This is a very simple job for a knife smith, but this is my first time. So I have to do a lot of thinking and planning.
I bought 4 cheap knives($13ea) that looks to be very robust for a 3” blade and for the weight. The blades come very sharp on all 4, no accident on this. Sharper than my Cold Steel and many of the Steel Will knives. It's the sharpest out of the box out of over 2 dozen of knives of different brands. Also, I compare the hardness of the blade by hitting the spine of two different blade to see the size of the dent. I do NOT believe they will heat treat only the edge of the blade and not the spine. Most likely for small folding knives, they heat treat as one piece(if they even heat treat).
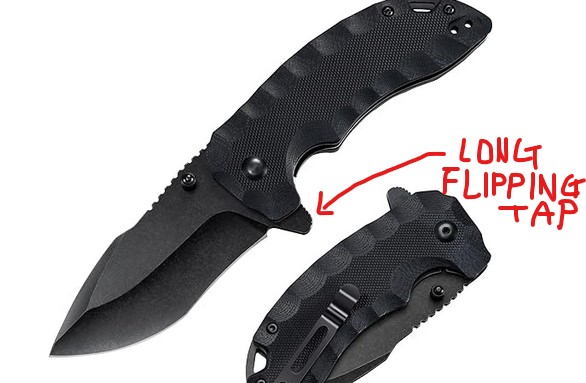
Good thing is even it has ball bearings pivot, they did not thin out the blade or the liner to fit the bearings, so there's no weak point at the pivot. The spine side of the blade is of full thickness to about 3/4" from the tip that make it strong and harder to break when use for prying. Also another thing I like this knife is the flipper tap is very long, it serve as good protection of the hand when thrusting into a hard object. This is the internal picture of the knife.
[/url
]
From the internal picture of the knife, you can see the distance from pivot point to the edge of the liner lock distance is 0.49" as shown, which, is longer distance than a lot of knives particular only 3" blade. This make the liner lock more secure and stronger. I want to change the ball bearings to bronze washer to make the knife tougher.
[url=https://postimages.org/]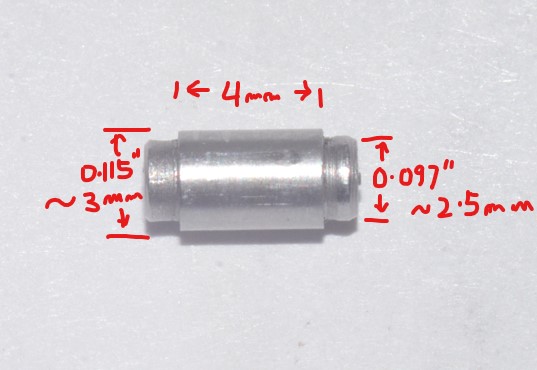
Problem with this knife is the blade stop has diameter 0.1” on both ends to fit into the liner as shown, the middle is 0.116” as shown above. So replacing with bronze washer would make the distance between the liners at the pivot point thinner than the blade stop pin as seen in the picture below, the pivot and blade stop pin is very close(0.6” apart) as shown, this make the distance between the liners uneven and the blade is wobbling sideway no matter what. I have to replace the blade stop pin. I chose a straight pin with 0.116” diameter dowel pin. I have to drill the hole on both liner plates a little bigger to accommodate the new pin.
It's quite an effort to drill. I step increased the drill size to step up to 0.116" in 2 steps to make it easier to drill through each step. IT WORKED. . I can feel the hardness of the liner when I try bending the liner lock out more to give it more a secured lock, together with how hard to drill, I conclude the steel of the liner is very good. Broke a few cobalt drill bits in the process.
The dowel fitted very snug, I use 1 bronze washer on each side of the blade with one at 0.01" and one 0.02". The original ball bearings were 0.03" thick each side. I literally took out 0.03" to make the linings much closer to the blade. The finished knife is smooth in opening, no side way movement of the blade. Everything is tight just like when the knife first came with bearings. It is a success.
I bought 4 cheap knives($13ea) that looks to be very robust for a 3” blade and for the weight. The blades come very sharp on all 4, no accident on this. Sharper than my Cold Steel and many of the Steel Will knives. It's the sharpest out of the box out of over 2 dozen of knives of different brands. Also, I compare the hardness of the blade by hitting the spine of two different blade to see the size of the dent. I do NOT believe they will heat treat only the edge of the blade and not the spine. Most likely for small folding knives, they heat treat as one piece(if they even heat treat).
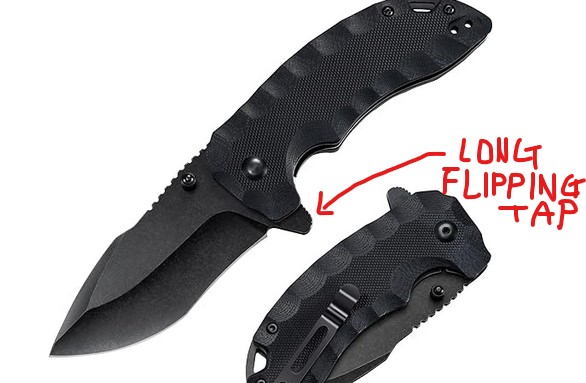
Good thing is even it has ball bearings pivot, they did not thin out the blade or the liner to fit the bearings, so there's no weak point at the pivot. The spine side of the blade is of full thickness to about 3/4" from the tip that make it strong and harder to break when use for prying. Also another thing I like this knife is the flipper tap is very long, it serve as good protection of the hand when thrusting into a hard object. This is the internal picture of the knife.

]
From the internal picture of the knife, you can see the distance from pivot point to the edge of the liner lock distance is 0.49" as shown, which, is longer distance than a lot of knives particular only 3" blade. This make the liner lock more secure and stronger. I want to change the ball bearings to bronze washer to make the knife tougher.
[url=https://postimages.org/]
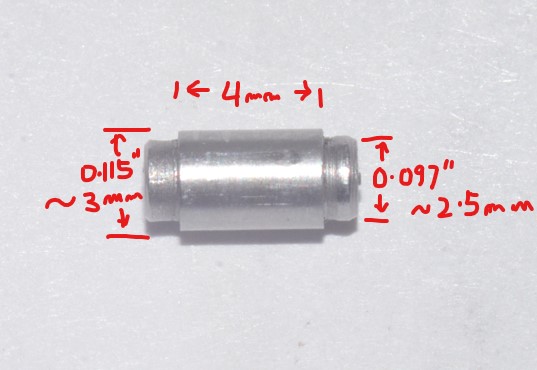
Problem with this knife is the blade stop has diameter 0.1” on both ends to fit into the liner as shown, the middle is 0.116” as shown above. So replacing with bronze washer would make the distance between the liners at the pivot point thinner than the blade stop pin as seen in the picture below, the pivot and blade stop pin is very close(0.6” apart) as shown, this make the distance between the liners uneven and the blade is wobbling sideway no matter what. I have to replace the blade stop pin. I chose a straight pin with 0.116” diameter dowel pin. I have to drill the hole on both liner plates a little bigger to accommodate the new pin.
It's quite an effort to drill. I step increased the drill size to step up to 0.116" in 2 steps to make it easier to drill through each step. IT WORKED. . I can feel the hardness of the liner when I try bending the liner lock out more to give it more a secured lock, together with how hard to drill, I conclude the steel of the liner is very good. Broke a few cobalt drill bits in the process.
The dowel fitted very snug, I use 1 bronze washer on each side of the blade with one at 0.01" and one 0.02". The original ball bearings were 0.03" thick each side. I literally took out 0.03" to make the linings much closer to the blade. The finished knife is smooth in opening, no side way movement of the blade. Everything is tight just like when the knife first came with bearings. It is a success.