Hi guys, Jason here. I've been reading this forum for quite some time now, and have asked some questions along the way to making my first knife. Looking back in my emails, it looks like I started this blade late January 2008. It's made from 5/32 O1 from Rob and Marilyn up here in Canada. Blade length is around 3.8" and the handle is right around 4".
I cut out the design with a hack saw, and then filed it down smooth. Other than a drill press to drill the holes in the tang, all work was done with files and sand paper. Started the bevels with a coarse Mastercraft file, then when I got the majority of the material off, I bought a Nicholson Mill Bastard file. Man, what a difference a quality file makes! I had heard people talk about Nicholsons, and were they ever right. After filing, I started sanding it. Just working with what I had, I started with 80 then jumped to 180 grit. For handles I'm going to be making up some micarta.
Just looking for some input pre-heat treat. All comments welcome - on design, sanding, plunges, bevels, and anything else you got. Good or bad, give it to me, I can take it all:thumbup:
Here are a bunch of pics:
Full flat grind with distal taper.
I left the edge around .027" thick or so. I was told this would be fine for heat treat? I don't have a grinder or anything, so I will be putting on the final edge with sandpaper I suppose.
Thanks for all the help thus far, and any comments/criticisms you can offer!
Jason
I cut out the design with a hack saw, and then filed it down smooth. Other than a drill press to drill the holes in the tang, all work was done with files and sand paper. Started the bevels with a coarse Mastercraft file, then when I got the majority of the material off, I bought a Nicholson Mill Bastard file. Man, what a difference a quality file makes! I had heard people talk about Nicholsons, and were they ever right. After filing, I started sanding it. Just working with what I had, I started with 80 then jumped to 180 grit. For handles I'm going to be making up some micarta.
Just looking for some input pre-heat treat. All comments welcome - on design, sanding, plunges, bevels, and anything else you got. Good or bad, give it to me, I can take it all:thumbup:
Here are a bunch of pics:




Full flat grind with distal taper.
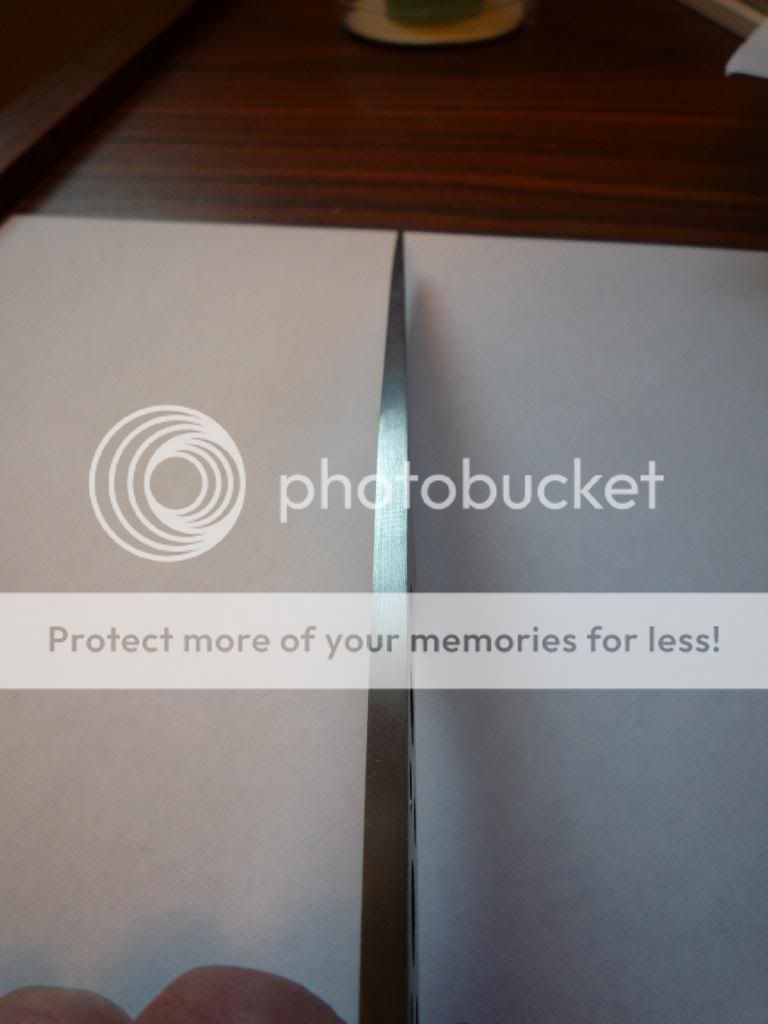
I left the edge around .027" thick or so. I was told this would be fine for heat treat? I don't have a grinder or anything, so I will be putting on the final edge with sandpaper I suppose.

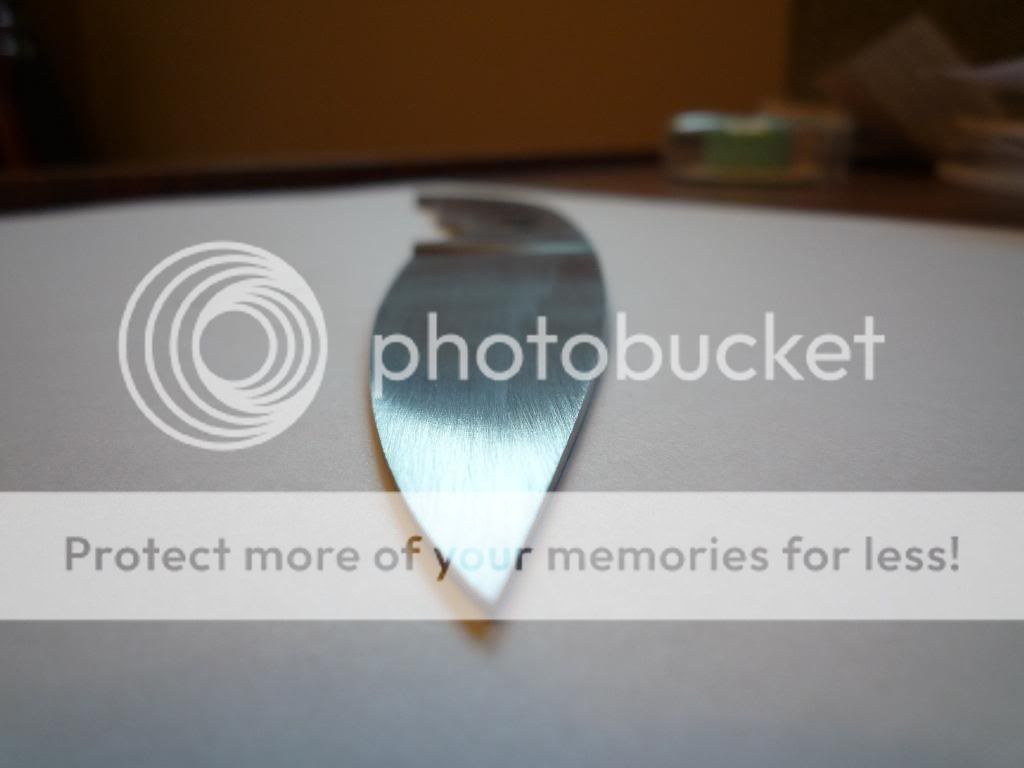
Thanks for all the help thus far, and any comments/criticisms you can offer!
Jason