- Joined
- Apr 14, 2006
- Messages
- 3,816
Well I promised to post what I do so here goes.
Here is the File guide I made up. It is made from A2 hardened glass hard and just stress relieved. Still glass hard a file glides over it effortlessly. I can get it to bite but only a brand new file and only on the sharp edges.
Measure the ricasso.
Select the gage blocks
Put in File guide
More to follow
Here is the File guide I made up. It is made from A2 hardened glass hard and just stress relieved. Still glass hard a file glides over it effortlessly. I can get it to bite but only a brand new file and only on the sharp edges.
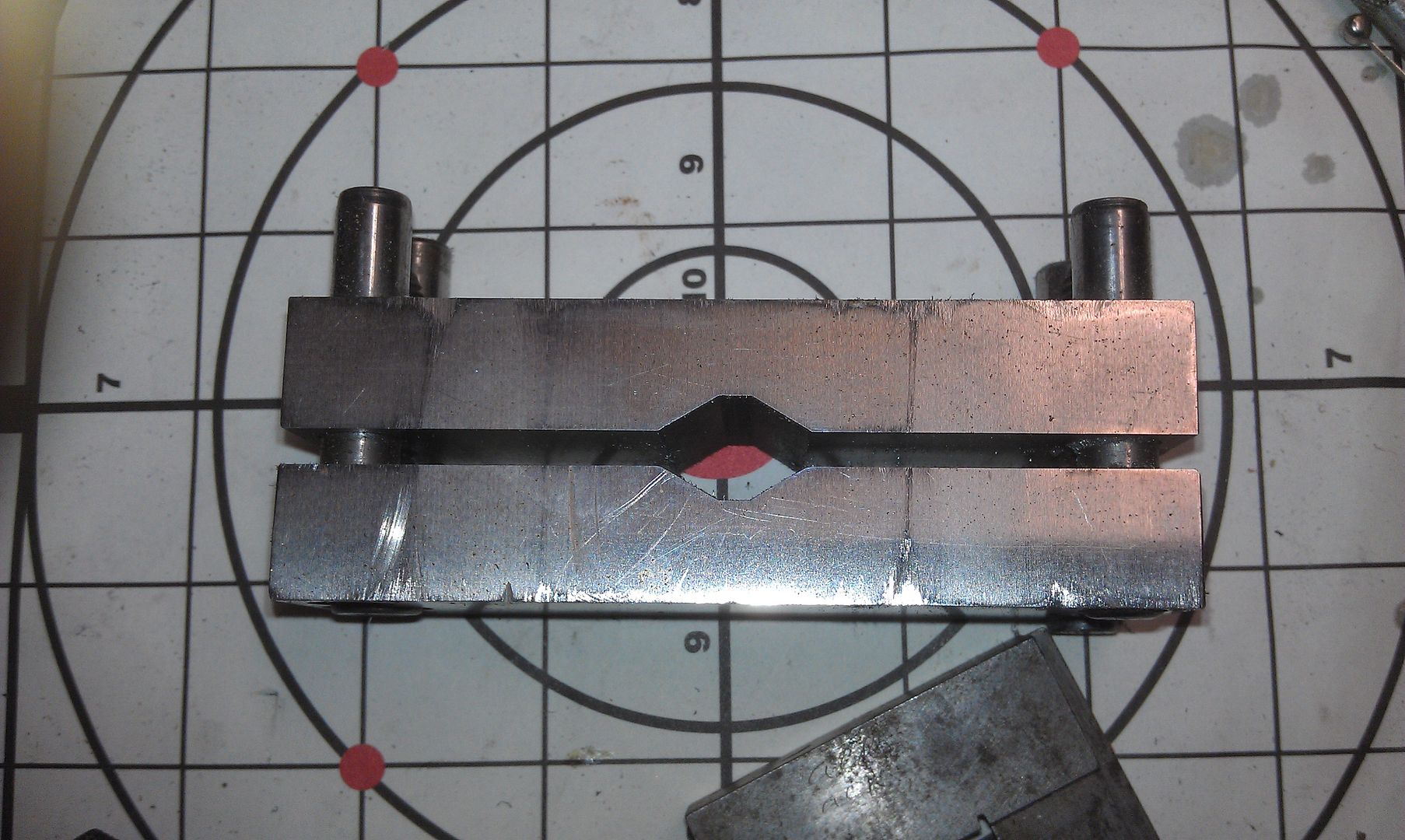
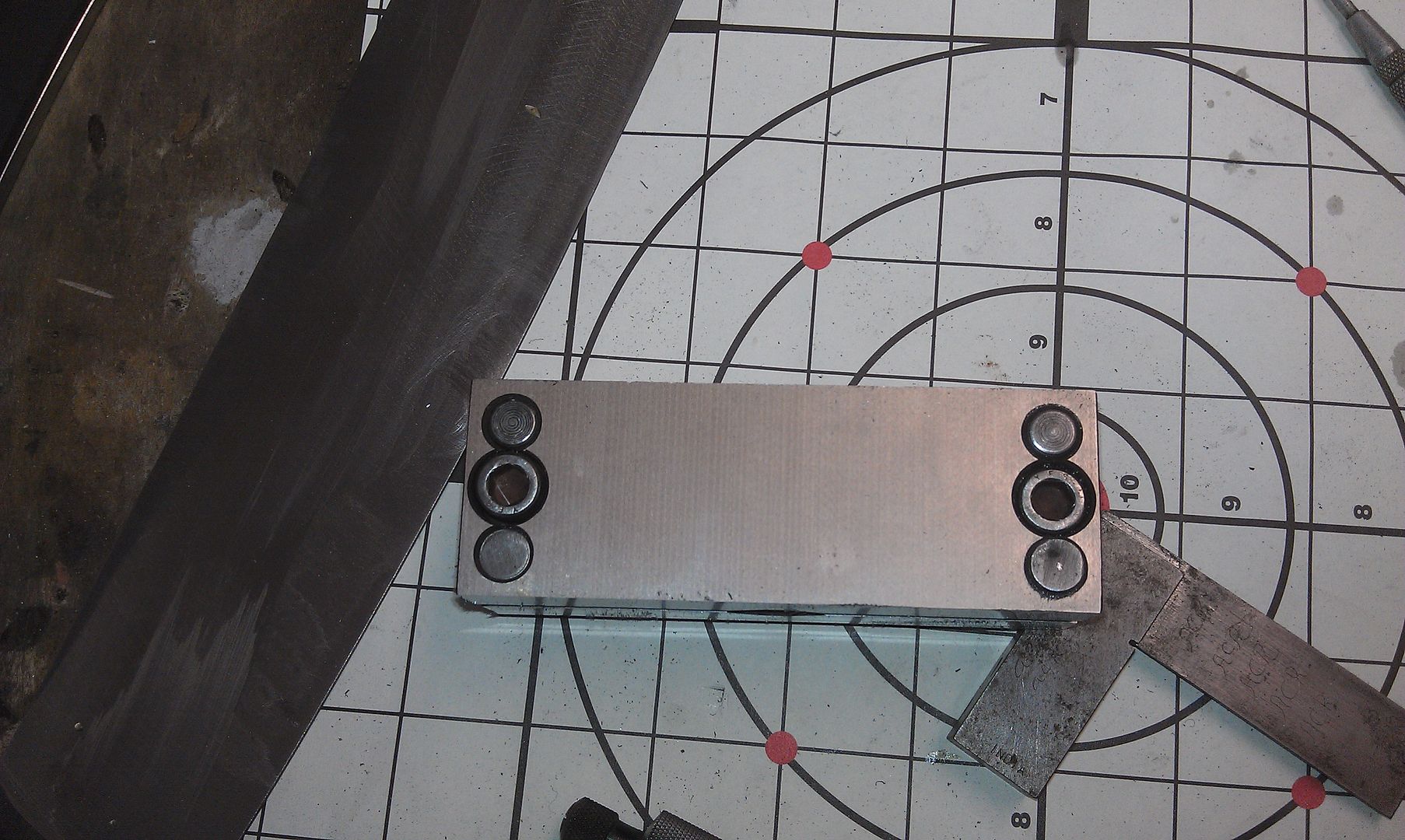
Measure the ricasso.
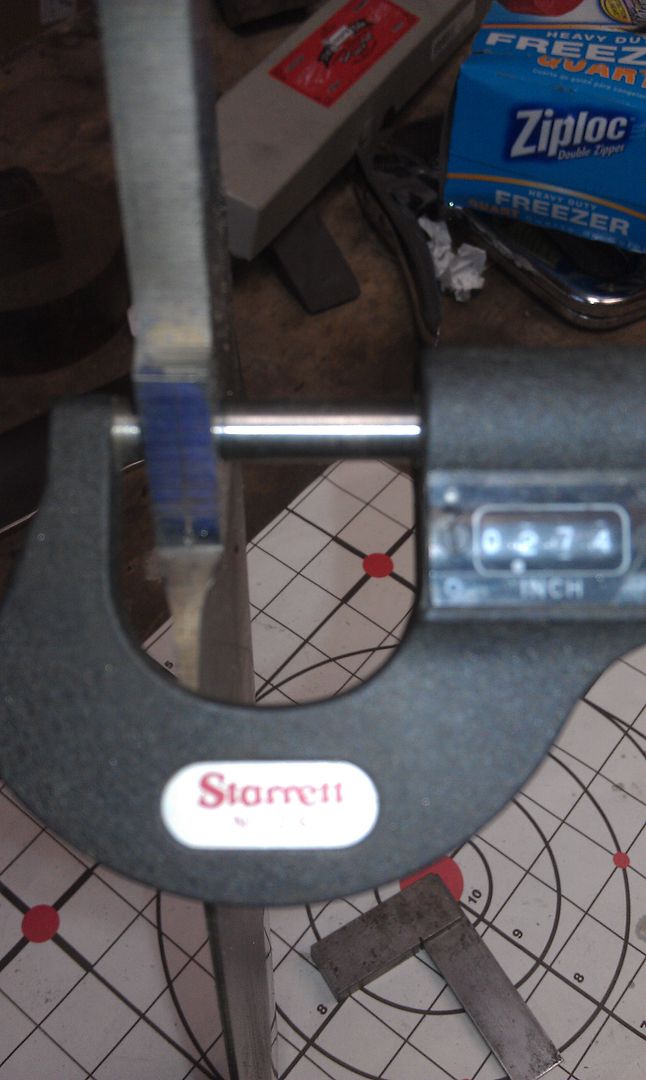
Select the gage blocks
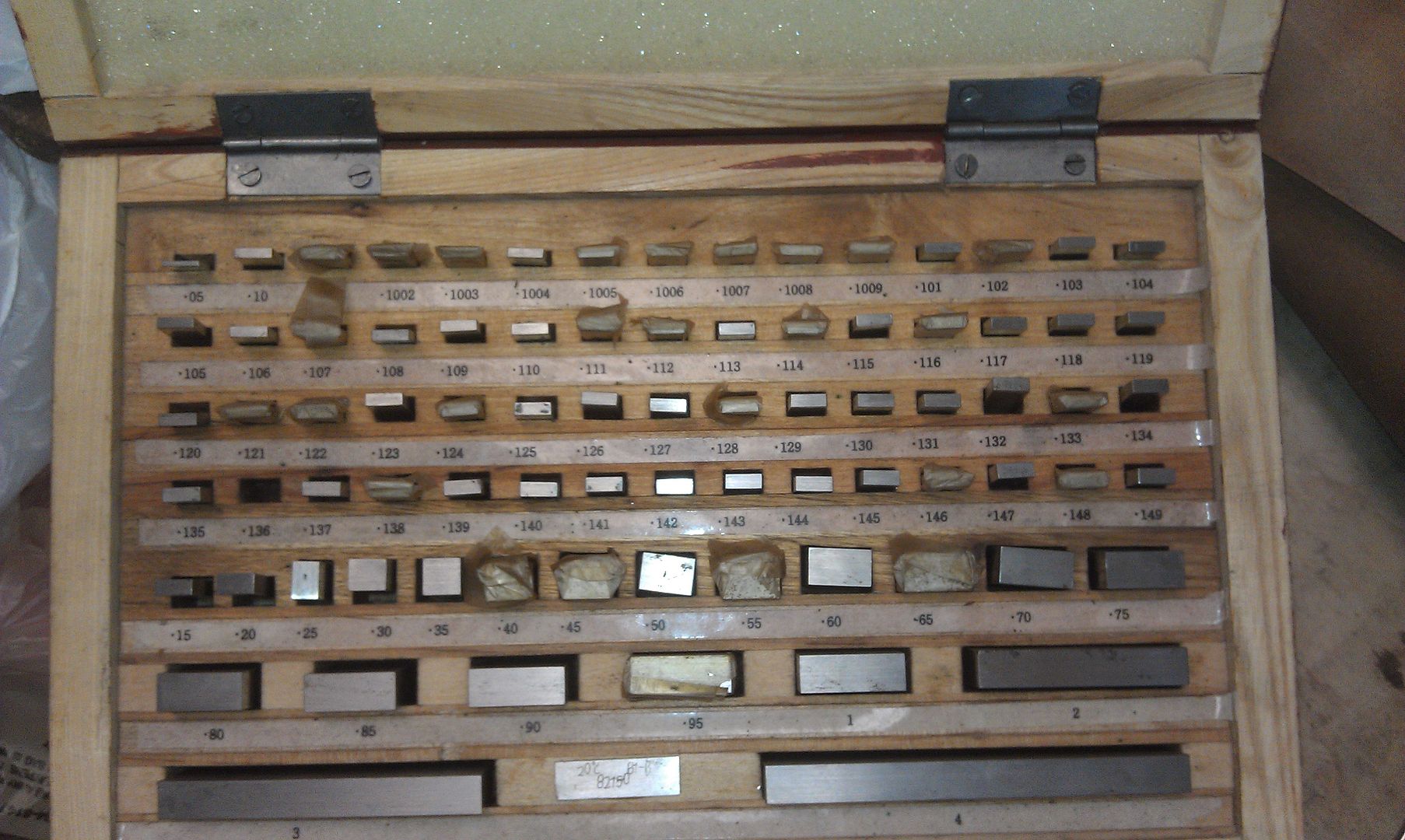
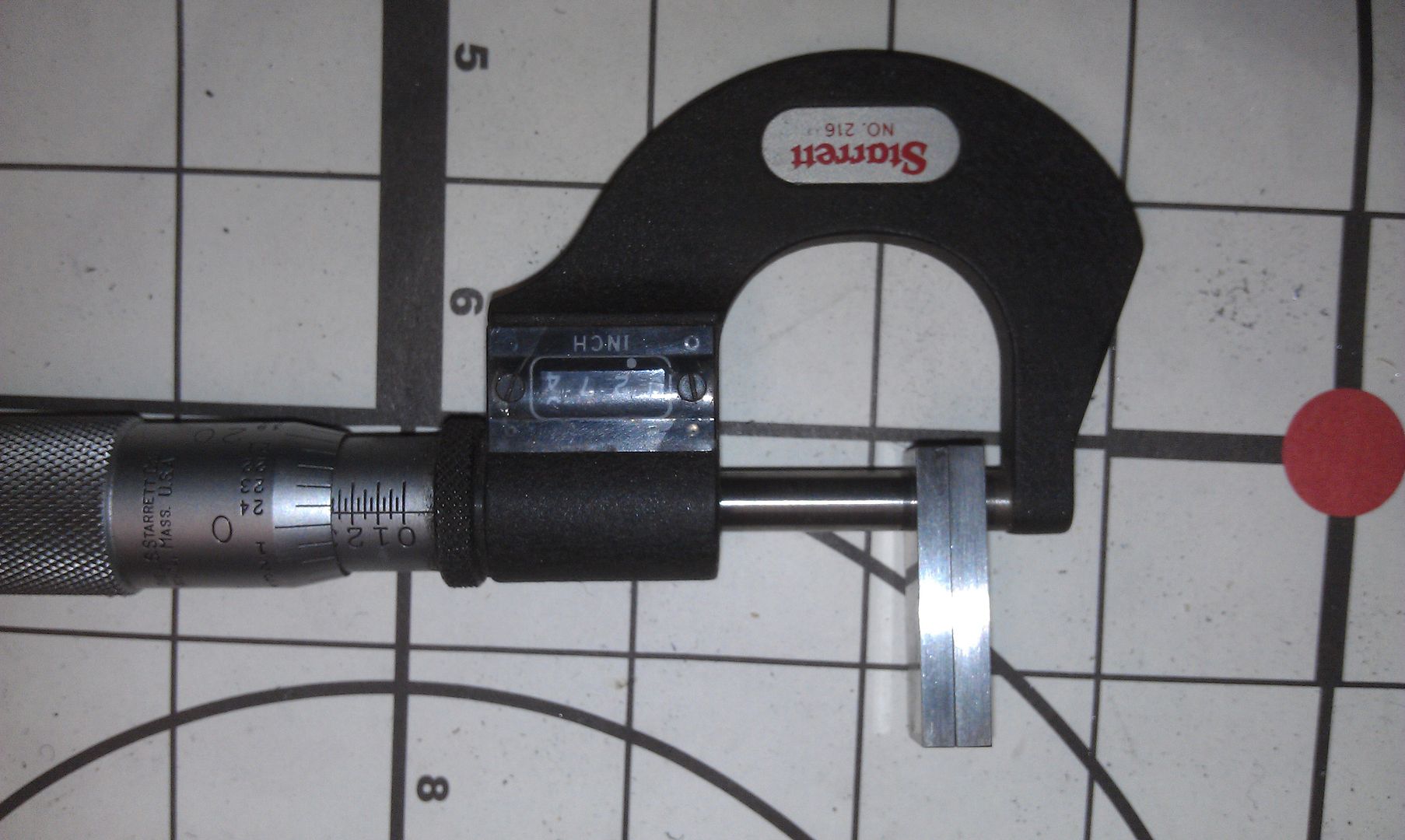
Put in File guide
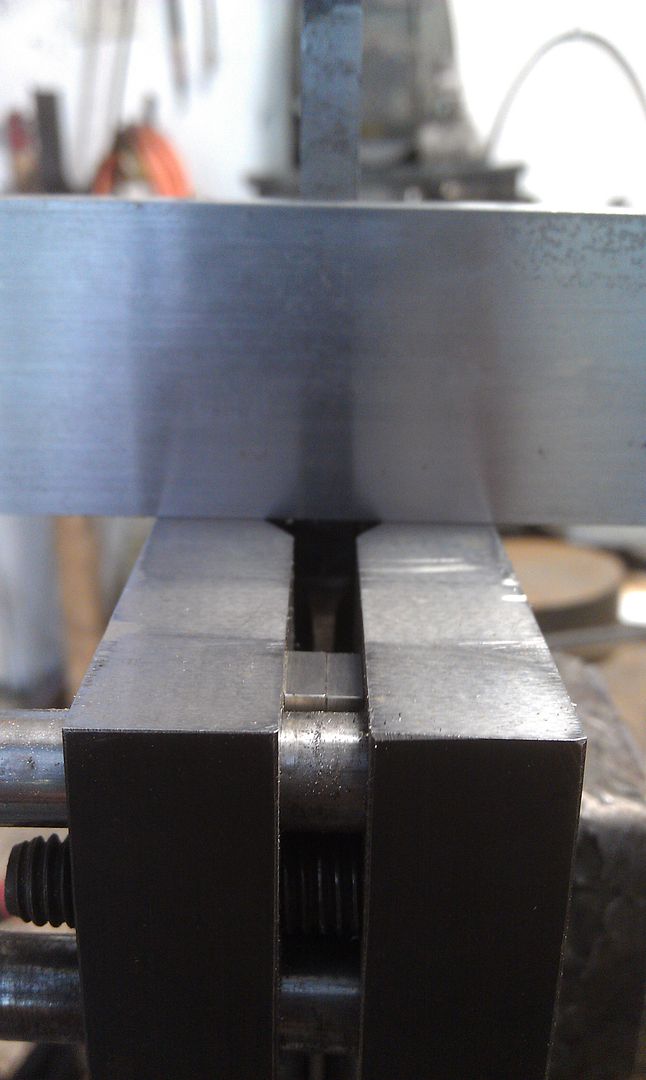
More to follow
Last edited: