JRB Blades
Knifemaker / Craftsman / Service Provider
- Joined
- Jul 22, 2013
- Messages
- 266
Now it's time to cut the lockbar and mill the lock relief. This takes about 30-40 min per blade, so I'll be done this weekend when I get some more shop time. I did two of them already and thought I'd go ahead and include this portion now. I use .025" cutoff discs from McMaster Carr along with their 1/16" wheel arbor.
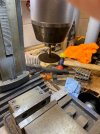
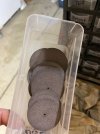
I place two drill bits in the holes that I drilled out for the ends of the lock bar. Then I place the handle scale in the vice with a couple of parralells stacked on top of each other. I set the drill bits on top of the handle scales and tighten the vice. Now my handle scale is level and even.
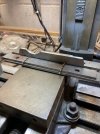
I run the mill at 2500RPM and take it slow to cut the lock bar relief. If you're careful, the disc won't break although they are pretty fragile.
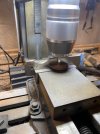
Once the lock bar is cut, I use a 5/16" carbide ball nosed end mill to mill the lockbar relief. Running at about 700RPM, I take about .005-.008" cuts using the DRO to make sure I am not taking too much of a bite at once. My little mill can't handle much more than that. We are shooting to get the "webbing" on the lock bar relief around .045" so we have good tension on the lockbar but not so much that it's a bear to unlock.
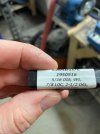
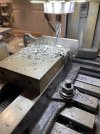
When the relief is finally cut, the cut in our lockbar is covered with the effects of milling our lock bar relief. Since the scale is still secured in the vice, I use the cutoff wheel to re-open that lockbar cut. After that I'll take it to the drill press and re-open the hole at the end of the lockbar relief with my 5/64" drill bit.
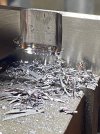
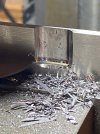
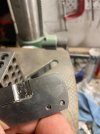
Looks like we are pretty close to our .045" target!
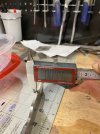
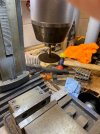
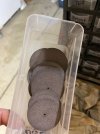
I place two drill bits in the holes that I drilled out for the ends of the lock bar. Then I place the handle scale in the vice with a couple of parralells stacked on top of each other. I set the drill bits on top of the handle scales and tighten the vice. Now my handle scale is level and even.
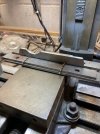
I run the mill at 2500RPM and take it slow to cut the lock bar relief. If you're careful, the disc won't break although they are pretty fragile.
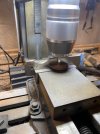
Once the lock bar is cut, I use a 5/16" carbide ball nosed end mill to mill the lockbar relief. Running at about 700RPM, I take about .005-.008" cuts using the DRO to make sure I am not taking too much of a bite at once. My little mill can't handle much more than that. We are shooting to get the "webbing" on the lock bar relief around .045" so we have good tension on the lockbar but not so much that it's a bear to unlock.
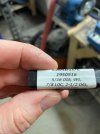
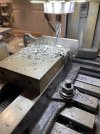
When the relief is finally cut, the cut in our lockbar is covered with the effects of milling our lock bar relief. Since the scale is still secured in the vice, I use the cutoff wheel to re-open that lockbar cut. After that I'll take it to the drill press and re-open the hole at the end of the lockbar relief with my 5/64" drill bit.
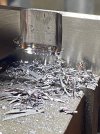
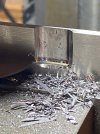
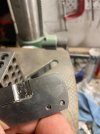
Looks like we are pretty close to our .045" target!
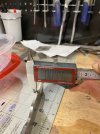