- Joined
- Mar 12, 2013
- Messages
- 1,167
Hey guys!
I make kydex sheaths for all my knives as I'm a fan of it's low maintenance and also the ability to do without straps/clips for knife retention, however I'm not a fan of all the fancy belt attachment methods out there (Tek-lock, etc...). With that in mind I've been looking for a nice way to do a belt loop from webbing, in order to keep with the low-maintenance setup of my knives.
I haven't seen too many people using webbing for belt loops so I though I'd share what I've learnt, as it turns out there's a bunch of leg-work to get the right stuff!
1) It's very hard to find webbing that's the right stiffness for a solid belt loop. Most webbing, even the stuff suppliers describe as 'stiff', is actually quite supple. I wanted webbing with a stiffness close to that of 7-8oz leather in order to make sure that the sheath wouldn't flop about. I bought several hundred yards of many different types of webbing from several suppliers before finding something that worked. This webbing from Lowy is what I'm using, it's inexpensive, extremely strong and it's also the stiffest I was able to find:
http://www.lowyusa.com/wbscu112
Unfortunately you have to buy a minimum of 50 yards, luckily it's not too expensive. If you're making a bunch of knives it definitely seems like it's worth it even though you have to buy in bulk.
2) Cutting the webbing and keeping edges that are acceptably neat is not super hard to do, but it's non-obvious how to get the cleanest result. I initially tried making a hot-knife that would form the end and also round the edges in one go. Unfortunately when you use a hot-knife you get significant build-up of melted plastic at the edge and it looks unprofessional. I tried cutting with a hobby knife and then cauterizing the frayed end but that ended up quite ragged.
What worked in the end was to use the belly of a sharp knife to saw through the webbing while it's laid flat on a cutting mat. The downward pressure applied over a wide area seems to stop any fraying. You can then run the flame from a ligher over the cut end quickly and end up with a very neat result.
3) Attaching the webbing to the sheath in a clean and sturdy way: I tried a number of different methods, but in the end simple #8-9 rivets worked the best. The rivets are put through holes in the webbing that are created by burning through the webbing with a piece of very hot 1/4" steel rod.
Leather would definitely be an easier option to be honest, but I'm convinced that the webbing will prove to be a good choice with it's weather resistance and strength.
Here's some photos of the finished product. I still need to test that the little kydex attachment plate is strong enough, but I'm very happy with how it's worked out otherwise. The stiff belt loop mounted near the mid-point on the sheath very much stays out of your way, and does not flap or swing even when running.
Feedback and criticism welcomed! If anyone else is using webbing for belt loops I'd love to hear of your experiences!
-Aaron
I make kydex sheaths for all my knives as I'm a fan of it's low maintenance and also the ability to do without straps/clips for knife retention, however I'm not a fan of all the fancy belt attachment methods out there (Tek-lock, etc...). With that in mind I've been looking for a nice way to do a belt loop from webbing, in order to keep with the low-maintenance setup of my knives.
I haven't seen too many people using webbing for belt loops so I though I'd share what I've learnt, as it turns out there's a bunch of leg-work to get the right stuff!
1) It's very hard to find webbing that's the right stiffness for a solid belt loop. Most webbing, even the stuff suppliers describe as 'stiff', is actually quite supple. I wanted webbing with a stiffness close to that of 7-8oz leather in order to make sure that the sheath wouldn't flop about. I bought several hundred yards of many different types of webbing from several suppliers before finding something that worked. This webbing from Lowy is what I'm using, it's inexpensive, extremely strong and it's also the stiffest I was able to find:
http://www.lowyusa.com/wbscu112
Unfortunately you have to buy a minimum of 50 yards, luckily it's not too expensive. If you're making a bunch of knives it definitely seems like it's worth it even though you have to buy in bulk.
2) Cutting the webbing and keeping edges that are acceptably neat is not super hard to do, but it's non-obvious how to get the cleanest result. I initially tried making a hot-knife that would form the end and also round the edges in one go. Unfortunately when you use a hot-knife you get significant build-up of melted plastic at the edge and it looks unprofessional. I tried cutting with a hobby knife and then cauterizing the frayed end but that ended up quite ragged.
What worked in the end was to use the belly of a sharp knife to saw through the webbing while it's laid flat on a cutting mat. The downward pressure applied over a wide area seems to stop any fraying. You can then run the flame from a ligher over the cut end quickly and end up with a very neat result.
3) Attaching the webbing to the sheath in a clean and sturdy way: I tried a number of different methods, but in the end simple #8-9 rivets worked the best. The rivets are put through holes in the webbing that are created by burning through the webbing with a piece of very hot 1/4" steel rod.
Leather would definitely be an easier option to be honest, but I'm convinced that the webbing will prove to be a good choice with it's weather resistance and strength.
Here's some photos of the finished product. I still need to test that the little kydex attachment plate is strong enough, but I'm very happy with how it's worked out otherwise. The stiff belt loop mounted near the mid-point on the sheath very much stays out of your way, and does not flap or swing even when running.

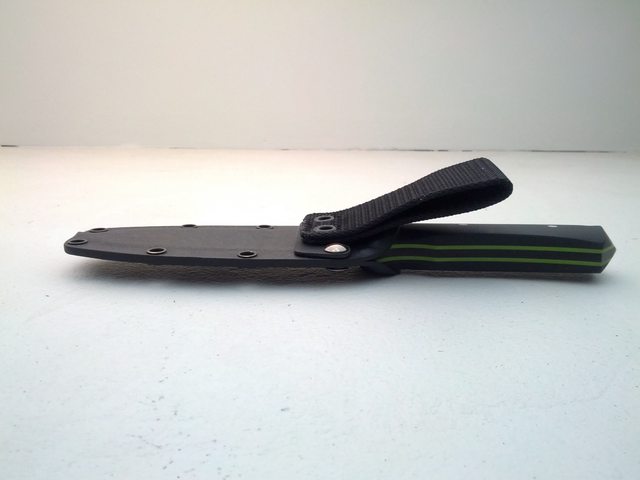
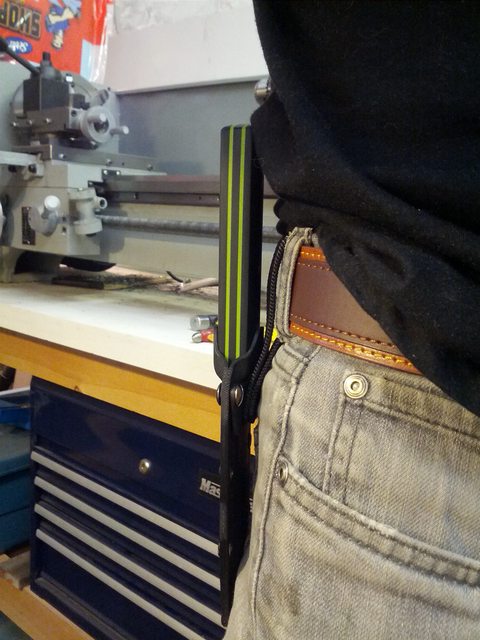

Feedback and criticism welcomed! If anyone else is using webbing for belt loops I'd love to hear of your experiences!
-Aaron