- Joined
- Apr 22, 2011
- Messages
- 460
UPDATE!
OK as promised here are pics of the grinds before I send them of for heat treating. I'd did these a bit different than the prototype and they look fantastic! Firstly I ground the swedges before I did the main bevels. This was MUCH easier and the result was faster and more accurate. Secondly since this is 3V and not 5160 like the prototype I am sending them off to be heat treated and can get away with a much more refined edge. This time around I went to 40 thousandths on the edge so the secondary bevel wont be a ridiculously massive as it was on the prototype. I started with a 12 deg bevel and then stepped it down to 8 deg and finally finished at 4.5 deg.
After grinding it all out I just wasn't satisfied with the surface finish of the carbide counter bore that milled the bearing pockets. For this flipper to be silky smooth BOTH surfaces that the roller bearings contact must be parallel and smooooth. To make it all perfect I turned down a 2" sanding disk kit to 11/16" on the lathe and used the laser cutter to cut 11/16" disks of adhesive backed sandpaper in 60,120, and 220 grits. Now I can chuck up the custom sized surface grinding wheel and smooth out the bearing pockets.
Next step is to get the handles sanded down, reamed to size, and tapped for pocket clips. Then I'll make the pocket clips and do all the finished surfaces in preparation for the blades to come back from heat treating. Everything looks good and on track!
OK as promised here are pics of the grinds before I send them of for heat treating. I'd did these a bit different than the prototype and they look fantastic! Firstly I ground the swedges before I did the main bevels. This was MUCH easier and the result was faster and more accurate. Secondly since this is 3V and not 5160 like the prototype I am sending them off to be heat treated and can get away with a much more refined edge. This time around I went to 40 thousandths on the edge so the secondary bevel wont be a ridiculously massive as it was on the prototype. I started with a 12 deg bevel and then stepped it down to 8 deg and finally finished at 4.5 deg.
After grinding it all out I just wasn't satisfied with the surface finish of the carbide counter bore that milled the bearing pockets. For this flipper to be silky smooth BOTH surfaces that the roller bearings contact must be parallel and smooooth. To make it all perfect I turned down a 2" sanding disk kit to 11/16" on the lathe and used the laser cutter to cut 11/16" disks of adhesive backed sandpaper in 60,120, and 220 grits. Now I can chuck up the custom sized surface grinding wheel and smooth out the bearing pockets.
Next step is to get the handles sanded down, reamed to size, and tapped for pocket clips. Then I'll make the pocket clips and do all the finished surfaces in preparation for the blades to come back from heat treating. Everything looks good and on track!
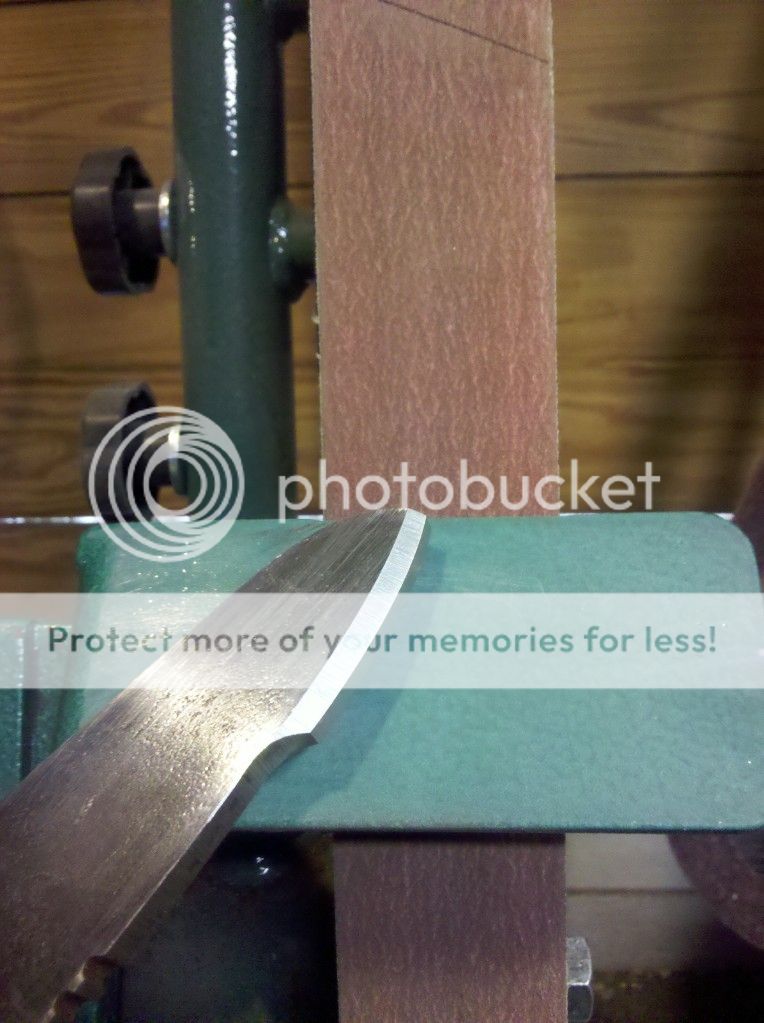

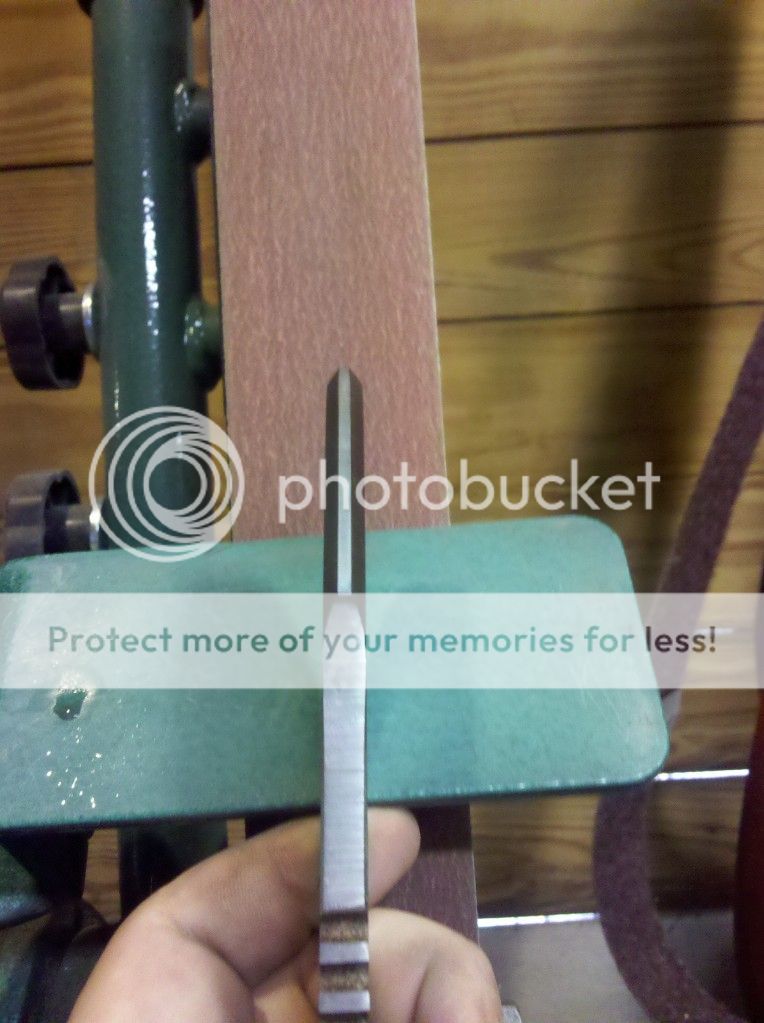
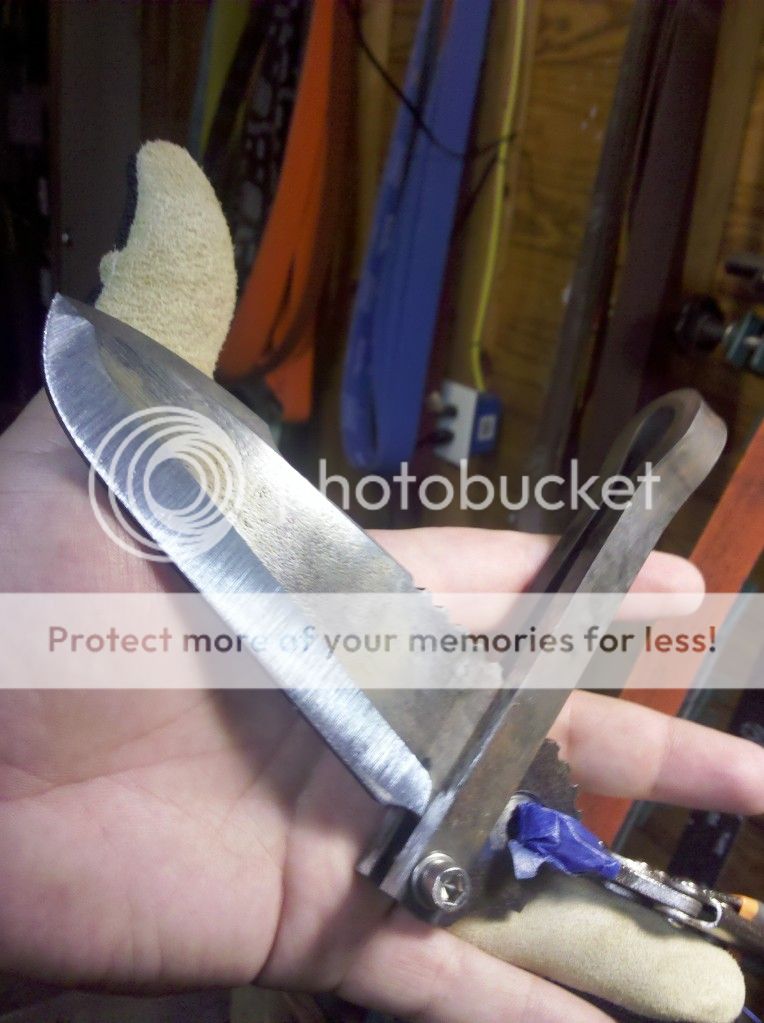



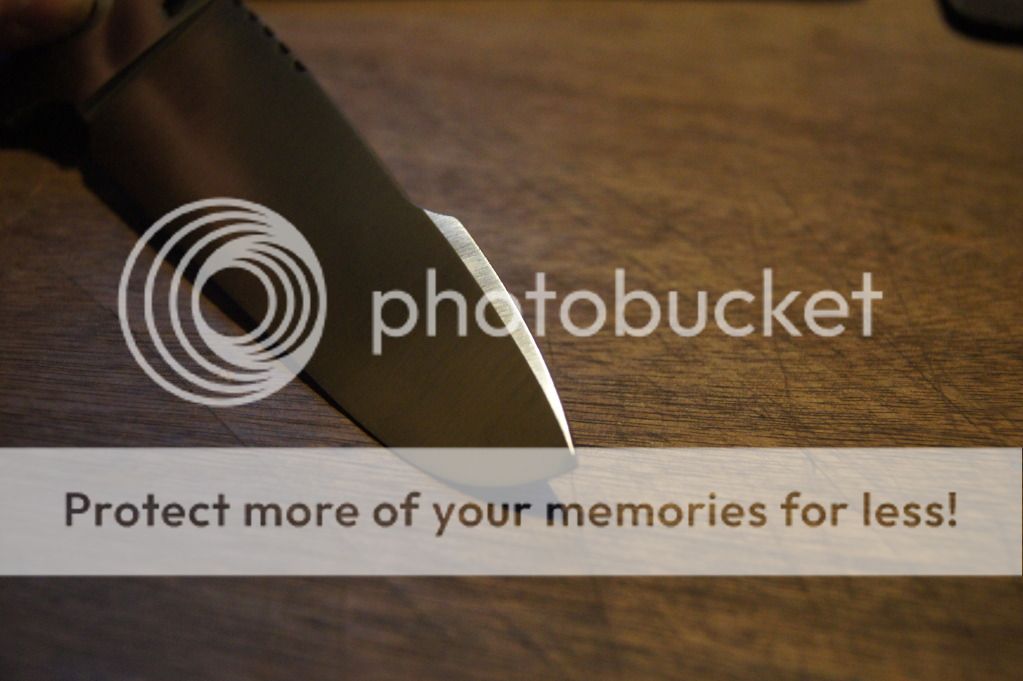



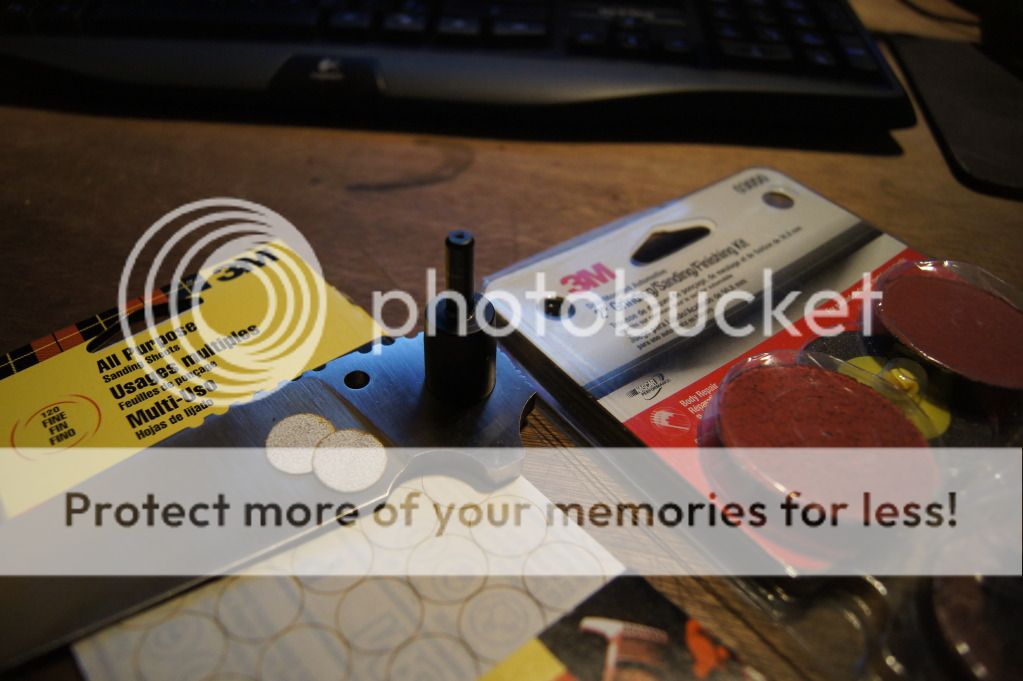