Brian.Evans
Registered Member
- Joined
- Aug 20, 2011
- Messages
- 3,267
I dropped my carbide faced file guide and snapped one of the carbide pieces, so I had to pause the Dart EDC run while it's off at Bruce Bump's shop getting repaired. Hopefully it will be back tomorrow or Monday. However, I wanted to work on something productive, so I got these rough ground and ready for heat treat. I usually make EDC and general purpose fixed blades, but I wanted to try a couple that were a bit more specialized.
First is about an 8 1/2" chefs knife. 3/32" 52100, right under 2" at the heel. I'm going to be making six more of this pattern once the Dart EDC run is finished, three in 52100 and three in AEB-L.
This is a project I've been working on for quite some time. I partnered with a guy over on Straight Razor Place forum three or four years ago to help me design a straight razor and convert to CAD. This is my first attempt at grinding one of the blanks. I have round nose, square nose, and square nose with a barber's notch patterns ready to be cut. This was ground on a 2" wheel, hopefully I can grind the next one on a 6" or 8" wheel. 0.220" thick A2, 0.850" from spine to edge. Should be right in that 16ish degree inclusive edge angle. The next ones will be in AEB-L or 52100.
Razors and kitchen knives are completely different than regular fixed blades. Even if these don't turn out I'm going to keep plugging along. I've really enjoyed pushing my limits as a maker by trying these.
First is about an 8 1/2" chefs knife. 3/32" 52100, right under 2" at the heel. I'm going to be making six more of this pattern once the Dart EDC run is finished, three in 52100 and three in AEB-L.
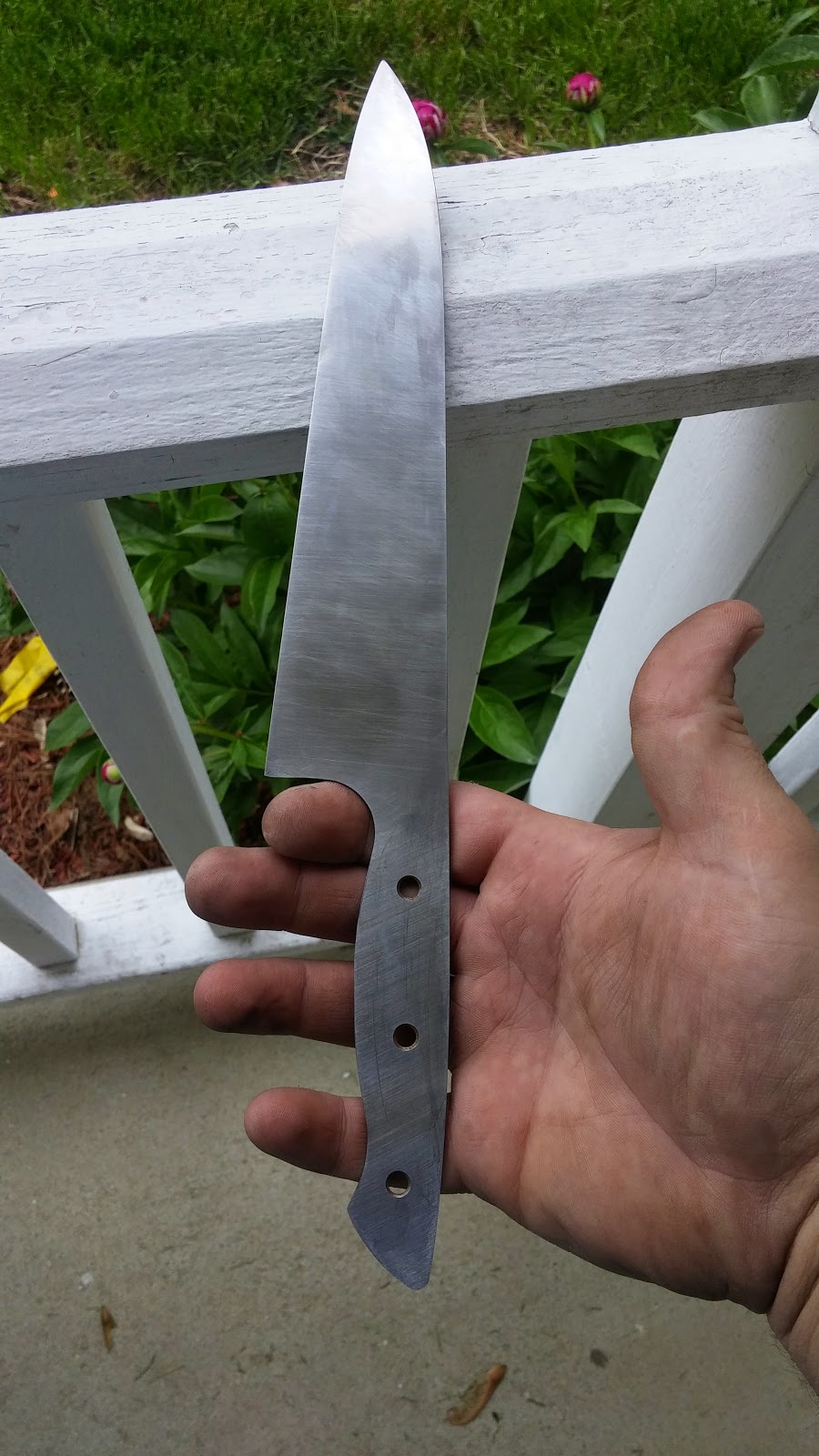
This is a project I've been working on for quite some time. I partnered with a guy over on Straight Razor Place forum three or four years ago to help me design a straight razor and convert to CAD. This is my first attempt at grinding one of the blanks. I have round nose, square nose, and square nose with a barber's notch patterns ready to be cut. This was ground on a 2" wheel, hopefully I can grind the next one on a 6" or 8" wheel. 0.220" thick A2, 0.850" from spine to edge. Should be right in that 16ish degree inclusive edge angle. The next ones will be in AEB-L or 52100.

Razors and kitchen knives are completely different than regular fixed blades. Even if these don't turn out I'm going to keep plugging along. I've really enjoyed pushing my limits as a maker by trying these.