- Joined
- Oct 21, 2006
- Messages
- 1,652
So, my TR6 needs a new frame. I've got a replacement frame just about ready to go (needs a few things like the differential mounts boxed in, and some other things I'll do to reinforce it since it's by itself right now.)
Having having taken my newly acquired TR7 for a nice long 144 mile round trip foliage tour yesterday with New England Triumphs, I picked today to start dismantling the TR6.
Here's the TR6 as it was the last day I drove it
Here's the TR7 yesterday morning while waiting for others to show up for the foliage tour
Today I removed the seats, most of the carpet, the front bumper and scoop, the two front fenders, the driver side door, and the bonnet all removed. Things are at once both worse than I hoped, but better than I feared.
The very first sign of trouble was when I was removing the driver side light fixture so that I could get at the interior bolts to remove the fender. The inner-cup part had significant rust holes in it.
I also had two stubborn bolts, after torches, penetrating oil, and big breaker bars failed to work, I had to drill through the heads and chisel them off
In order to get the bolt off inside the light housing, due to lack of having a ratchet with an adjustable angle head, I took the bonnet off first
Once I did get the driver side fender off, this is what greeted me. The yellow thing is a pen that some how got into the wall of the car
The driver side fender isnt that bad, the rust at the bottom should be repairable.
When I cleaned out the driver side wall, I was surprised that the rocker panel is solid, and it's just the front panel that's realy rusted out. A little bit of rust has crept to the tub wall, but only at the very bottom corner.
The top of the tub where the fender bolts down is a bit rusted, but should be repairable alright.
Having having taken my newly acquired TR7 for a nice long 144 mile round trip foliage tour yesterday with New England Triumphs, I picked today to start dismantling the TR6.
Here's the TR6 as it was the last day I drove it
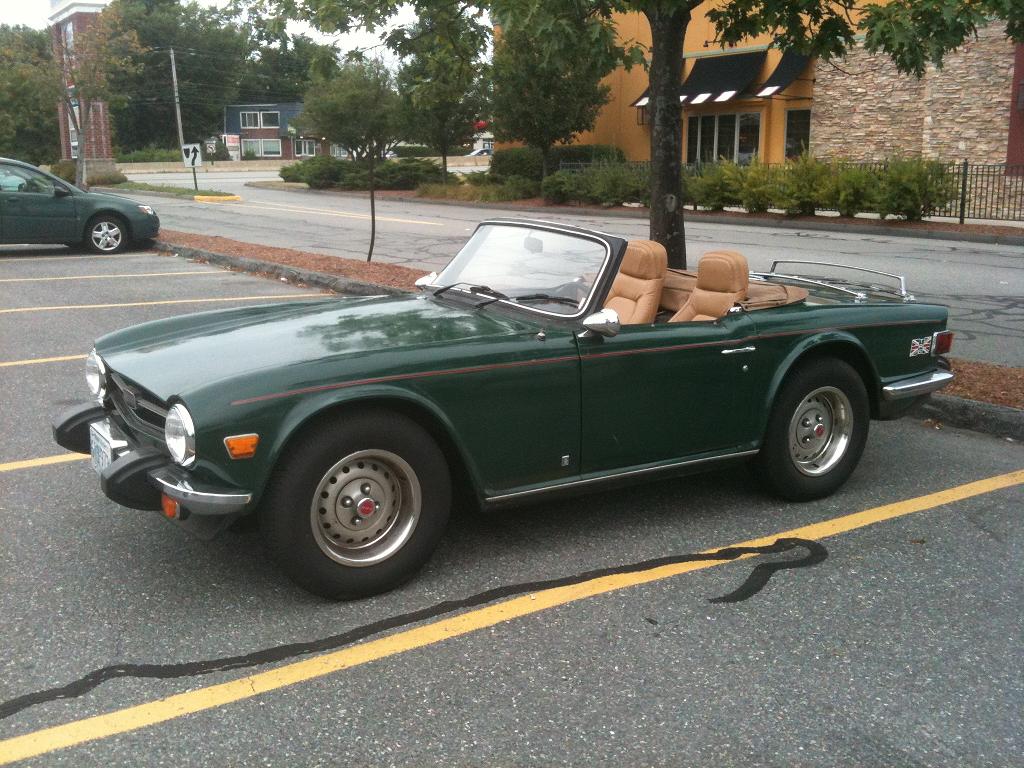
Here's the TR7 yesterday morning while waiting for others to show up for the foliage tour
Today I removed the seats, most of the carpet, the front bumper and scoop, the two front fenders, the driver side door, and the bonnet all removed. Things are at once both worse than I hoped, but better than I feared.
The very first sign of trouble was when I was removing the driver side light fixture so that I could get at the interior bolts to remove the fender. The inner-cup part had significant rust holes in it.
I also had two stubborn bolts, after torches, penetrating oil, and big breaker bars failed to work, I had to drill through the heads and chisel them off
In order to get the bolt off inside the light housing, due to lack of having a ratchet with an adjustable angle head, I took the bonnet off first
Once I did get the driver side fender off, this is what greeted me. The yellow thing is a pen that some how got into the wall of the car
The driver side fender isnt that bad, the rust at the bottom should be repairable.
When I cleaned out the driver side wall, I was surprised that the rocker panel is solid, and it's just the front panel that's realy rusted out. A little bit of rust has crept to the tub wall, but only at the very bottom corner.
The top of the tub where the fender bolts down is a bit rusted, but should be repairable alright.