- Joined
- Dec 3, 1999
- Messages
- 9,437
Hi folks- 
I keep having the same issue with my shoulder file guide--- Since I make my knives with a very short ricasso, there isn't much of a flat/parallel area for the file guide to clamp down on. Since the cap screws and guide pins typically end up just past the ricasso, where the distal taper starts... this leaves me clamping down on a wedge. It's a very lightly tapered wedge, but a wedge nonetheless. That makes the file guide come tight with a bit of a crown. I usually put some kind of shim on the thin side... essentially allowing me to clamp down on a uniform thickness. Pics below are from the thread in my signature.
This is obviously an exaggerated sketch, but it shows the issue I'm talking about.
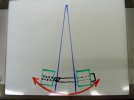
I'd like to NOT have to mess around with the "shim, check.... shim, check.... etc." program.
I've been kicking around ideas on how to eliminate this, but thought I'd throw the topic up here and see if any of you have any thoughts on it.
One idea is a guide with less height and bigger guide pins (3/8) that would be less forgiving, and so the center line of the pins/screws would be on the flat/parallel part of the ricasso.
Another idea is a much bigger guide, with 4 guide pins.
I don't know what the ideal tolerances are on the holes. Obviously the guide pins are typically pressed into, or peined snugly into the fixed side of the guide, and have a sliding fit on the opposite piece, but I'm not sure what exact tolerances should be used to allow that, but not allow any slop or crowning of the guide.
Any thoughts?
These pics show my current solution... Sketch 1- shimming it, pic 2 and 3- eventually getting it clamped down dead flat.

I keep having the same issue with my shoulder file guide--- Since I make my knives with a very short ricasso, there isn't much of a flat/parallel area for the file guide to clamp down on. Since the cap screws and guide pins typically end up just past the ricasso, where the distal taper starts... this leaves me clamping down on a wedge. It's a very lightly tapered wedge, but a wedge nonetheless. That makes the file guide come tight with a bit of a crown. I usually put some kind of shim on the thin side... essentially allowing me to clamp down on a uniform thickness. Pics below are from the thread in my signature.
This is obviously an exaggerated sketch, but it shows the issue I'm talking about.
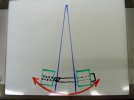
I'd like to NOT have to mess around with the "shim, check.... shim, check.... etc." program.
I've been kicking around ideas on how to eliminate this, but thought I'd throw the topic up here and see if any of you have any thoughts on it.
One idea is a guide with less height and bigger guide pins (3/8) that would be less forgiving, and so the center line of the pins/screws would be on the flat/parallel part of the ricasso.
Another idea is a much bigger guide, with 4 guide pins.
I don't know what the ideal tolerances are on the holes. Obviously the guide pins are typically pressed into, or peined snugly into the fixed side of the guide, and have a sliding fit on the opposite piece, but I'm not sure what exact tolerances should be used to allow that, but not allow any slop or crowning of the guide.
Any thoughts?

These pics show my current solution... Sketch 1- shimming it, pic 2 and 3- eventually getting it clamped down dead flat.
Attachments
Last edited: