- Joined
- Sep 16, 2015
- Messages
- 157
D2 is some other worldly stuff. Seems like its cracking on the edges. Even trying to leave the billet to cool off in the forge.
Got a good forge weld:
But i can't figure out why its still cracking:
It requires me to dig into the billet to remove the cracks:
On a side note, I am convinced this is going to work to grind billets flat:
Not as much with the diamond wheel, but a cup style grinder.
Got a good forge weld:
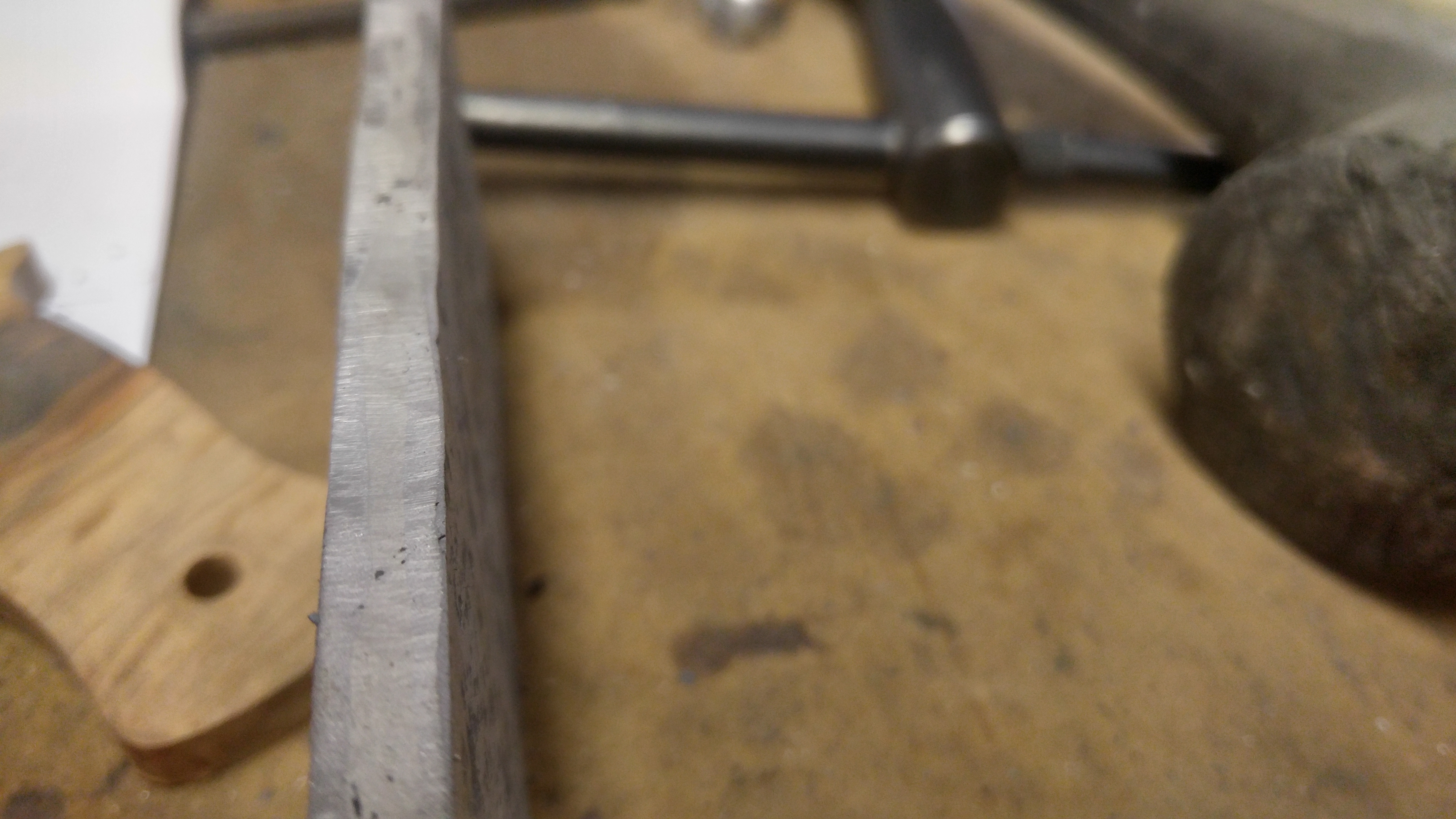
But i can't figure out why its still cracking:
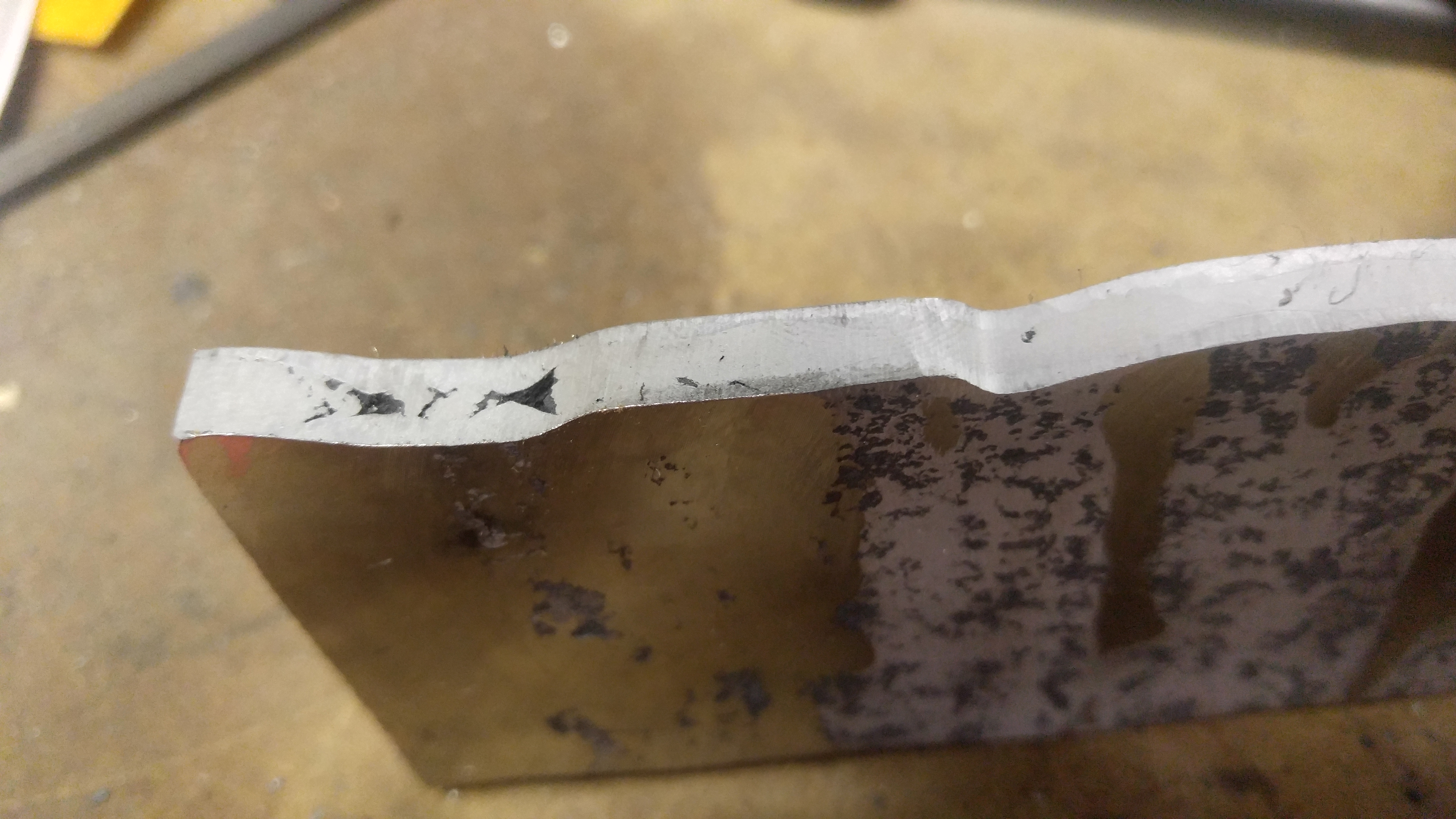
It requires me to dig into the billet to remove the cracks:
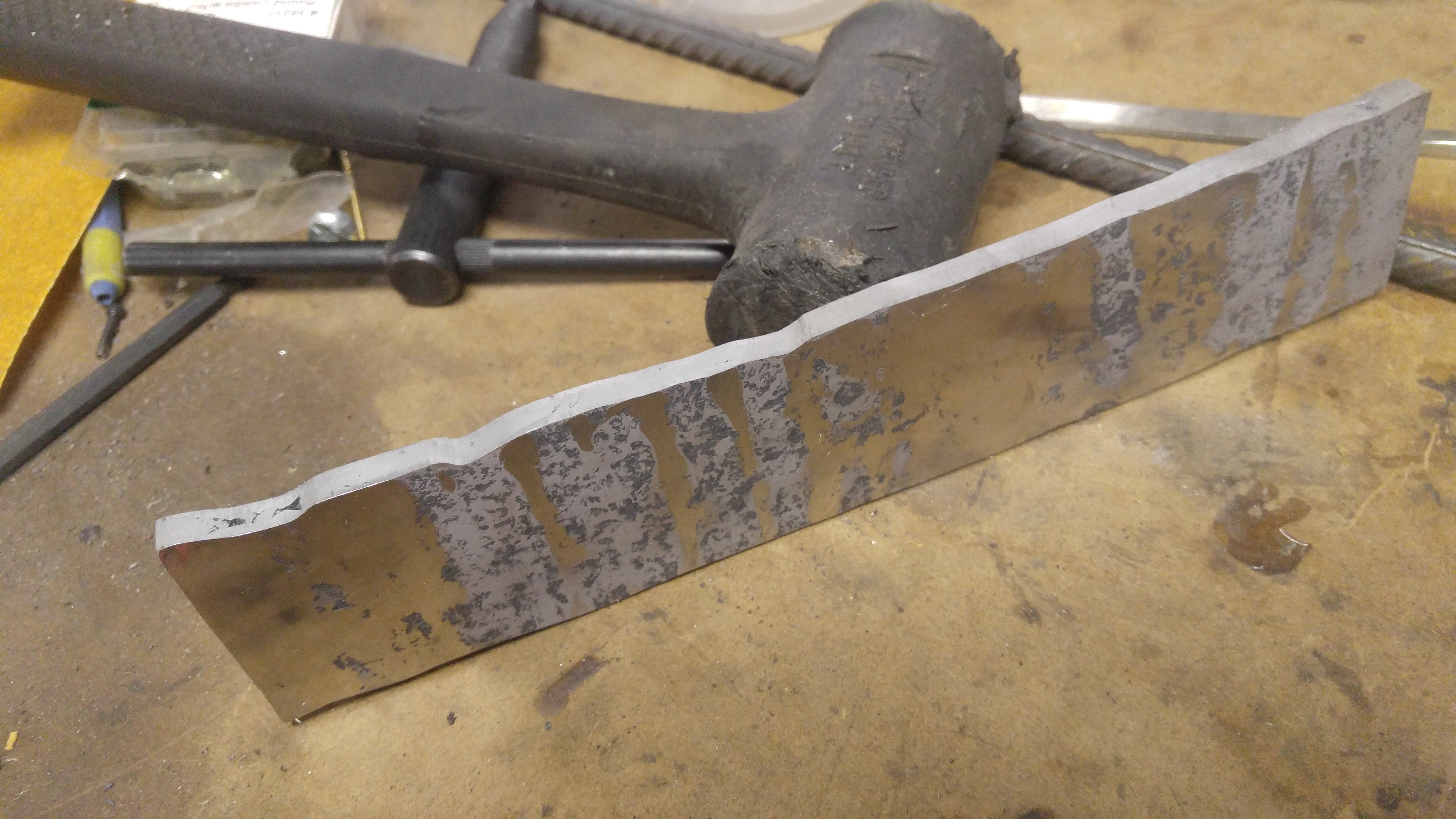
On a side note, I am convinced this is going to work to grind billets flat:

Not as much with the diamond wheel, but a cup style grinder.