- Joined
- Oct 28, 2006
- Messages
- 13,363
I have been admiring Bruce Bump's work for a long time so I was naturally very excited when my order came up.
After our deciding on a design which in addition to Bruce's magic includes the masterful engraving of Jere Davidson and the the color-case hardening process of Doug Turnbull Bruce immediately went to work on the "Allen Pinkerton Bowie". He's been sharing his efforts in a work in progress over on the CKCA forum for about 6 weeks.
The full thread including the forging of the damascus, questions/answers etc. can be found @ http://www.customknifecollectorsassociation.com/vbulletin/showthread.php?t=520
Here's a peak at what the finished Bowie will look like though we've made some subtle adjustments along the way.(these drawings have been reduced so not actual size)
Bruce started off forging a 9" Feather Pattern Damascus Blade and we will start here with the completed billet.
Bruce take us on the journey:
I used my brand new Jet band saw and cut this one lengthwise. I like this saw!
I forged the best slice out into a blade and did some quick grinding to see what I have as far as problems and pattern. Its hard to see the pattern until I do a deep etch but it looks pretty good so far. There were a couple hair-line cracks along the edge but they ground right out. We might have a good one this time but like I've said before "keep your fingers crossed".
I have it in the annealing oven at 1325 deg. for 30 minutes.
Don't go too far away, I'm heat treating and grinding the blade next asap.
After our deciding on a design which in addition to Bruce's magic includes the masterful engraving of Jere Davidson and the the color-case hardening process of Doug Turnbull Bruce immediately went to work on the "Allen Pinkerton Bowie". He's been sharing his efforts in a work in progress over on the CKCA forum for about 6 weeks.
The full thread including the forging of the damascus, questions/answers etc. can be found @ http://www.customknifecollectorsassociation.com/vbulletin/showthread.php?t=520
Here's a peak at what the finished Bowie will look like though we've made some subtle adjustments along the way.(these drawings have been reduced so not actual size)
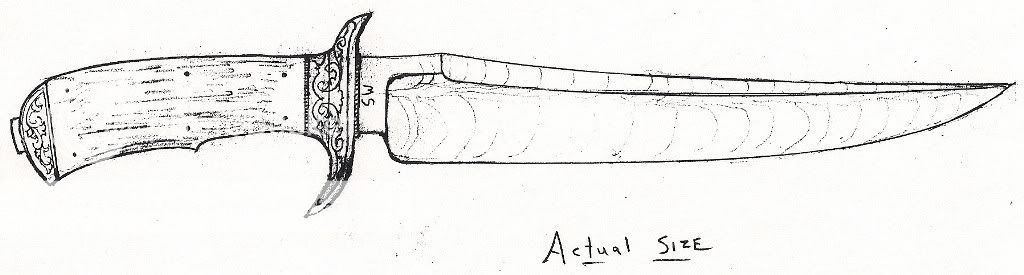

Bruce started off forging a 9" Feather Pattern Damascus Blade and we will start here with the completed billet.
Bruce take us on the journey:
I used my brand new Jet band saw and cut this one lengthwise. I like this saw!
I forged the best slice out into a blade and did some quick grinding to see what I have as far as problems and pattern. Its hard to see the pattern until I do a deep etch but it looks pretty good so far. There were a couple hair-line cracks along the edge but they ground right out. We might have a good one this time but like I've said before "keep your fingers crossed".
I have it in the annealing oven at 1325 deg. for 30 minutes.
Don't go too far away, I'm heat treating and grinding the blade next asap.





Last edited: