Hengelo_77
Basic Member
- Joined
- Mar 2, 2006
- Messages
- 6,221
I keep having problems with the pivot pin not disappearing. Grinding after hamering it looks gone but it comes back when I get to the finer grits.
I use a 50:1 conical reamer to remove a very small amount of material and I think that the pin expands at the surface but doesn't fill the cavity a bit deeper.
Is it my hamering technique that causes this?
I grind the sides of the pin with 400 grit. I knocked it back up. It is shiny at the top but the cavity goes deeper. So I think there was a hollow under the shiny part.
Black = bolster
Red = pin
Yellow = cavity as I suspect
What do I do wrong?
I use a 50:1 conical reamer to remove a very small amount of material and I think that the pin expands at the surface but doesn't fill the cavity a bit deeper.
Is it my hamering technique that causes this?
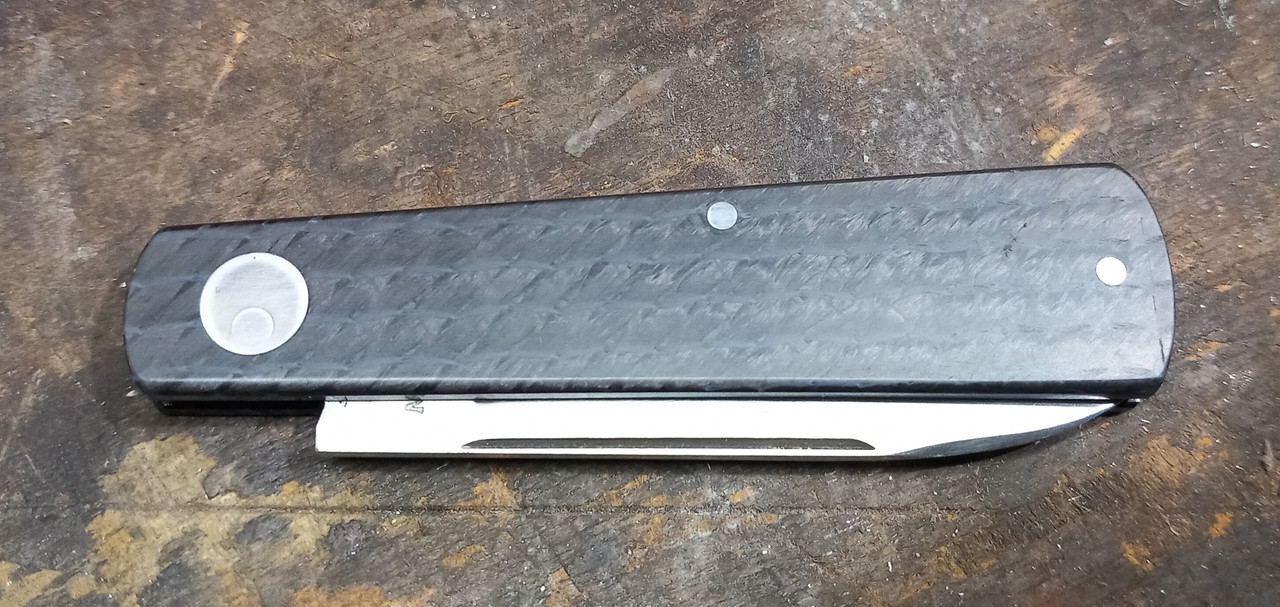
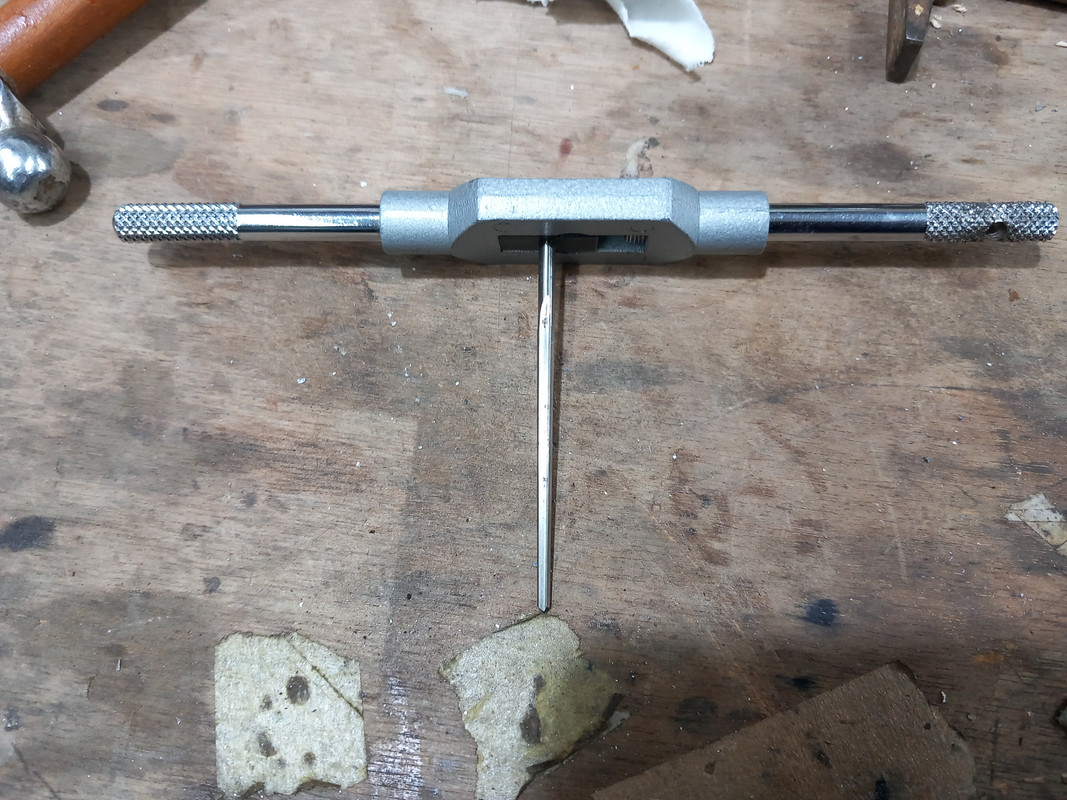
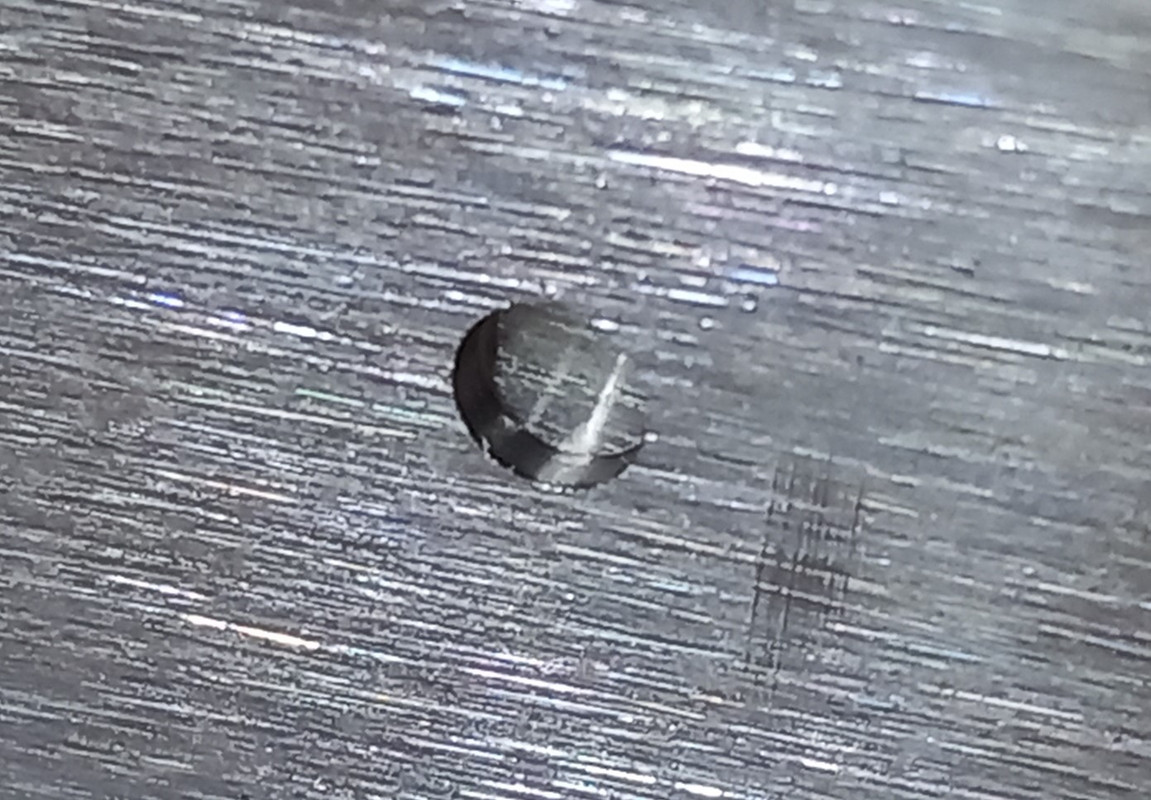
I grind the sides of the pin with 400 grit. I knocked it back up. It is shiny at the top but the cavity goes deeper. So I think there was a hollow under the shiny part.
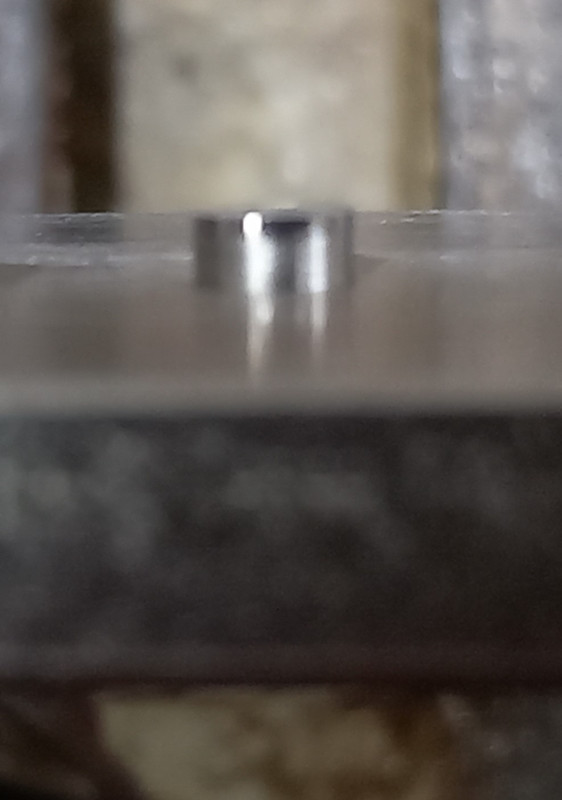
Black = bolster
Red = pin
Yellow = cavity as I suspect
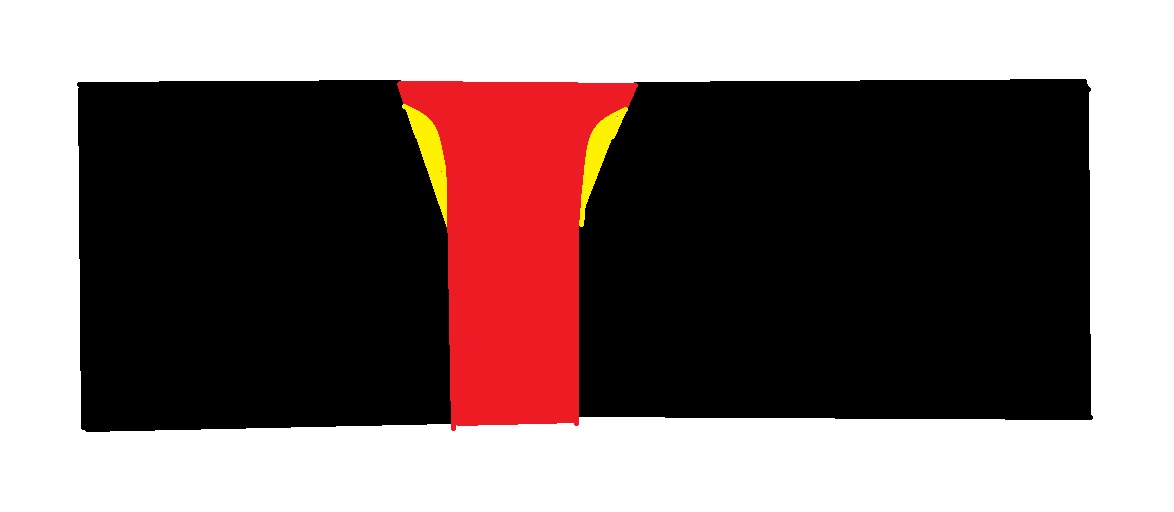
What do I do wrong?