Gareth Bull
BANNED
- Joined
- Apr 6, 2012
- Messages
- 107
I thought Id do a pictorial of a linerlock Im making, might be useful to some, so here we go:
Here are the basic parts, roughly cut out. Theyre all a little oversized so I can grind them all down together for a tight fit.
Step 1 is drilling all the holes in one of the liners; Im using UNF-080 screw so I drill with a 1.25mm drillbit:
Step 2 is transferring those holes into the opposite liner. I clamp them together with a piece of G10 underneath for rigidity and also something for the drill to pop out the titanium into, that way I wont drill into my clamps.
Step 3 is enlarging the holes in one scale to allow the screws to pass though easily, I used a 1.5mm drillbit here. I also countersunk the holes to accommodate the heads of the screws.
Now you can tap the liner with the smaller holes. This is a brilliant tapping jig that keeps everything absolutely perpendicular and stable, UNF-080 taps break very easily, this tool makes them last for ages. Only tap the holes you need for the next step (pivot and backstrap holes in this case) you'll need to pass a drillbit through the bolster and handle material holes later and if they were tapped you might ruin the threads.
Now that the holes are tapped, I screw the two liners together and sand them down so they match.
Next I grind a bevel on the titanium bolsters and a matching angle on the micarta. This creates a dovetail which helps keep the handle material down and looks great when you radius the handle later on. I set the rest on my disc sander to 45 degrees and grind the parts to a blade edge. I step the grits up to 600 so the parts fit tightly.
Here are the dovetailed parts; you can see how theyll fit.
Here are the basic parts, roughly cut out. Theyre all a little oversized so I can grind them all down together for a tight fit.

Step 1 is drilling all the holes in one of the liners; Im using UNF-080 screw so I drill with a 1.25mm drillbit:

Step 2 is transferring those holes into the opposite liner. I clamp them together with a piece of G10 underneath for rigidity and also something for the drill to pop out the titanium into, that way I wont drill into my clamps.


Step 3 is enlarging the holes in one scale to allow the screws to pass though easily, I used a 1.5mm drillbit here. I also countersunk the holes to accommodate the heads of the screws.

Now you can tap the liner with the smaller holes. This is a brilliant tapping jig that keeps everything absolutely perpendicular and stable, UNF-080 taps break very easily, this tool makes them last for ages. Only tap the holes you need for the next step (pivot and backstrap holes in this case) you'll need to pass a drillbit through the bolster and handle material holes later and if they were tapped you might ruin the threads.

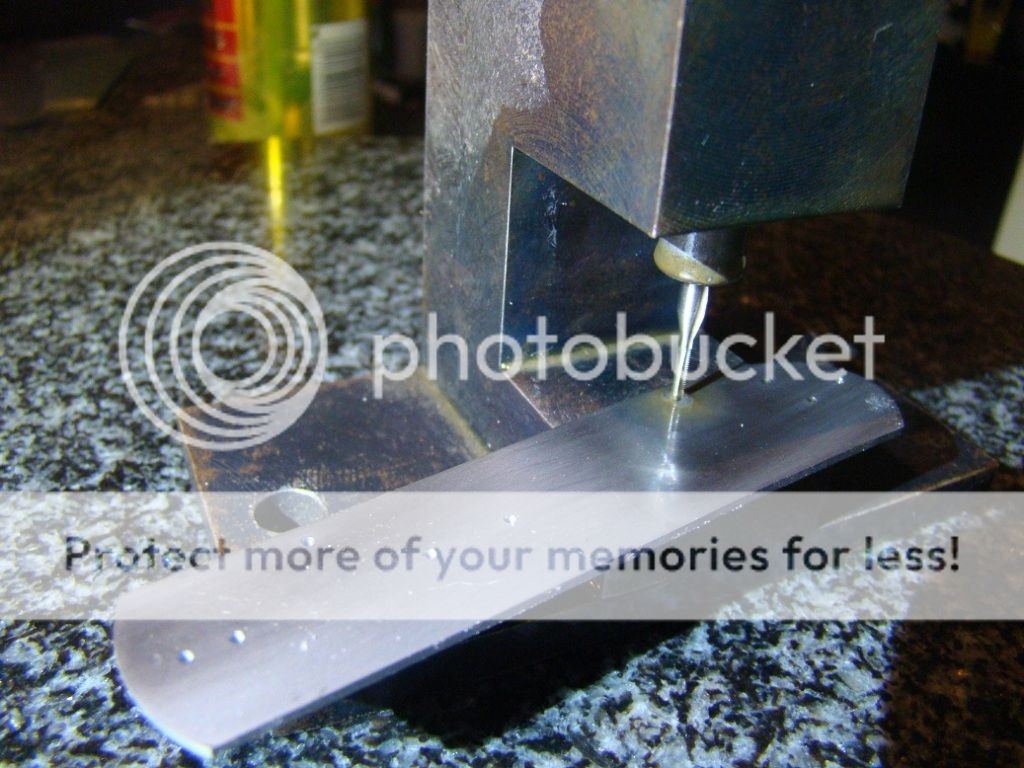
Now that the holes are tapped, I screw the two liners together and sand them down so they match.
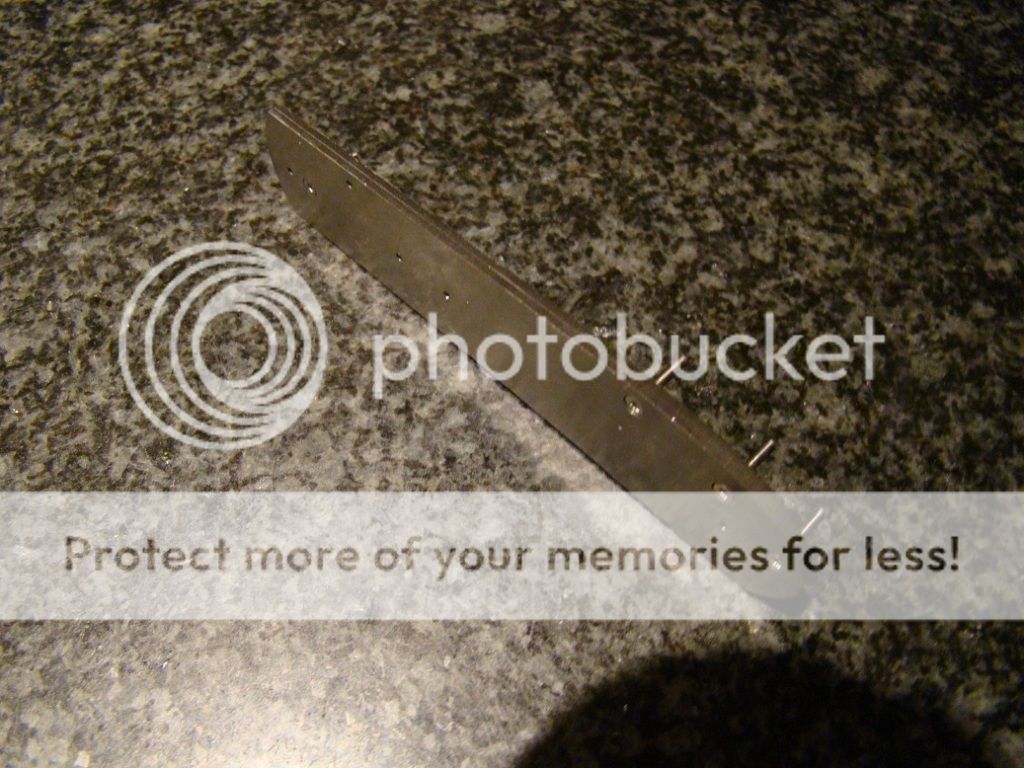

Next I grind a bevel on the titanium bolsters and a matching angle on the micarta. This creates a dovetail which helps keep the handle material down and looks great when you radius the handle later on. I set the rest on my disc sander to 45 degrees and grind the parts to a blade edge. I step the grits up to 600 so the parts fit tightly.
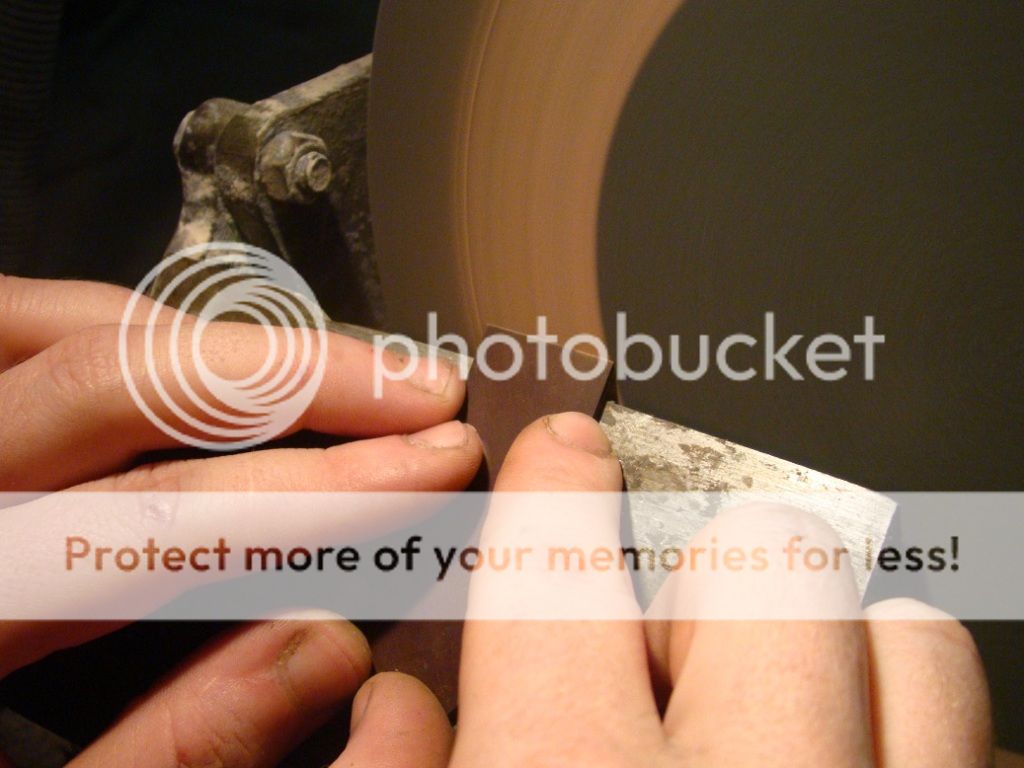

Here are the dovetailed parts; you can see how theyll fit.
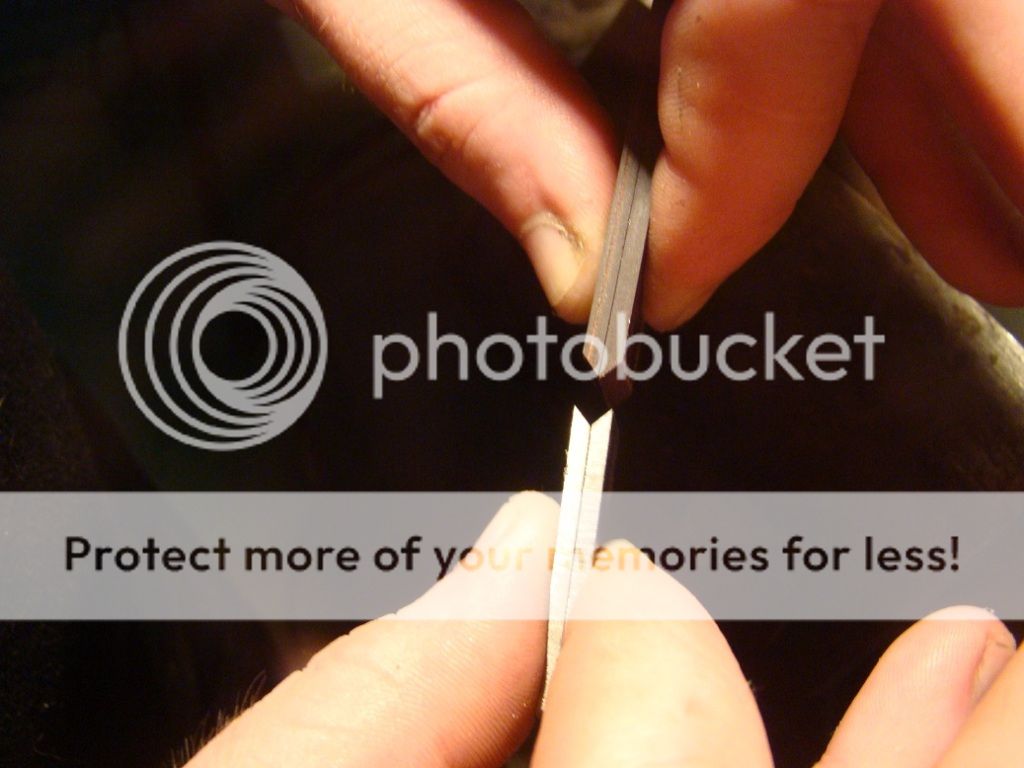