The following was posted on Peter Vido's blog, AxeConnected.
Earlier this year we ordered a two-pack of double bit "cruiser" axes from the Barco company in Pennsylvania; one for a fellow ax user in Nova Scoti, the other for us to test out and review.
First of all, let me say that I consider this ax to be very unique. I'll elaborate on that, but for now, some of my first impressions:
Barco's description of their axes sounds very impressive. They don't say too much on the specific product descriptions, but the implication is that these are US made
From their website:
"These are the finest quality US made axes available. The Kelly Perfect® features a full polished head with deep bevels to reduce binding of the head in the wood, painted a distinctive blue, while the Kelly Woodslasher® line is painted red with polished edge."
Although I hope that this company would not deliberately mislead their customers, at this point I am doubtful about the origins of this cruiser ax.
The most obvious thing to cause my suspicion that these "Forged with pride in the USA" axes are imported -- the heads are not stamped with any name or trademark, or even weight. The heads do have a faint "BARCO / WEAR SAFETY GOGGLES USA / 08 1" printed on one face.
(Gee, thanks for reminding me, where did I leave those safety goggles that I always wear when using an ax...?) As soon as the red paint is removed, the only mention of USA is gone with it. If one of the last remaining ax manufacturers in the US was proud of their product, don't you think they would be sure to leave a prominent trademark, one that will speak to the quality of their axes in years to come?
Back to the ax (whatever the origin), that "2 1/2 lb. Kelly Woodslasher Michigan double bit cruiser" from Barco.
Taking a closer look at the one we kept, it seemed worthwhile to document how the edges had been ground. Or over-ground, I should say. The edge had been rather unevenly ground, too much taken off at the top and bottom corners, one corner nearly burned and a big burr left on the edge.
Peter spent half an hour thinning down one of the faces to the kind of edge we keep on our felling axes, which is thinner than the standard these days, but nearly on par with how the old fellas in these parts liked their axes. He didn't file right up to the corners, but the top right one already looks as though it's had too much metal removed.
We hadn't done anything to the handle by this point; I could already tell that, at 20mm, it was thicker than I would like to use (though admittedly thinner than most conventional ax handles these days), but it wasn't a "club", so Peter suggested that I try it out as is.
Heading off to the woods to give it a test run, I felled a small green fir tree and then quickly hewed a short piece of the trunk.
The thick handle bothered me, and I felt like it should have been longer for the weight of the head, but overall, I was pretty pleased with the little cruiser by that point. Impressed with how clean a hewing job it did, I was already thinking about the review I'd be giving it; if not glowing, at least pretty positive. Well, that was before I went to limb the few small branches
About three-quarters of the way along the length of this little tree, something felt wrong. There was a bit of swearing involved when I looked at the ax; the edge had gotten both chipped off and bent over -- "rolled" is the proper term, I believe. Going back over the length of the tree, I and located the largest limbs, all of which were smaller than 1/2 an inch in diameter.
This is where I started feeling that I was in possession of a pretty unique little ax; I've never before heard of this happening. I am by no means knowledgeable when it comes to steel quality and forged tools in general, but I was under the impression that edge tools can sometimes be too hard, causing the steel to chip, or too soft, causing it to buckle or bend over. Never seen both at once though
Here's a closer look at the edge. Unique, all right!
I had taken another ax along that day, a 2 3/4 lb. Swedish military surplus single bit on a 27" handle, with the edge filed down the way we like them. So before heading back home, I felled and limbed another fir with that one. The edge remained intact
Then for good measure I chopped down and limbed a third tree using only a kukri knife, a new one that a good friend had kindly sent for us to test out. The edge on this kukri was thinner than others I'd seen, but when put through the same treatment as the cruiser, it passed the test with flying colours, no damage whatsoever.
Thus I suspect that it can't have been only those 'tough' branches that were to blame
At Peter's suggestion I took the cruiser out again later on, this time using the opposite face. I had taken the burr off and smoothed the transition between the micro-bevel and the rest of the face but did no actual re-shaping. With it, I managed to take down a small green beech (with a great deal of effort, since the edge had virtually no penetration ability, unsurprisingly).
The next day Peter removed the damaged edge on the first face, leaving a thicker profile. By this time I had gotten tired of using that handle the way it had come from the factory, so I took a rasp to it and pretty much just removed the lacquer, then smoothed it down with a piece of glass.
I happened to think of taking photos of the labels on either side of the handle before removing them.
Good thing too, this one had a very important message, as I was soon to find out.
Not as thin as I'd like, but it sure felt better after being slightly flattened, with the lacquer removed.
Then I headed off into to the woods and picked a medium-sized poplar to test it out on.
I was nearly done notching it, when I took another swing and the handle came back empty, with the head lying in the snow at the base of the tree. I just stared in disbelief. Nope, I hadn't overreached and hit the handle; that fine American hickory just couldn't take the combination of the soft green poplar wood and the girl swinging it. (Weren't these cruisers supposed to be used by grown men?)
The "wear safety goggles" is still faintly visible; now I understand... Shouldn't they have added "wear steel toe boots"?
I'd be interested in hearing some opinions on this one; have you ever seen such a porous-looking hickory?
Another thing we realized once the handle broke was that the wood was amazingly light, not even close to the weight of normal hickory. If we take Barco's word that the handle was USA hickory, not some strange Chinese wood that looks like an Aero Bar on the inside, then our tentative conclusions are that this wood had dry rot.
Okay, but we didn't give up on this ax yet; Peter knocked the remaining broken handle out of the eye, and quickly fitted it with a thiner (18mm) 30" maple handle. This time I tried splitting some firewood with the original (thick) face. This ax does not have an optimal splitting profile, but it worked fine with the "flick" technique I use.
Then, with that new maple handle, I headed off to see what damage I could do next. Taking along the Swedish military surplus ax again, I did some comparisons of the chopping efficiency. Not a real fair comparison, but the Swedish ax's extra weight and the Barco's (now) longer handle balanced out a little bit.
I took down a pair of dying poplars, trying to make an unbiased comparison of the effort expended, then did the same with two larger firs. (One more strike against this "USA" cruiser: the steel has much poorer edge retention in comparison to all of the other axes I've been using; I could hardly believe how fast it dulled even while bucking poplar with no knots.)
The Swedish ax won, hands down. I chopped the trees down in approximately 1/3 less time, and as I limbed each of their respective firs, the Swedish ax left much cleaner cuts, while the cruiser tore the bark surrounding the limbs.
I wasn't happy with the edge on the cruiser (the one that had been thinned, damaged, filed off and left thicker) so in the spirit of second chances, Peter filed it down again, though not quite as thin as the first time. Again, I chopped down a couple firs, then carefully limbed them. Whew, no damage. Then I took down a tiny (green) fir to use as a pushing pole for the larger trees, and started limbing the 1/4" diameter branches. Whoops, there goes another piece of the edge! A few more cuss-words and I headed home, since I hadn't taken a back-up ax along that time.
That was the end of my using this ax for the time being. During the time that I was testing the Barco cruiser, I'd also been doing some chopping with several other axes of adequately thin edge profiles, none of which ever suffered torn edges and broken handles. I might add that the maple handle is still intact, after being put through tougher treatment than the hickory one lasted long enough to endure...
So, would I recommend this ax to anyone based on my experiences? Com'on, now, do I really have to answer that one?

Earlier this year we ordered a two-pack of double bit "cruiser" axes from the Barco company in Pennsylvania; one for a fellow ax user in Nova Scoti, the other for us to test out and review.
First of all, let me say that I consider this ax to be very unique. I'll elaborate on that, but for now, some of my first impressions:
Barco's description of their axes sounds very impressive. They don't say too much on the specific product descriptions, but the implication is that these are US made
From their website:
"These are the finest quality US made axes available. The Kelly Perfect® features a full polished head with deep bevels to reduce binding of the head in the wood, painted a distinctive blue, while the Kelly Woodslasher® line is painted red with polished edge."
Although I hope that this company would not deliberately mislead their customers, at this point I am doubtful about the origins of this cruiser ax.
The most obvious thing to cause my suspicion that these "Forged with pride in the USA" axes are imported -- the heads are not stamped with any name or trademark, or even weight. The heads do have a faint "BARCO / WEAR SAFETY GOGGLES USA / 08 1" printed on one face.
(Gee, thanks for reminding me, where did I leave those safety goggles that I always wear when using an ax...?) As soon as the red paint is removed, the only mention of USA is gone with it. If one of the last remaining ax manufacturers in the US was proud of their product, don't you think they would be sure to leave a prominent trademark, one that will speak to the quality of their axes in years to come?
Back to the ax (whatever the origin), that "2 1/2 lb. Kelly Woodslasher Michigan double bit cruiser" from Barco.
Taking a closer look at the one we kept, it seemed worthwhile to document how the edges had been ground. Or over-ground, I should say. The edge had been rather unevenly ground, too much taken off at the top and bottom corners, one corner nearly burned and a big burr left on the edge.
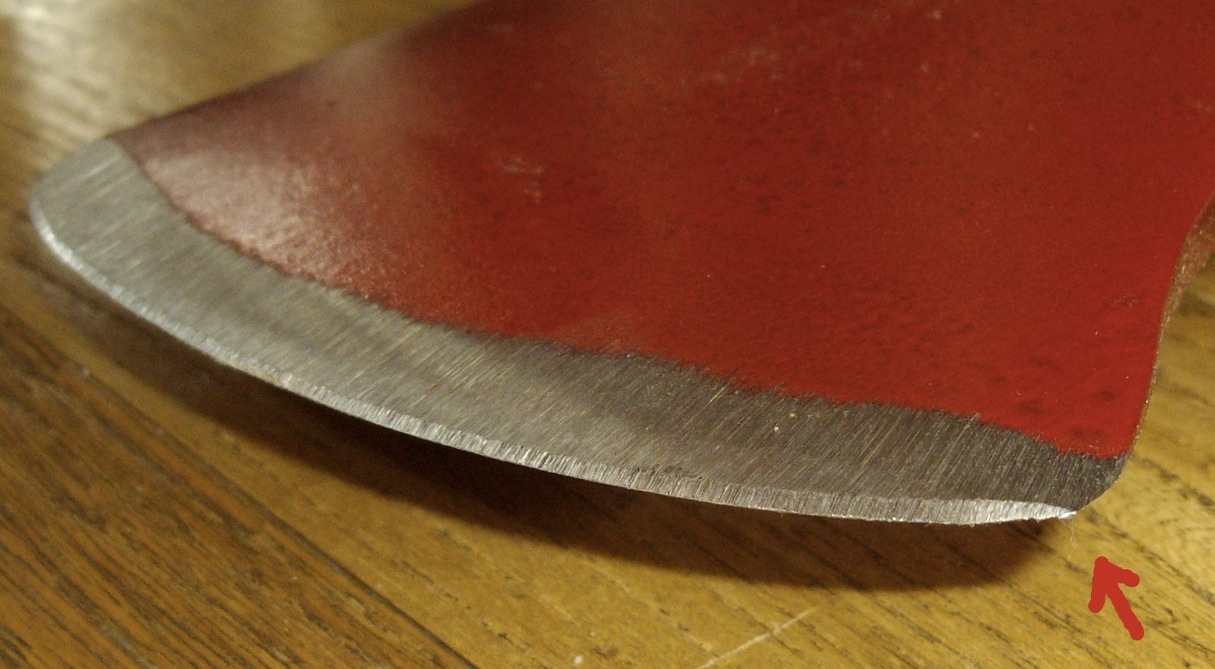
Peter spent half an hour thinning down one of the faces to the kind of edge we keep on our felling axes, which is thinner than the standard these days, but nearly on par with how the old fellas in these parts liked their axes. He didn't file right up to the corners, but the top right one already looks as though it's had too much metal removed.
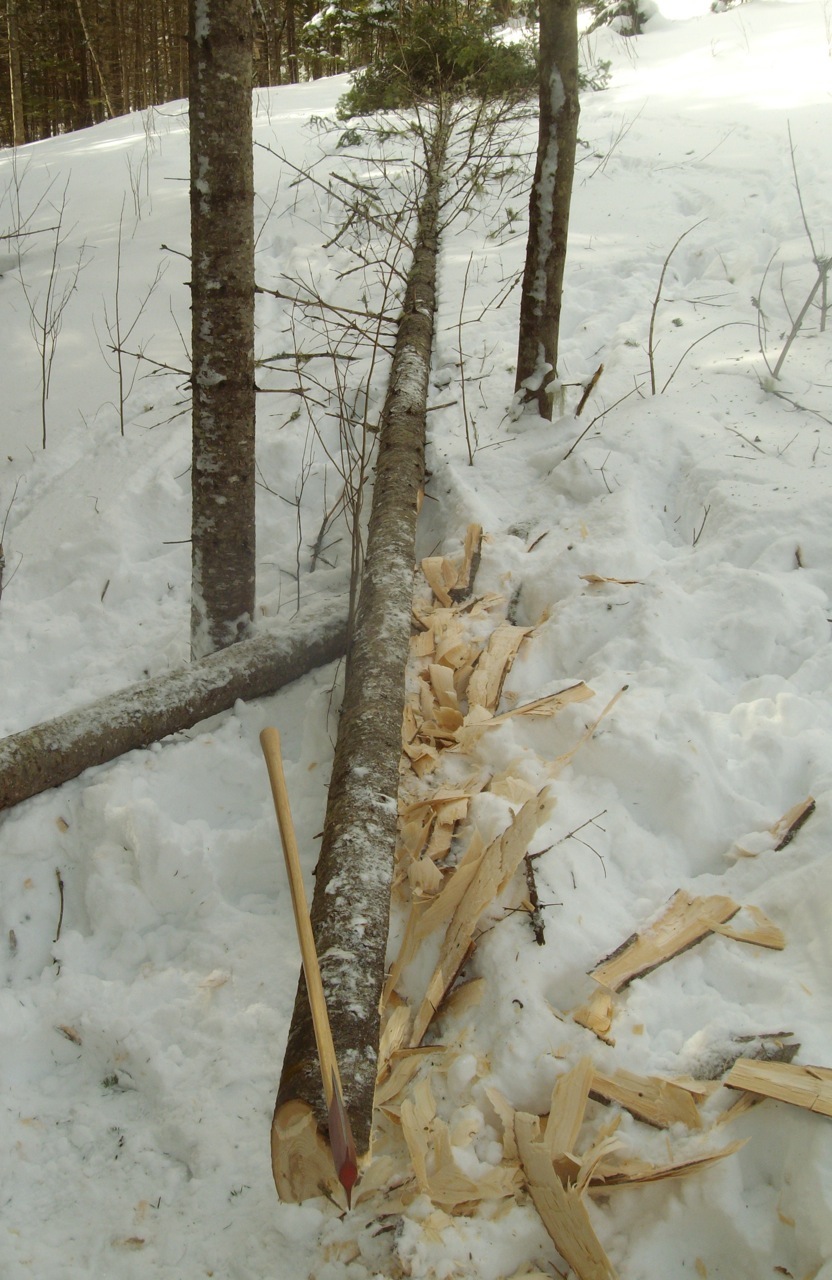
We hadn't done anything to the handle by this point; I could already tell that, at 20mm, it was thicker than I would like to use (though admittedly thinner than most conventional ax handles these days), but it wasn't a "club", so Peter suggested that I try it out as is.
Heading off to the woods to give it a test run, I felled a small green fir tree and then quickly hewed a short piece of the trunk.
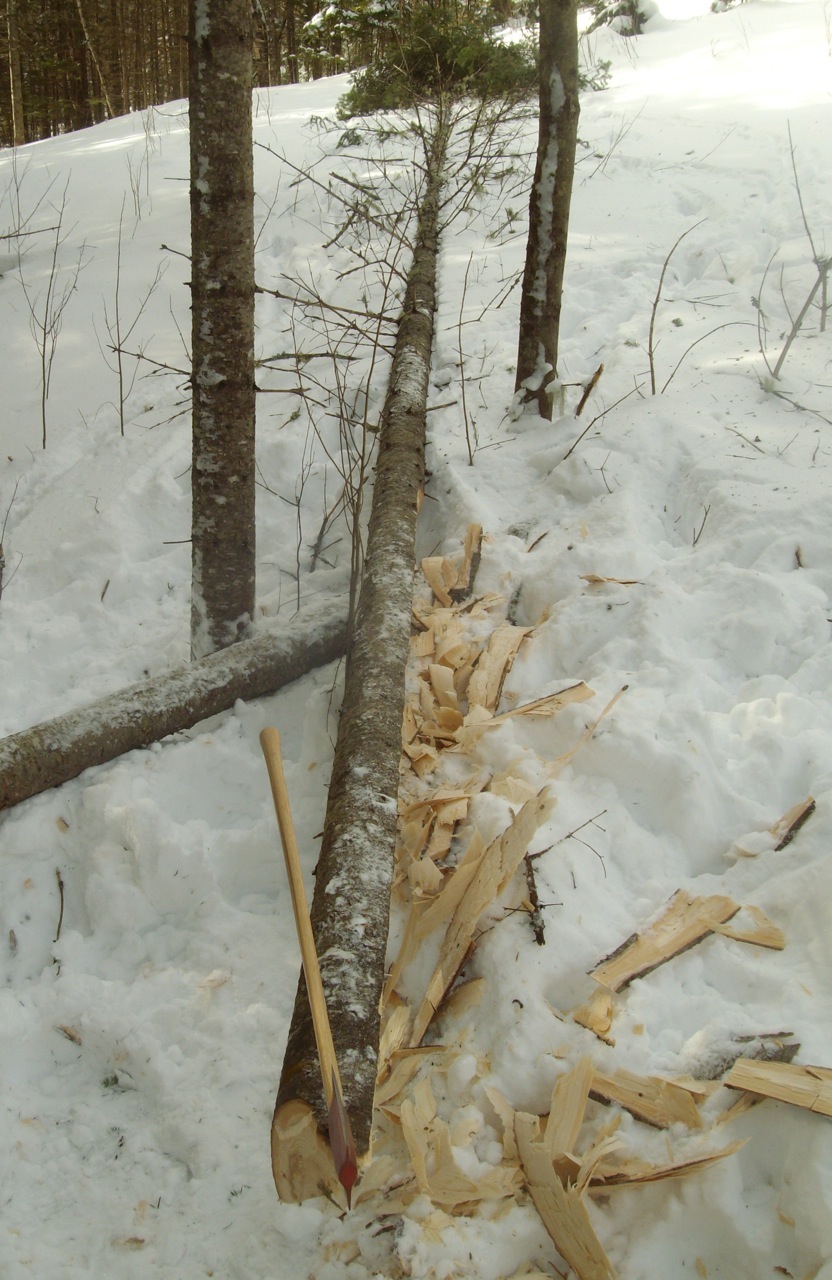
The thick handle bothered me, and I felt like it should have been longer for the weight of the head, but overall, I was pretty pleased with the little cruiser by that point. Impressed with how clean a hewing job it did, I was already thinking about the review I'd be giving it; if not glowing, at least pretty positive. Well, that was before I went to limb the few small branches
About three-quarters of the way along the length of this little tree, something felt wrong. There was a bit of swearing involved when I looked at the ax; the edge had gotten both chipped off and bent over -- "rolled" is the proper term, I believe. Going back over the length of the tree, I and located the largest limbs, all of which were smaller than 1/2 an inch in diameter.
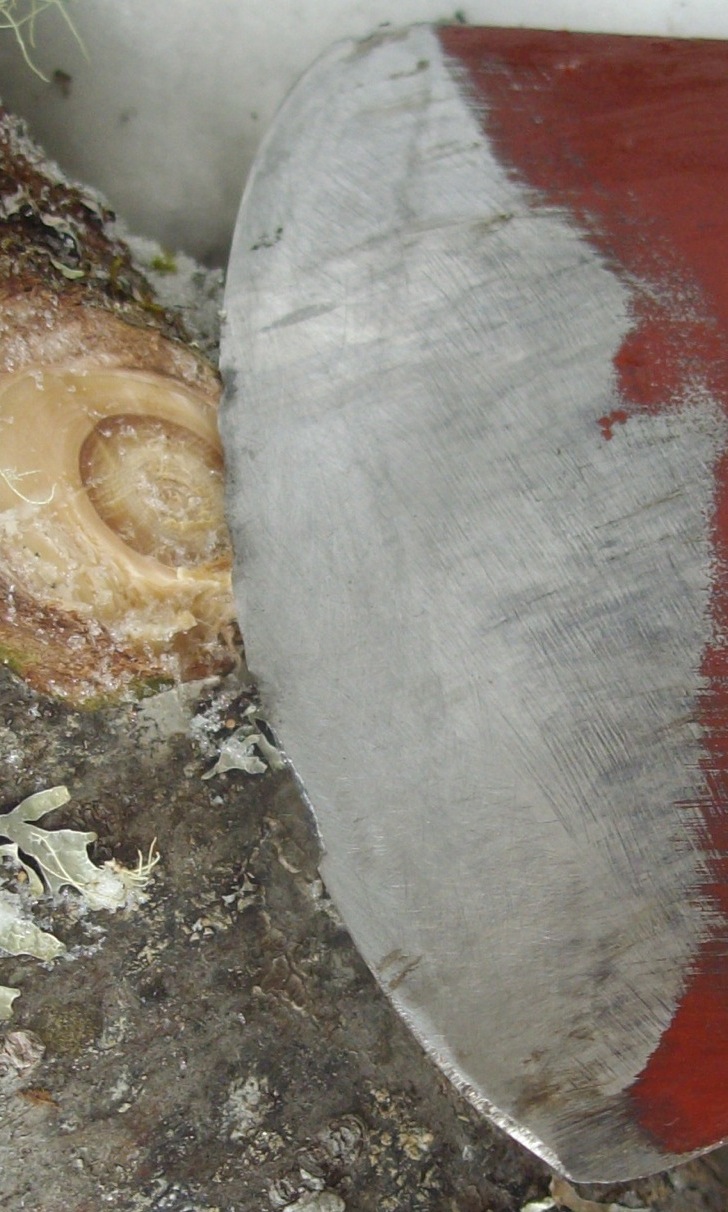
This is where I started feeling that I was in possession of a pretty unique little ax; I've never before heard of this happening. I am by no means knowledgeable when it comes to steel quality and forged tools in general, but I was under the impression that edge tools can sometimes be too hard, causing the steel to chip, or too soft, causing it to buckle or bend over. Never seen both at once though
Here's a closer look at the edge. Unique, all right!
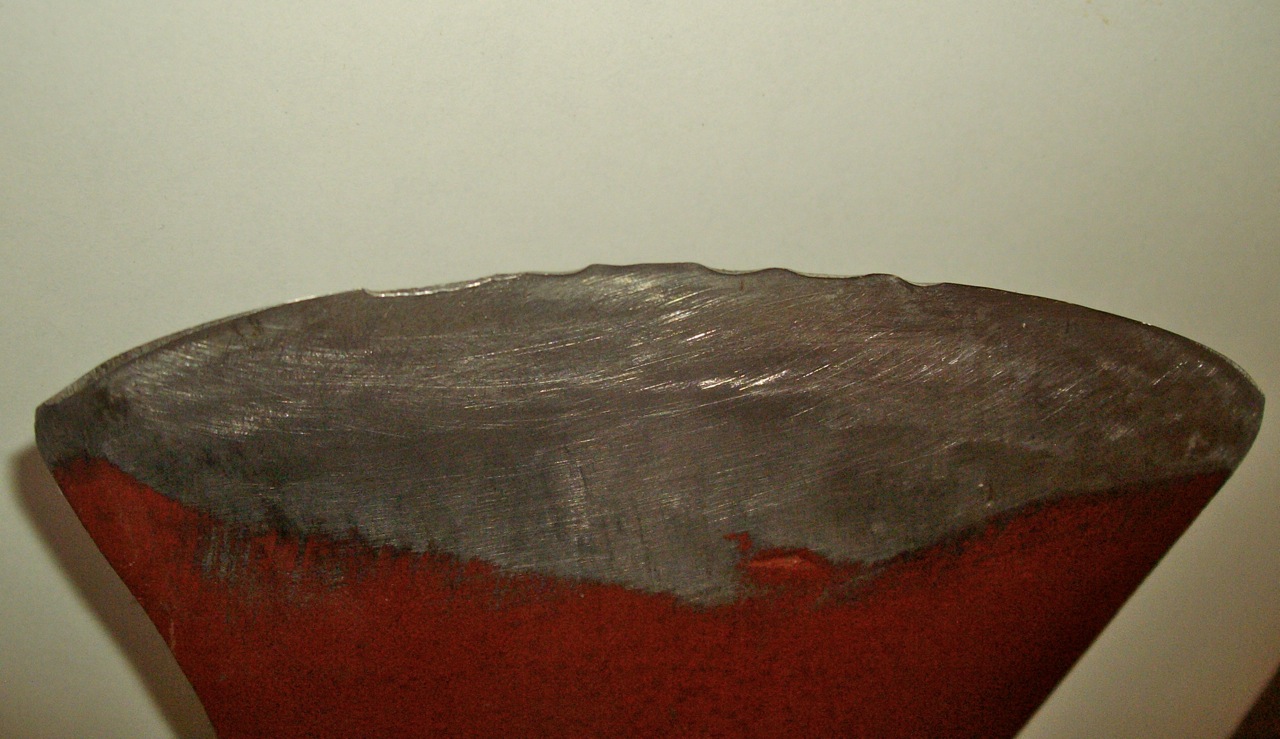
I had taken another ax along that day, a 2 3/4 lb. Swedish military surplus single bit on a 27" handle, with the edge filed down the way we like them. So before heading back home, I felled and limbed another fir with that one. The edge remained intact
Then for good measure I chopped down and limbed a third tree using only a kukri knife, a new one that a good friend had kindly sent for us to test out. The edge on this kukri was thinner than others I'd seen, but when put through the same treatment as the cruiser, it passed the test with flying colours, no damage whatsoever.
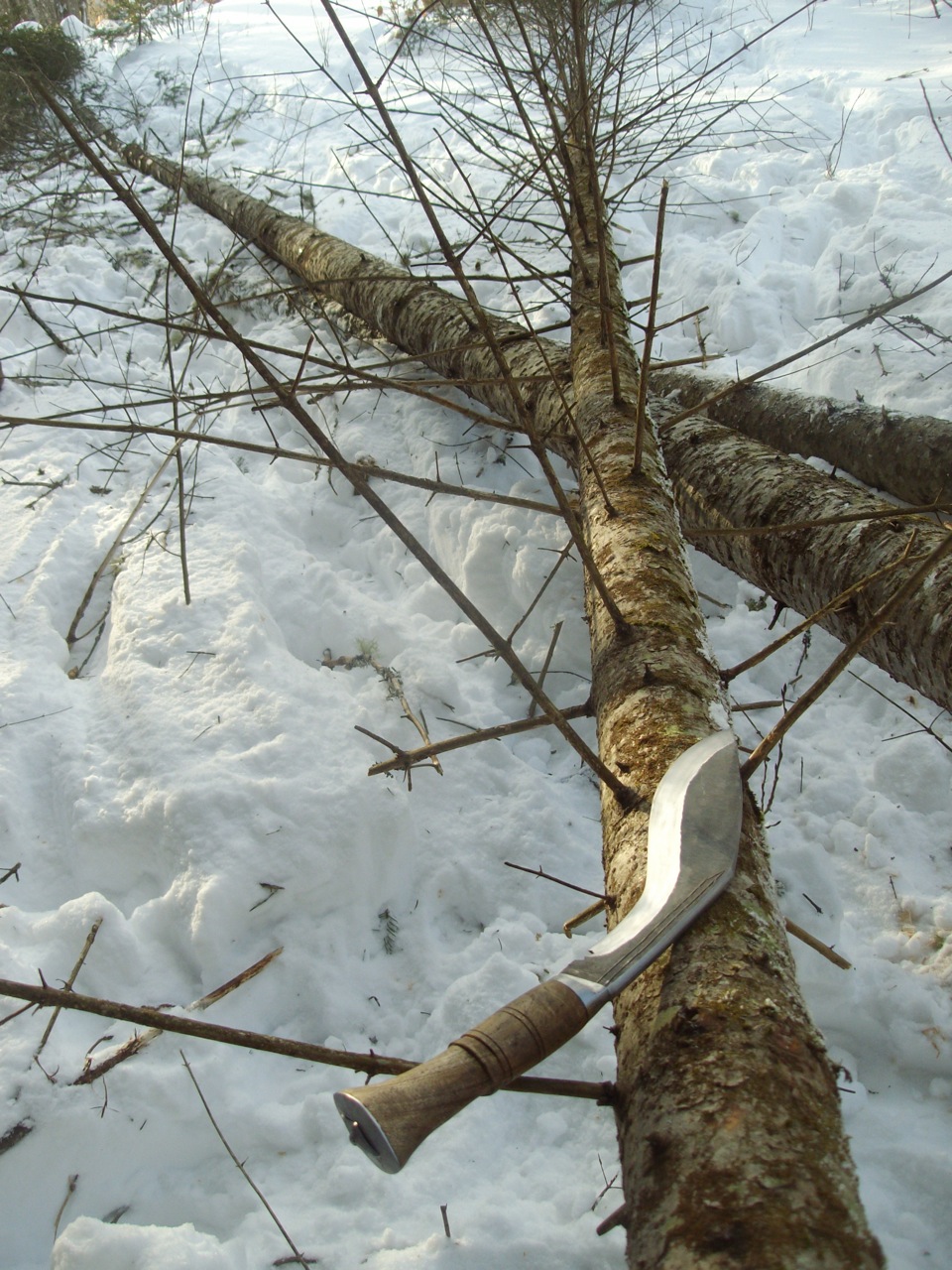
Thus I suspect that it can't have been only those 'tough' branches that were to blame
At Peter's suggestion I took the cruiser out again later on, this time using the opposite face. I had taken the burr off and smoothed the transition between the micro-bevel and the rest of the face but did no actual re-shaping. With it, I managed to take down a small green beech (with a great deal of effort, since the edge had virtually no penetration ability, unsurprisingly).
The next day Peter removed the damaged edge on the first face, leaving a thicker profile. By this time I had gotten tired of using that handle the way it had come from the factory, so I took a rasp to it and pretty much just removed the lacquer, then smoothed it down with a piece of glass.
I happened to think of taking photos of the labels on either side of the handle before removing them.
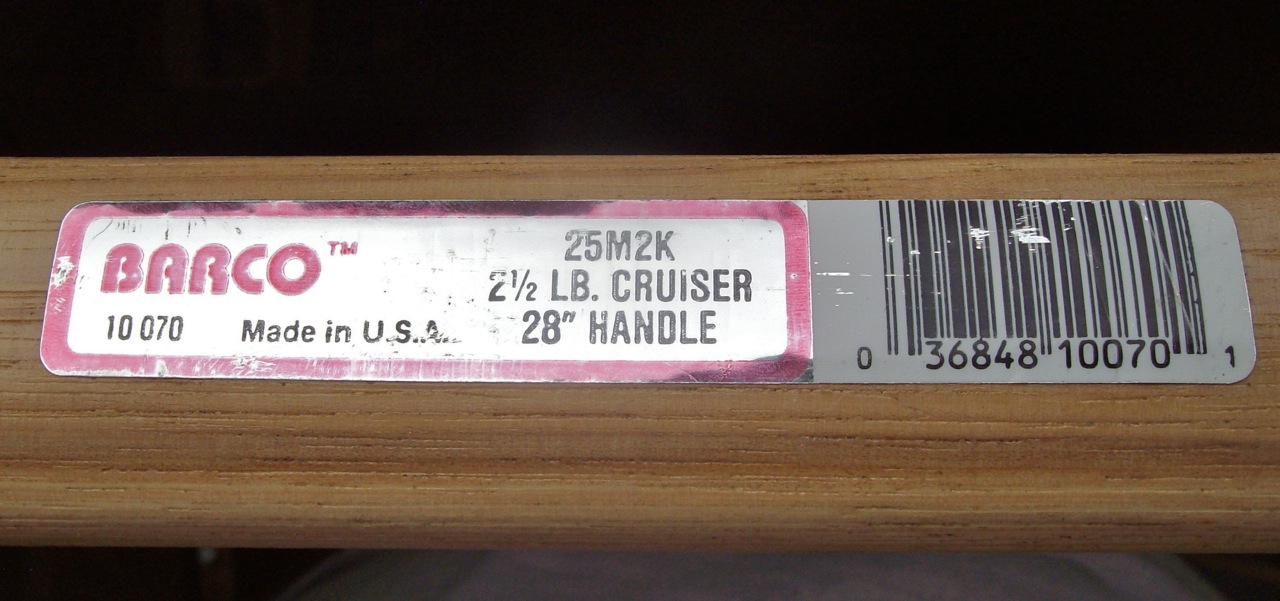
Good thing too, this one had a very important message, as I was soon to find out.
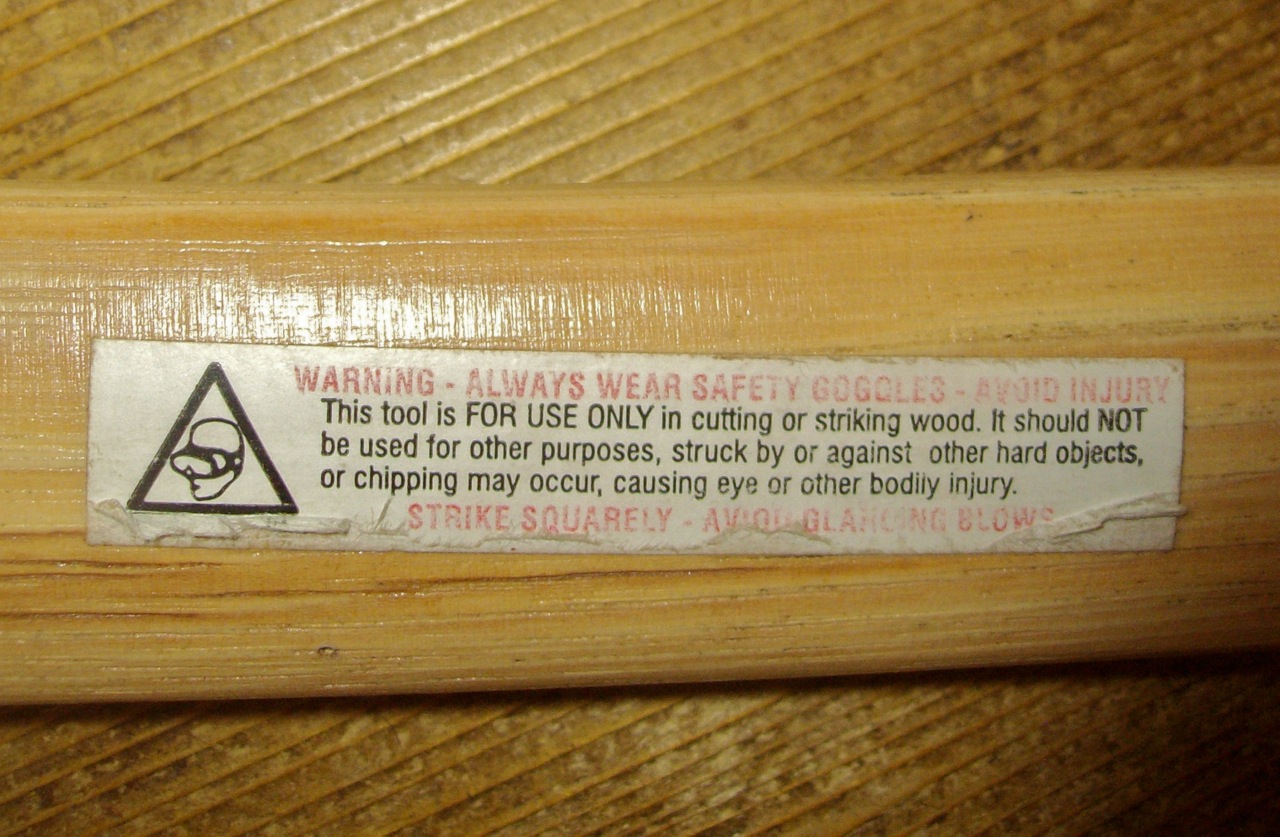
Not as thin as I'd like, but it sure felt better after being slightly flattened, with the lacquer removed.
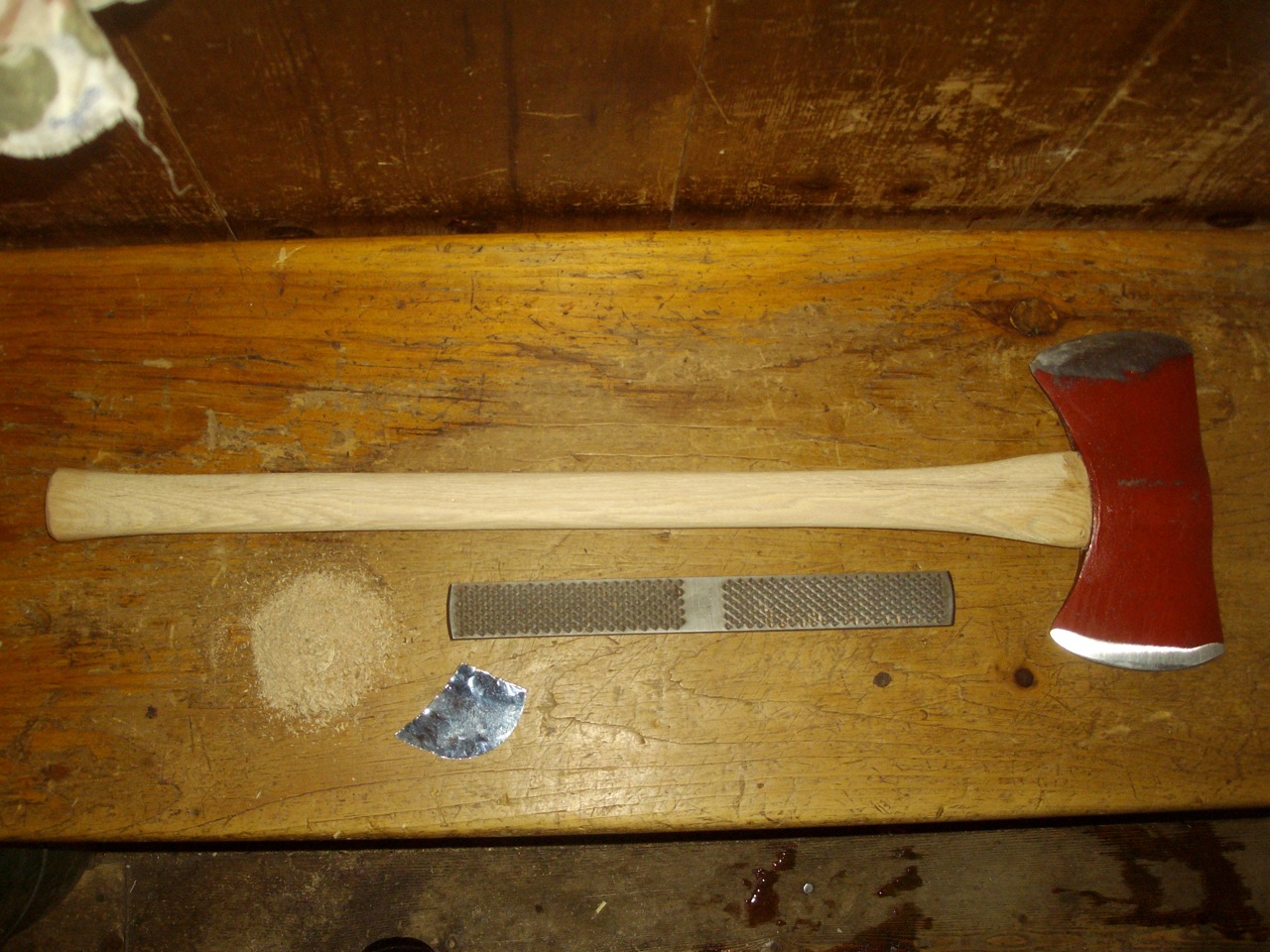
Then I headed off into to the woods and picked a medium-sized poplar to test it out on.
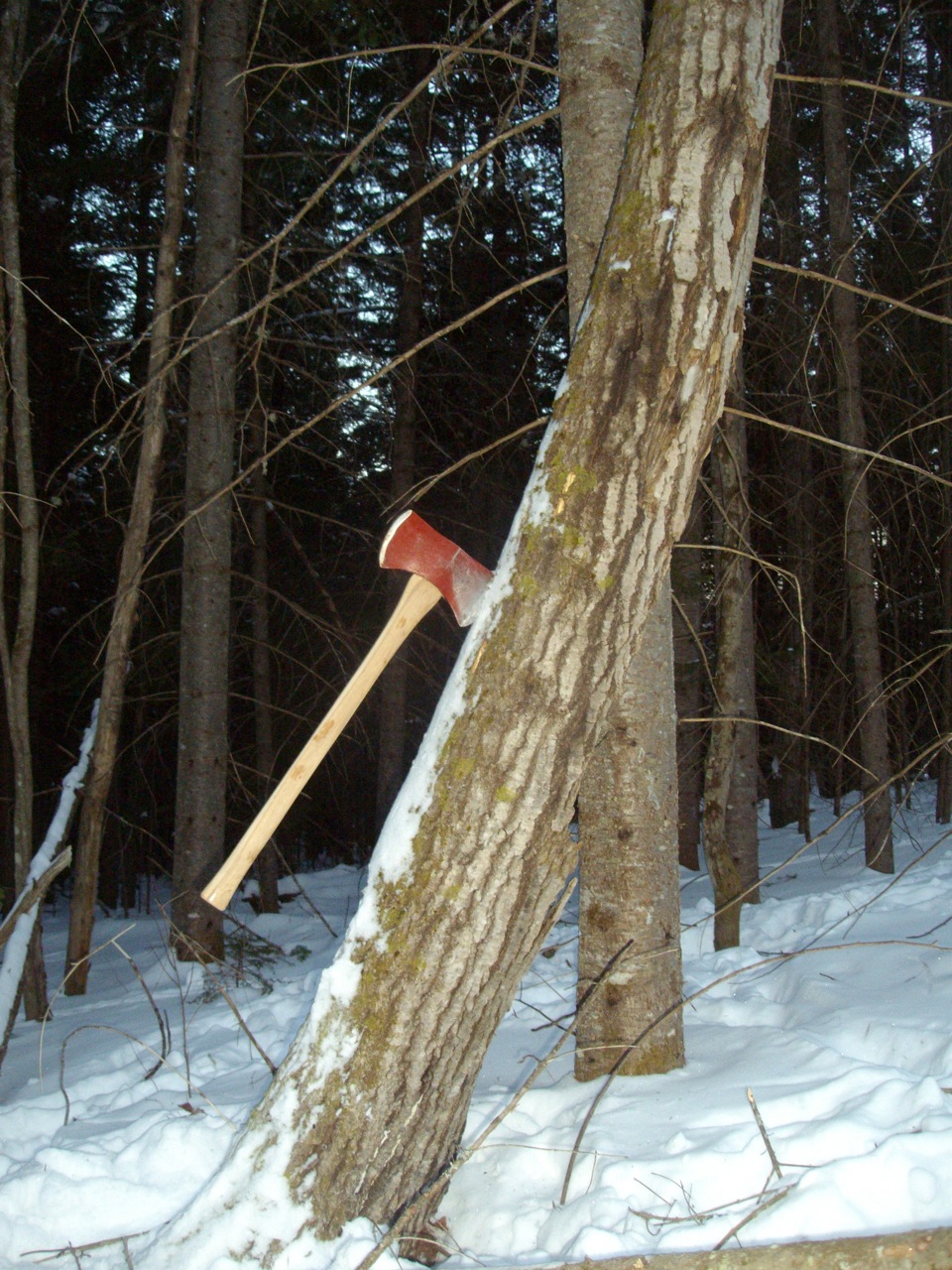
I was nearly done notching it, when I took another swing and the handle came back empty, with the head lying in the snow at the base of the tree. I just stared in disbelief. Nope, I hadn't overreached and hit the handle; that fine American hickory just couldn't take the combination of the soft green poplar wood and the girl swinging it. (Weren't these cruisers supposed to be used by grown men?)

The "wear safety goggles" is still faintly visible; now I understand... Shouldn't they have added "wear steel toe boots"?

I'd be interested in hearing some opinions on this one; have you ever seen such a porous-looking hickory?

Another thing we realized once the handle broke was that the wood was amazingly light, not even close to the weight of normal hickory. If we take Barco's word that the handle was USA hickory, not some strange Chinese wood that looks like an Aero Bar on the inside, then our tentative conclusions are that this wood had dry rot.
Okay, but we didn't give up on this ax yet; Peter knocked the remaining broken handle out of the eye, and quickly fitted it with a thiner (18mm) 30" maple handle. This time I tried splitting some firewood with the original (thick) face. This ax does not have an optimal splitting profile, but it worked fine with the "flick" technique I use.
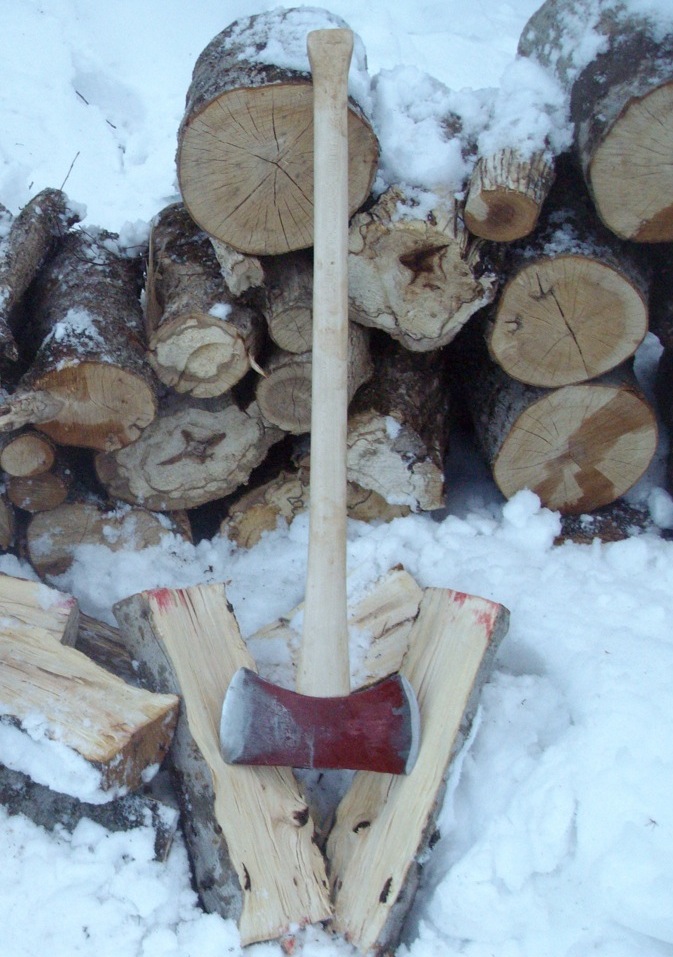
Then, with that new maple handle, I headed off to see what damage I could do next. Taking along the Swedish military surplus ax again, I did some comparisons of the chopping efficiency. Not a real fair comparison, but the Swedish ax's extra weight and the Barco's (now) longer handle balanced out a little bit.
I took down a pair of dying poplars, trying to make an unbiased comparison of the effort expended, then did the same with two larger firs. (One more strike against this "USA" cruiser: the steel has much poorer edge retention in comparison to all of the other axes I've been using; I could hardly believe how fast it dulled even while bucking poplar with no knots.)

The Swedish ax won, hands down. I chopped the trees down in approximately 1/3 less time, and as I limbed each of their respective firs, the Swedish ax left much cleaner cuts, while the cruiser tore the bark surrounding the limbs.

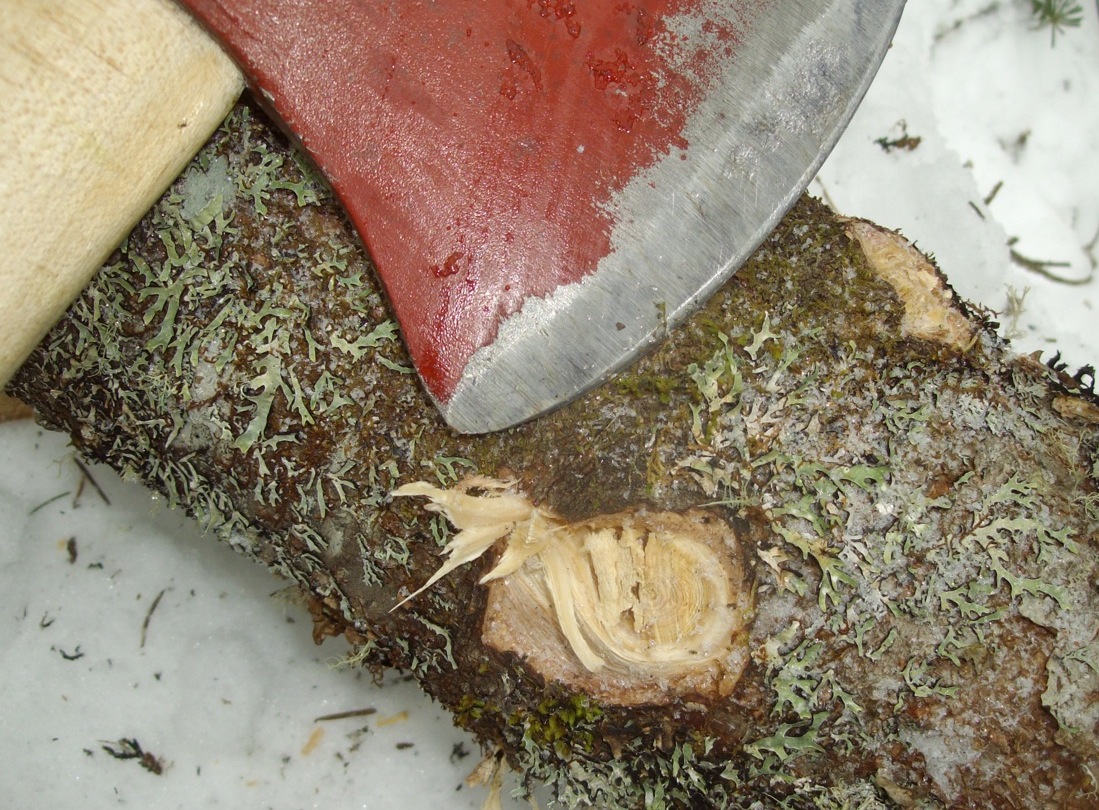
I wasn't happy with the edge on the cruiser (the one that had been thinned, damaged, filed off and left thicker) so in the spirit of second chances, Peter filed it down again, though not quite as thin as the first time. Again, I chopped down a couple firs, then carefully limbed them. Whew, no damage. Then I took down a tiny (green) fir to use as a pushing pole for the larger trees, and started limbing the 1/4" diameter branches. Whoops, there goes another piece of the edge! A few more cuss-words and I headed home, since I hadn't taken a back-up ax along that time.
That was the end of my using this ax for the time being. During the time that I was testing the Barco cruiser, I'd also been doing some chopping with several other axes of adequately thin edge profiles, none of which ever suffered torn edges and broken handles. I might add that the maple handle is still intact, after being put through tougher treatment than the hickory one lasted long enough to endure...
So, would I recommend this ax to anyone based on my experiences? Com'on, now, do I really have to answer that one?