Last Visible Canary
actively parsing hurf durf
- Joined
- Nov 28, 2006
- Messages
- 4,577
With any khukuri that I plan on using, I like to etch it to see just where the hamon is. It can give some indication of where problem areas are likely to arise, and where you can really wail on it and not worry about excessive rolling. Occasionally you'll get a hamon that only covers the sweet spot, other times you'll get one that covers too much of the blade and may cause lines of stress from edge to spine.
Every now and then, you get what I consider to be a perfect khukuri hammon line. In this case, the hamon is crisp and clear from the tip to within 2 inches of the cho. The sweet spot has an inch of depth, and the tip section has at least 1/2" of depth.
I've been out of the loop for a while, so I'm not sure of the kami who made this. The symbol appears to be a bow and arrow.
Every now and then, you get what I consider to be a perfect khukuri hammon line. In this case, the hamon is crisp and clear from the tip to within 2 inches of the cho. The sweet spot has an inch of depth, and the tip section has at least 1/2" of depth.
I've been out of the loop for a while, so I'm not sure of the kami who made this. The symbol appears to be a bow and arrow.
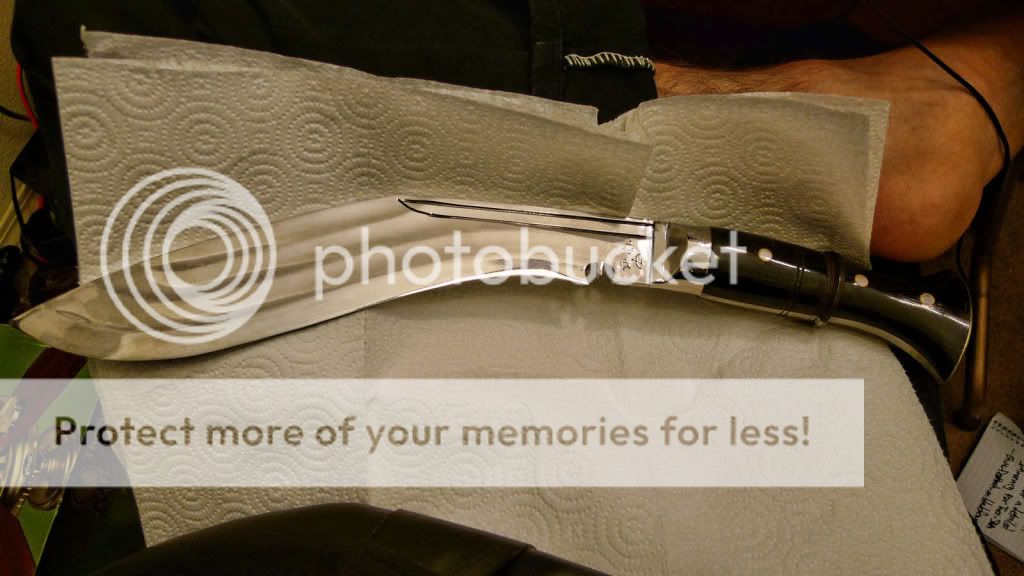

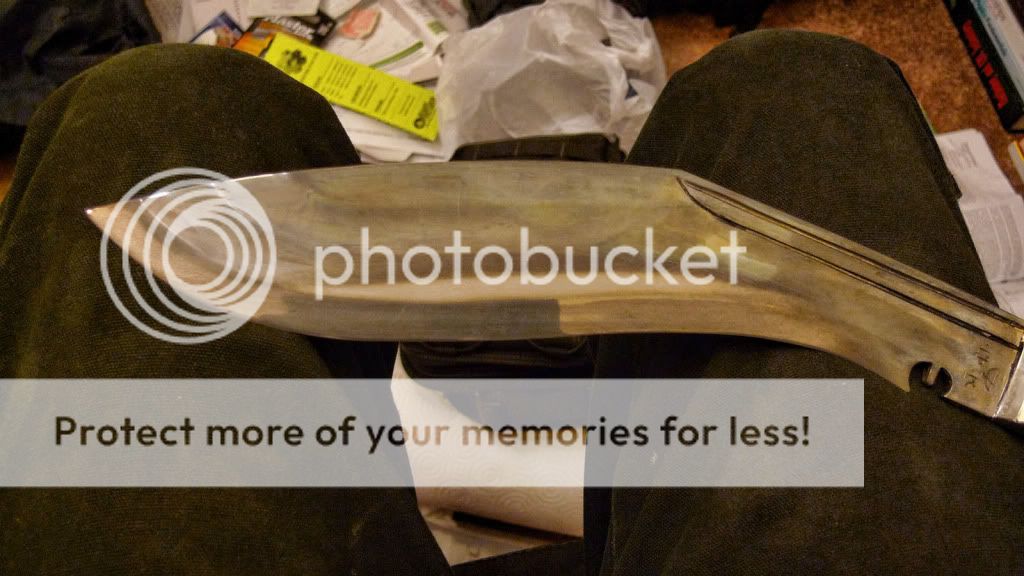
