- Joined
- Aug 13, 2002
- Messages
- 5,703
I've tried all possible solutions in an effort to make slotting handles for hidden tang easier. Files, hacksaw blades super glued together, power hacksaw, drywall knife, even extra long drill bits in a Dremel. 
(Ask me how how now know not to put an extra long bit with a poorly balanced depth stop on it in a 15,000RPM Dremel!
Seems obvious in retrospect. I guess I'm the guy for whom they put the Do not ingest warnings on things like Acetone.
)
After a post by Ed Caffrey about broaches that Michael Rader made for him I thought why not. Might as well try that too. Of course they are not even close to the incredible broaches Michael did. They are made of 1095 but not even heat treated. And as you can see, the teeth geometry is probably all wrong.
BUT even as crappy as they are, they work great. A thousand times better than anything else I tried and spent countless hours messing with. Wish I had tried that first. Simply used those little cut-off disks in the Dremel to shape the teeth. ***Don't forget those safety glasses!***
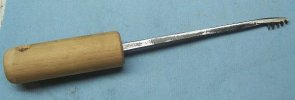
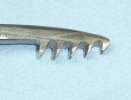
Make some, you'll be happy you did. :thumbup:

(Ask me how how now know not to put an extra long bit with a poorly balanced depth stop on it in a 15,000RPM Dremel!


After a post by Ed Caffrey about broaches that Michael Rader made for him I thought why not. Might as well try that too. Of course they are not even close to the incredible broaches Michael did. They are made of 1095 but not even heat treated. And as you can see, the teeth geometry is probably all wrong.
BUT even as crappy as they are, they work great. A thousand times better than anything else I tried and spent countless hours messing with. Wish I had tried that first. Simply used those little cut-off disks in the Dremel to shape the teeth. ***Don't forget those safety glasses!***
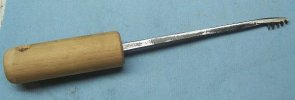
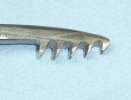
Make some, you'll be happy you did. :thumbup: