Square_peg
Gold Member
- Joined
- Feb 1, 2012
- Messages
- 13,818
This is a follow up thread on a post I made in another thread about slip-on type handles. See that post here:
http://www.bladeforums.com/forums/s...-eye-vs-Axe-Wedge-eye?p=14306344#post14306344
This wedging system addresses a mythical scenario where you're isolated in the wilderness and have broken your axe handle. You need a functioning axe to save your life. We know this is never really gonna happen but for the sake of argument let's go with this scenario.
I discovered this system on a broadaxe I purchased a few years ago. I'm guessing that the previous owner had a second handle for this broadaxe which allowed hafting it with the bevel reversed from right to left. That's a handy thing and was likely the reason that some old boy came up with this. Here's the system as it came on that old broadaxe. This axe was solid as hung with this system.
So the previous owner could remove this haft and insert another one through the top of the eye and thereby change the handing of his broadaxe.
For some time I've had the idea try this system out with a regular axe or hatchet. The earlier thread gave me the nudge I needed to finally do this. Remember, this is an "isolated in the wilderness" situation so what I did was quick and dirty with only knife and a hatchet. OTOH you could do this carefully in the shop with power tools and make it a nice handle. The work could easily be done with just the broken axe if that is all you had. And we all know how to burn an old handle out of an axe head with the bit buried in the dirt to protect the temper.
So I started with this, a branch of big leaf maple which I dragged home a couple weeks ago.
Right away it split on me when I started to carve it. But since this was just to demonstrate the system I continued on. Hey, in the wilderness you may have no choice but to carry on.
Here I've shaved off part of the handle to make room for what I call the side wedge. I'll also have to take off some material for the back wedge.
It's important that the side wedge sticks further back than the handle. Imagine if this haft wasn't split. The side wedge would protrude 1/4" further toward the poll than the haft does. The back wedge will force the side wedge over the haft causing the side wedge to fill the eye side-to-side.
Here I've started work on the back wedge. Note how it pushes the side wedge over the haft.
With the back wedge in I could swing this axe now. At this point I've got 25 minutes into carving this handle and wedge system.
A bottom view of the wedged axe.
Another 25 minutes of whittling and I have a functional axe. I did a little chopping and splitting with it to make sure it worked.
I pounded the wedges in a little further after use. I might have to re-wedge it once the green handle dries.
Here I've pulled the haft off the first head and put it on another head. I switched it back later.
One of these days I'll take the time to make a nice one of these. If any of you try this please post your results.
http://www.bladeforums.com/forums/s...-eye-vs-Axe-Wedge-eye?p=14306344#post14306344
This wedging system addresses a mythical scenario where you're isolated in the wilderness and have broken your axe handle. You need a functioning axe to save your life. We know this is never really gonna happen but for the sake of argument let's go with this scenario.
I discovered this system on a broadaxe I purchased a few years ago. I'm guessing that the previous owner had a second handle for this broadaxe which allowed hafting it with the bevel reversed from right to left. That's a handy thing and was likely the reason that some old boy came up with this. Here's the system as it came on that old broadaxe. This axe was solid as hung with this system.
So the previous owner could remove this haft and insert another one through the top of the eye and thereby change the handing of his broadaxe.
For some time I've had the idea try this system out with a regular axe or hatchet. The earlier thread gave me the nudge I needed to finally do this. Remember, this is an "isolated in the wilderness" situation so what I did was quick and dirty with only knife and a hatchet. OTOH you could do this carefully in the shop with power tools and make it a nice handle. The work could easily be done with just the broken axe if that is all you had. And we all know how to burn an old handle out of an axe head with the bit buried in the dirt to protect the temper.
So I started with this, a branch of big leaf maple which I dragged home a couple weeks ago.

Right away it split on me when I started to carve it. But since this was just to demonstrate the system I continued on. Hey, in the wilderness you may have no choice but to carry on.

Here I've shaved off part of the handle to make room for what I call the side wedge. I'll also have to take off some material for the back wedge.

It's important that the side wedge sticks further back than the handle. Imagine if this haft wasn't split. The side wedge would protrude 1/4" further toward the poll than the haft does. The back wedge will force the side wedge over the haft causing the side wedge to fill the eye side-to-side.
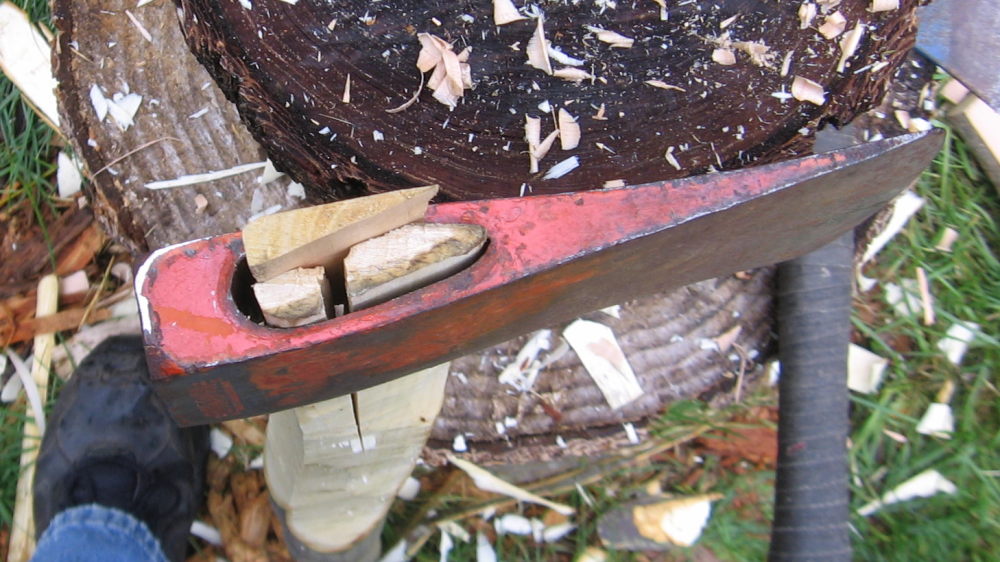
Here I've started work on the back wedge. Note how it pushes the side wedge over the haft.

With the back wedge in I could swing this axe now. At this point I've got 25 minutes into carving this handle and wedge system.
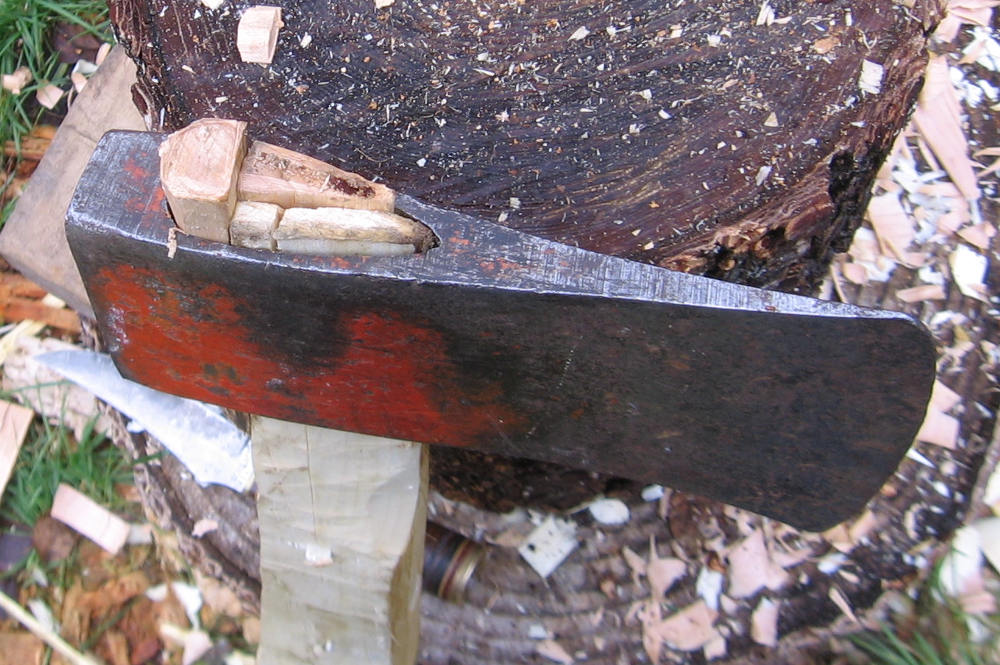
A bottom view of the wedged axe.
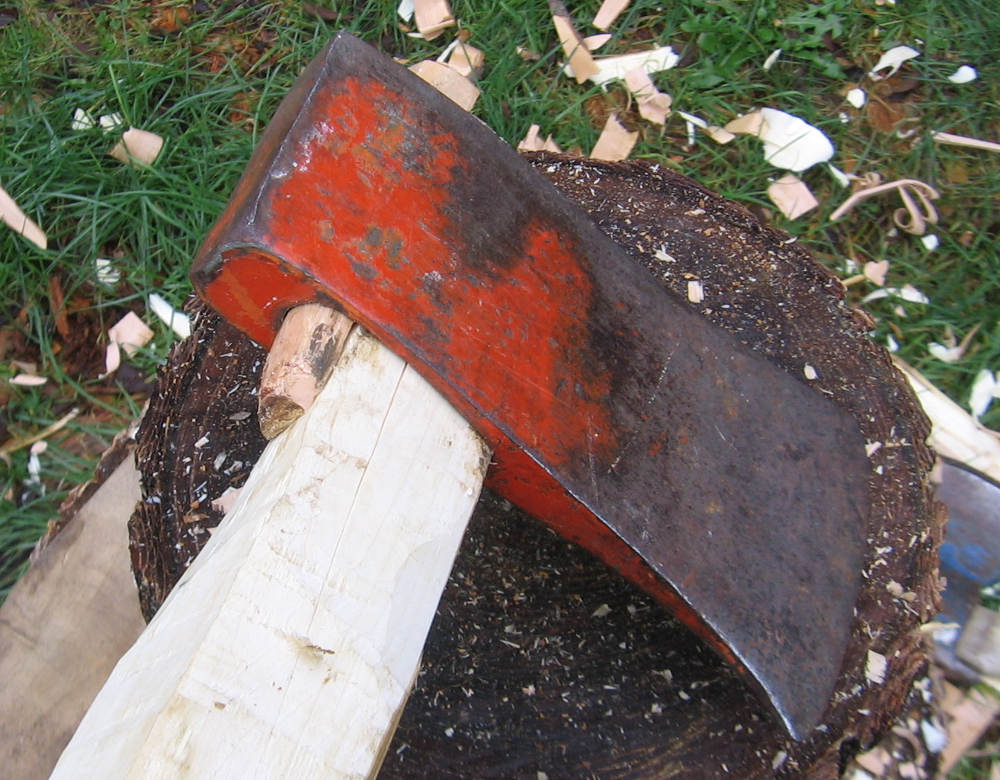
Another 25 minutes of whittling and I have a functional axe. I did a little chopping and splitting with it to make sure it worked.
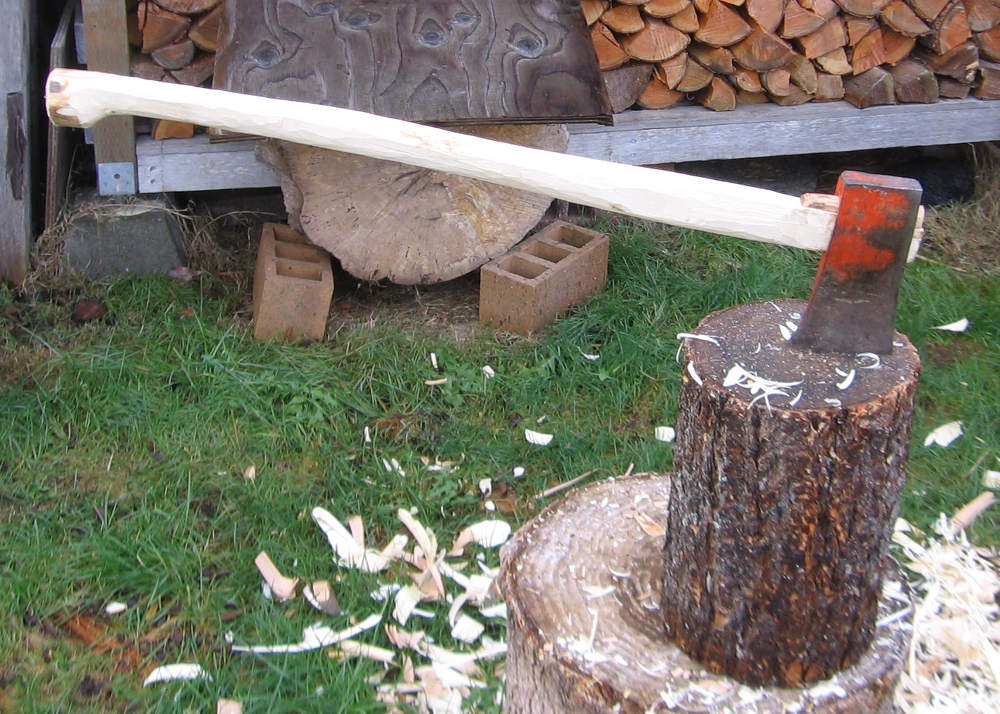
I pounded the wedges in a little further after use. I might have to re-wedge it once the green handle dries.
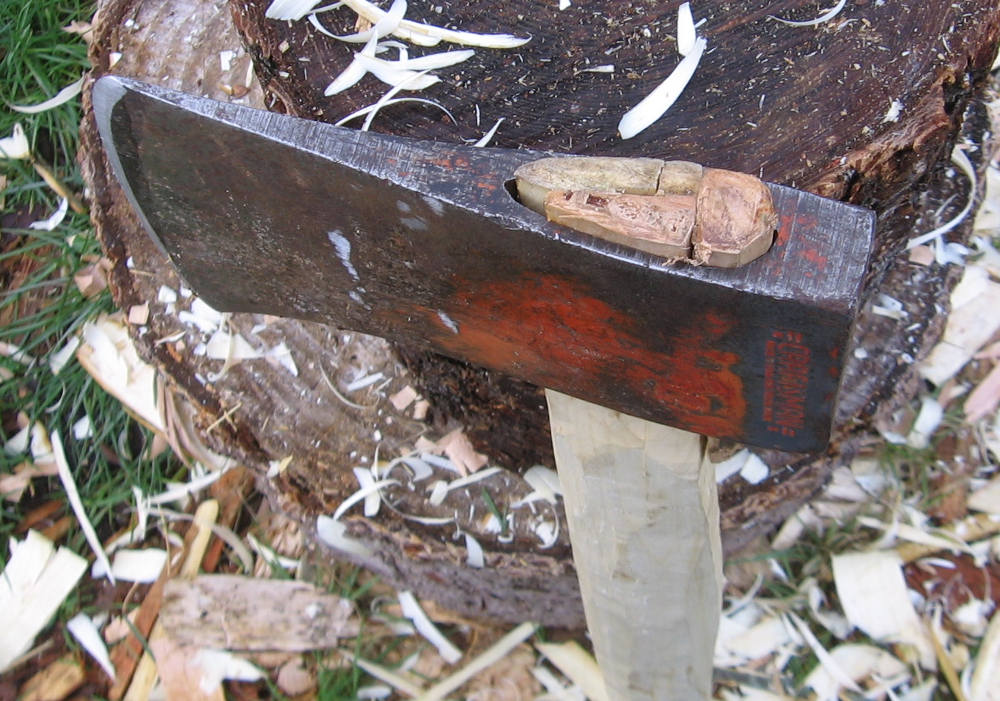
Here I've pulled the haft off the first head and put it on another head. I switched it back later.

One of these days I'll take the time to make a nice one of these. If any of you try this please post your results.
Last edited: