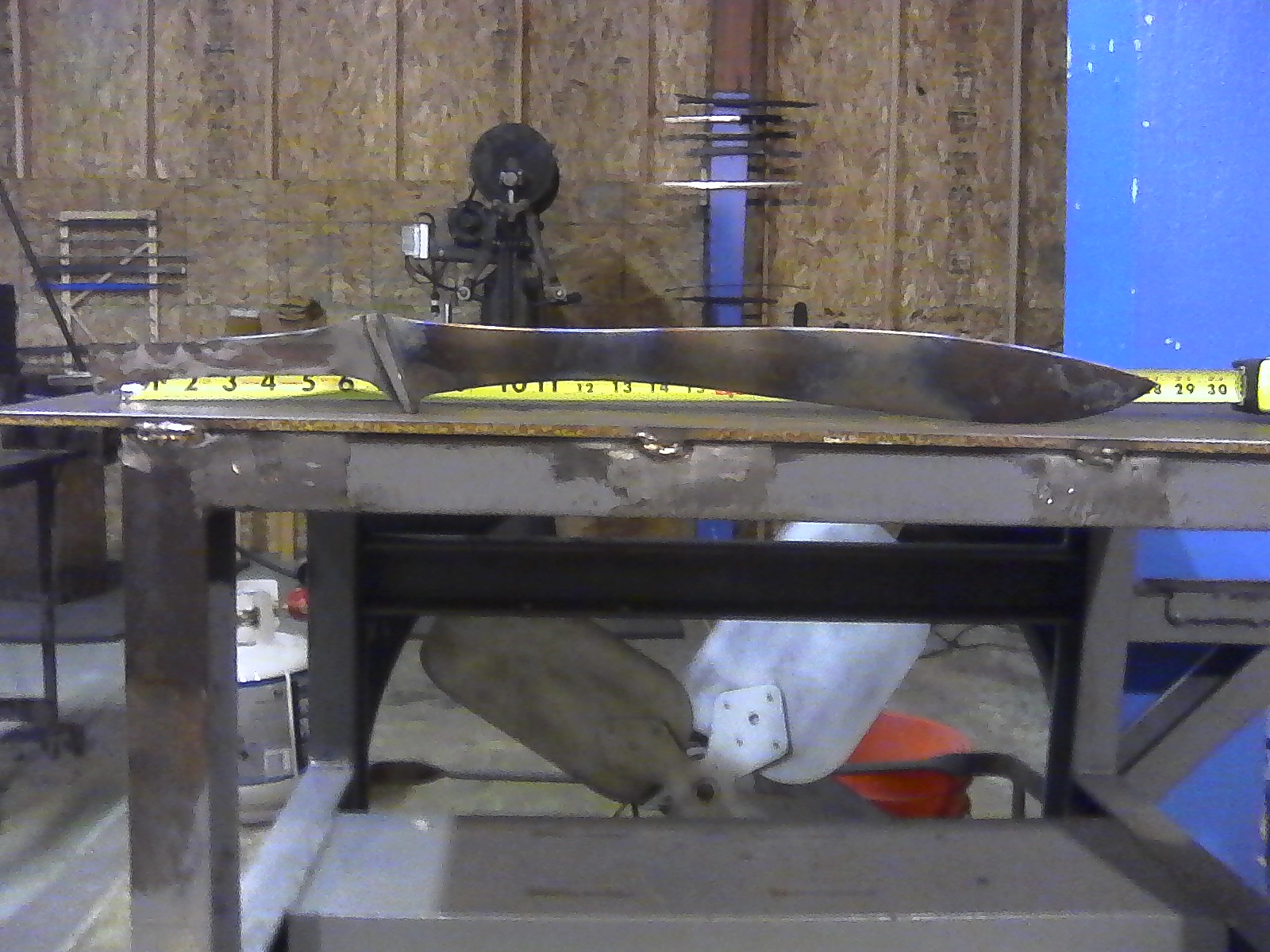
Straightening.

The blade was convex-ground to zero along its length. It is quite thick by the guard, and tapers rapidly toward the tip.

Apparently it looks like a "falkri," or falcata-kukri, haha.


Thanks for looking.

-------
"Update! Just got it back from Sam, heat treated/pommel added/balance adjusted...and it's freaking awesome!" -WValtakis
~Chip
------
Looking forward to seeing how it looks after engraving.