The kit comes from Rough Ryder. It is my third knife-making experience. I love this.
However, the rocker bar sticks up too far and I cannot figure out why. All the pieces were made by the manufacturer and so were the holes. I can't tell if the spring should be cut shorter, the pivot pin hole raised, the width of the rocker bar reduced, or what.
Does anyone have an answer? It's probably obvious to all of you experts but I just don't see it.
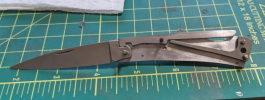
Thanks.
However, the rocker bar sticks up too far and I cannot figure out why. All the pieces were made by the manufacturer and so were the holes. I can't tell if the spring should be cut shorter, the pivot pin hole raised, the width of the rocker bar reduced, or what.
Does anyone have an answer? It's probably obvious to all of you experts but I just don't see it.
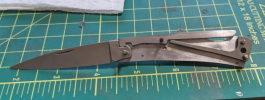
Thanks.