- Joined
- Aug 21, 2013
- Messages
- 3,898
Using Trailtime's example - A new supplemental handle. The only hickory I had around was an old Model T Ford wheel spoke (about 1925 model year car). I used a cross dowel barrel nut in the handle with one side exposed and contoured to the shape of the handle.
The parts:
![]()
The competed parts:
![]()
Done with more handle parts in the background:
![]()
Jim
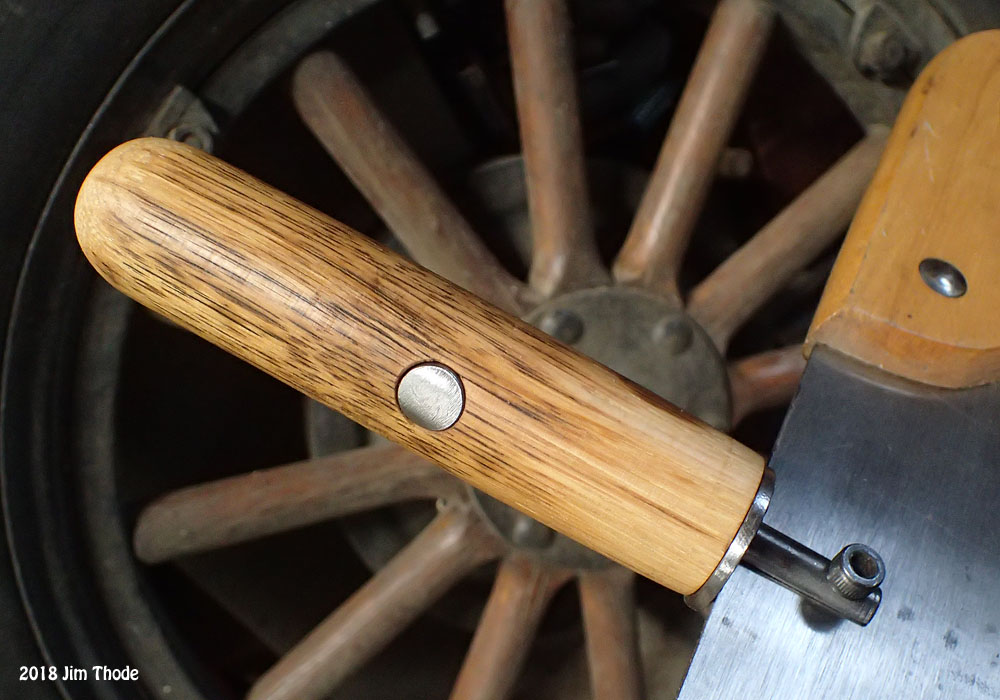
That really is impressive Jim!