- Joined
- Jan 29, 2014
- Messages
- 1,638
I will have an actual project in the next few days but in the mean time this poorly drawn diagram. This is just how I do the cross wedges, there are other methods that make sense. The next time I do one, I'll photograph it along the way.
crosswedge by city_ofthe_south, on Flickr
What I wanted to illustrate is that the first wedge is the same width as the handle - top left image.
Top right image shows the wedge driven. The green line indicates where I split the wedge with a chisel. The arrows indicate that the first wedge has spread the handle "front to back".
Bottom image shows that the second wedge can be driven as usual.
Another picture of the same concept.
crosswedge2 by city_ofthe_south, on Flickr
First image the black is the eye, the 2 kerfs are cut.
Second image the first wedge is driven the same width as the handle, spreading the eye "front to back", leaving room "left to right" for the handle to spread.
Third image shows a wedge as wide as the eye. You can picture that when the second wedge is driven it will be fighting the first one.
Final image shows both wedges driven, filling up the eye.
So, could you just use 2 small wedges in the 3rd picture to solve the problem? Yep. But to my way of thinking, this is simpler and the result is the same.
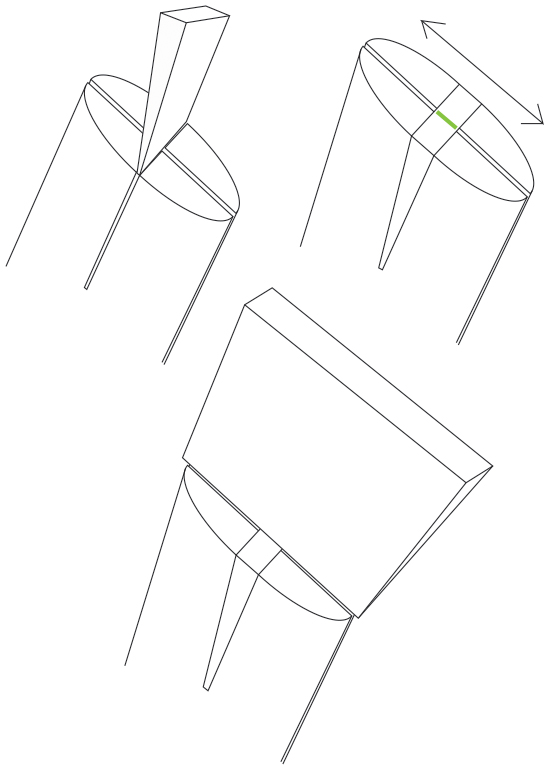
What I wanted to illustrate is that the first wedge is the same width as the handle - top left image.
Top right image shows the wedge driven. The green line indicates where I split the wedge with a chisel. The arrows indicate that the first wedge has spread the handle "front to back".
Bottom image shows that the second wedge can be driven as usual.
Another picture of the same concept.
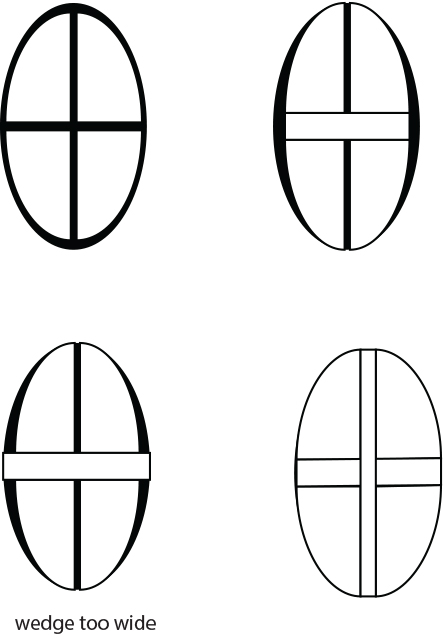
First image the black is the eye, the 2 kerfs are cut.
Second image the first wedge is driven the same width as the handle, spreading the eye "front to back", leaving room "left to right" for the handle to spread.
Third image shows a wedge as wide as the eye. You can picture that when the second wedge is driven it will be fighting the first one.
Final image shows both wedges driven, filling up the eye.
So, could you just use 2 small wedges in the 3rd picture to solve the problem? Yep. But to my way of thinking, this is simpler and the result is the same.
Last edited: