is this clsoe to what you guys are talking about? T.A., Martin, and McCallion H. "Knife Slicing of Wood Across the Grain." Wood Science and Technology 30 (1996): 397-410.
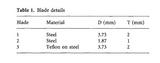
A graph of load versus crosshead displacement for three specimens cut at 50 mm/min
is shown in Fig. 7. The three curves are quite similar given the natural variability of the
wood samples. As the blade penetrates the wood the cutting force increases linearly and
continues to rise after the head of the blade is fully embedded in the block. It attains
a maximum value of 135 kN/m at a depth of about 6 mm. Thereafter a steady state is
reached and the cutting force remains relatively constant for the rest of the cut. Minor
fluctuations in the loads reflect noise in the signal due to microcracking in the wood.
When the blade first contacts the body, there is no apparent jump in the load. This
indicates that the wood fibres fracture almost immediately at a very low load. Most of
the energy going into the cutting operation is, therefore, associated with compressing
and shearing the wood around the rigid indentor.
Figure 13 shows the cutting forces recorded for wet and dry wood specimens sliced
with a 1 mm thick steel blade. The dry wood yields an average cutting force of 84 kN/m;
a reduction of 34% over that measured with blade 1 (see Table 3). The theoretical model
predicts a 50% reduction in the cutting force for a blade of half the thickness. However,
this does not occur in practice, because the energy required to fracture the fibres
remains constant and the volume of material being deformed increases in a non-linear
manner, as the blade thickness increases. A large fluctuation in the steady state load
occurs at a crosshead displacement of about 15 mm, where a ball of wood is torn from
the block. At this point, more energy is dissipated and the cutting force rises. The steady
state cutting force in the wet wood gradually increases from 32 kN/m to 50 kN/m as the
blade penetrates the block. This increase occurs because the wood fibres return to their
original orientations after shearing past the wedge and compress the web behind the
blade. This effect adds a friction load to the cutting force. The compressive stress on the
web is estimated to be 500 kPa, based on the experimental results and a friction
coefficient of 0.236. With improved blade designs and less permanent fibre damage, this
effect becomes more of a problem. Therefore, the ideal blade should not have a web
behind it.
Lastly we examine the effect of the blade angle on the theoretical cutting force when
using a frictionless blade. Figure 14 shows the effect of the blade angle for two particular
cases: (a) a blade of constant thickness, T, and (b) a blade of constant depth, D. In case
(a), the surface area of the blade tends to infinity as the blade angle tends to zero.
Therefore, the cutting force solution also tends to infinity for small blade angles. As the
blade angle increases two effects come into play; the volume of material being deformed
decreases, and the rotation of the fibres near the blade surface increases. These two
effects cause the theoretical cutting load to decrease. As the wedge opens up, the cutting
operation tends towards crushing, which is more likely to induce fracture along the
grain and an inferior surface finish on the cut. The theoretical model does not provide
a suitable representation of the stress distribution around the blade, when crushing
occurs.
In case (b) the cutting load rises from zero as the blade angle increases and then falls
away again for the same reasons as those just mentioned. This figure suggests that
a blade angle of greater than 30 ~ would reduce the cutting force. This finding is
supported by experimental work by Donohue (1994), which shows a decreasing cutting
force for a constant blade thickness as the blade angle is increased from 15 ~ to 45 ~
A predicted cutting force of 205 kN/m is indicated by a line at 13 = 30 ~ This is somewhat
higher than that recorded, but is in the correct range considering the unknown material
properties for the Pinus radiata samples. A full finite element analysis for an
orthotropic material with finite strain should be developed, in conjunction with the
experimental determination of the material constants, to obtain an accurate
understanding of the stresses in the cutting region. A fracture mechanics approach
could then be used to predict crack growth across and along the fibres.
