- Joined
- Feb 24, 2000
- Messages
- 1,877
This is a very informative post.
I like my hamons to be dark above the temper line. To get this, I use Rutlands stove cement for clay. After heat treat I dip in 1part FeCl and 3 parts water several times and scrub the blade with 0000 steel wool between etches. Then I use make up pads and use 1500 silican carbide. I concentrate on the bottom part of the blade.
It takes a total of maybe 20 minutes to get this result. For what I sell my knives for I don't want to spend a lot of time bringing out the hamon.
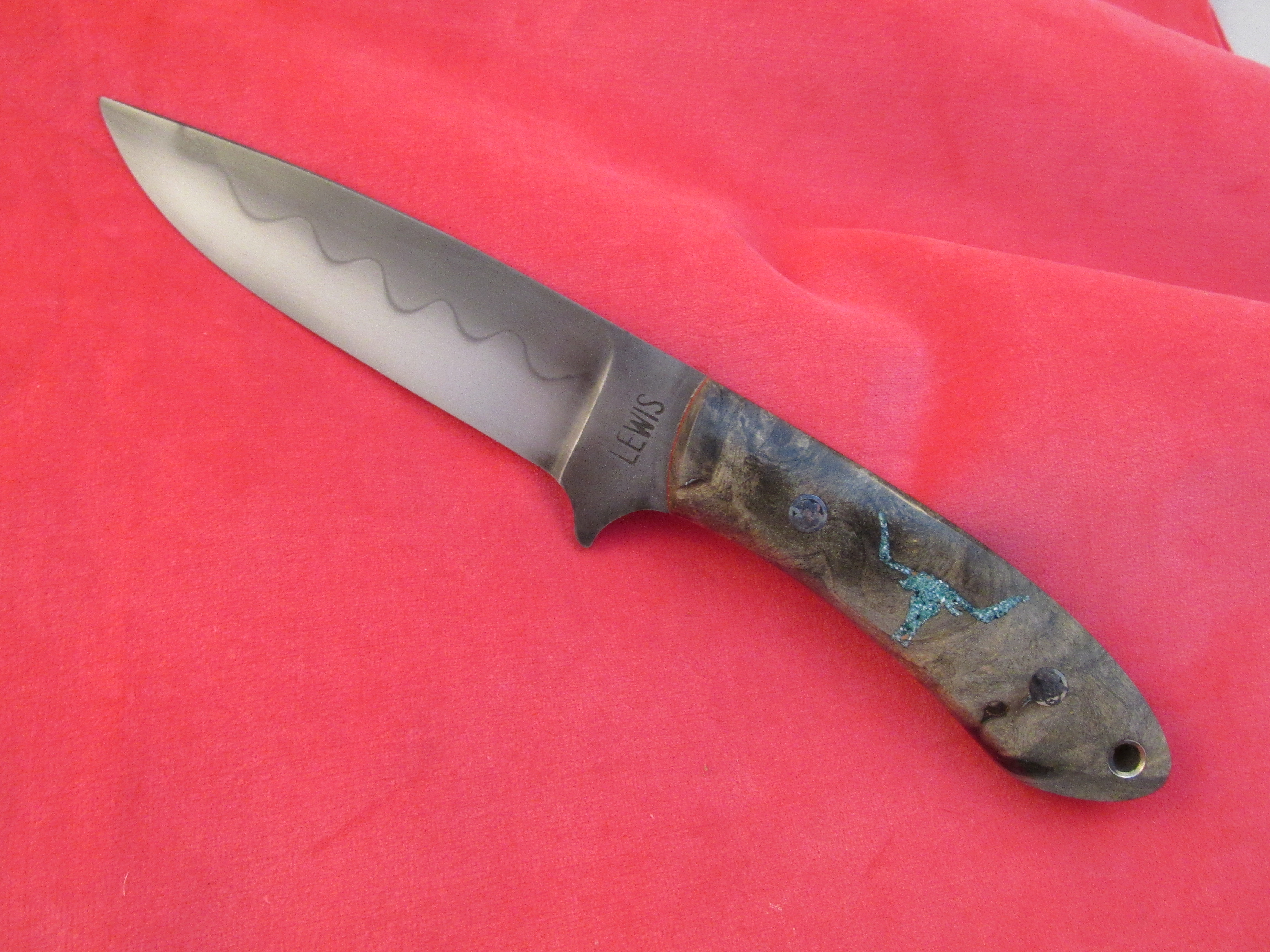
I like my hamons to be dark above the temper line. To get this, I use Rutlands stove cement for clay. After heat treat I dip in 1part FeCl and 3 parts water several times and scrub the blade with 0000 steel wool between etches. Then I use make up pads and use 1500 silican carbide. I concentrate on the bottom part of the blade.
It takes a total of maybe 20 minutes to get this result. For what I sell my knives for I don't want to spend a lot of time bringing out the hamon.