Square_peg
Gold Member
- Joined
- Feb 1, 2012
- Messages
- 13,823
Here I will put forth a supposition on the origin of phantom bevels. I've been toying with this idea for a few years. The idea is that old axes with worn heels and toes were taken to the blacksmith who pushed material from the cheeks out to the heel and toe giving the axe a new life.
While I lack certain proof of this origin I'm certain in my own mind that phantom bevels evolved in this way. It's such a natural progression that I don't doubt it occurred independently in logging camps across the NE - likely in the 19th century, possibly earlier.
Presume you're working in a mid-19th century logging camp somewhere in the NE. Presume further that your axe was a major expense and that rather than replace it you were likely to take it to the camp blacksmith for repair or re-steeling. Most large camps had a blacksmith on site to keep tools and rigging in good repair. Consider that these old axes would have been made with wrought iron bodies. Wrought iron moves much more easily under the smith's hammer than modern steel does. A smith might, rather than adding steel, choose to move some material from the fat cheeks of that old axe up to the heel and toe. In the process the cheeks would become thinned at the top and bottom (the areas that would most readily move to the heel or toe).
Loggers would have found these repaired axes to penetrate deeper and release easier while still 'popping the chip' with their high centerlines. Others would ask for their axes to be repaired in the same way. Suppliers, who aren't selling as many axes because these loggers prefer their repaired axes, would decide to copy the new style. And voilà, phantom beveled axes are being produced.
As I said, I have no proof of this occurring but I can present the evidence which lead me to this theory. Have a look at this old felling axe from the Northeast.
It's heavily worn but still has very thick cheeks - lots of material there to work with. By hammering bevels into the top of bottom of those fat cheeks a smith could give new life to that axe. Here's an example of an axe that has forged been in this manner.
It's been hammered so thin that the top (most wear occurs at the toe) is thinned almost to a knife edge.
It's so thin it has warped! Several times I almost ground that thin bent edge off before I realized its importance! Glad I never did that.
Now have a look at a few worn old axes. Can you see that these old thick-cheeked axes could easily be repaired by the method I've described?
What do you guys think, especially those of you with some blacksmithing experience? I'm convinced this is how bevels began. Perhaps old logging camp journals will one day confirm this.
While I lack certain proof of this origin I'm certain in my own mind that phantom bevels evolved in this way. It's such a natural progression that I don't doubt it occurred independently in logging camps across the NE - likely in the 19th century, possibly earlier.
Presume you're working in a mid-19th century logging camp somewhere in the NE. Presume further that your axe was a major expense and that rather than replace it you were likely to take it to the camp blacksmith for repair or re-steeling. Most large camps had a blacksmith on site to keep tools and rigging in good repair. Consider that these old axes would have been made with wrought iron bodies. Wrought iron moves much more easily under the smith's hammer than modern steel does. A smith might, rather than adding steel, choose to move some material from the fat cheeks of that old axe up to the heel and toe. In the process the cheeks would become thinned at the top and bottom (the areas that would most readily move to the heel or toe).
Loggers would have found these repaired axes to penetrate deeper and release easier while still 'popping the chip' with their high centerlines. Others would ask for their axes to be repaired in the same way. Suppliers, who aren't selling as many axes because these loggers prefer their repaired axes, would decide to copy the new style. And voilà, phantom beveled axes are being produced.
As I said, I have no proof of this occurring but I can present the evidence which lead me to this theory. Have a look at this old felling axe from the Northeast.
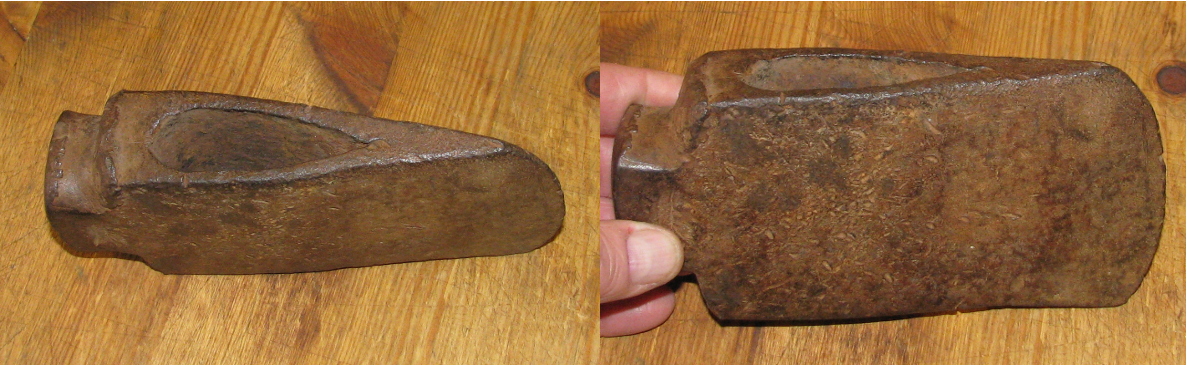
It's heavily worn but still has very thick cheeks - lots of material there to work with. By hammering bevels into the top of bottom of those fat cheeks a smith could give new life to that axe. Here's an example of an axe that has forged been in this manner.
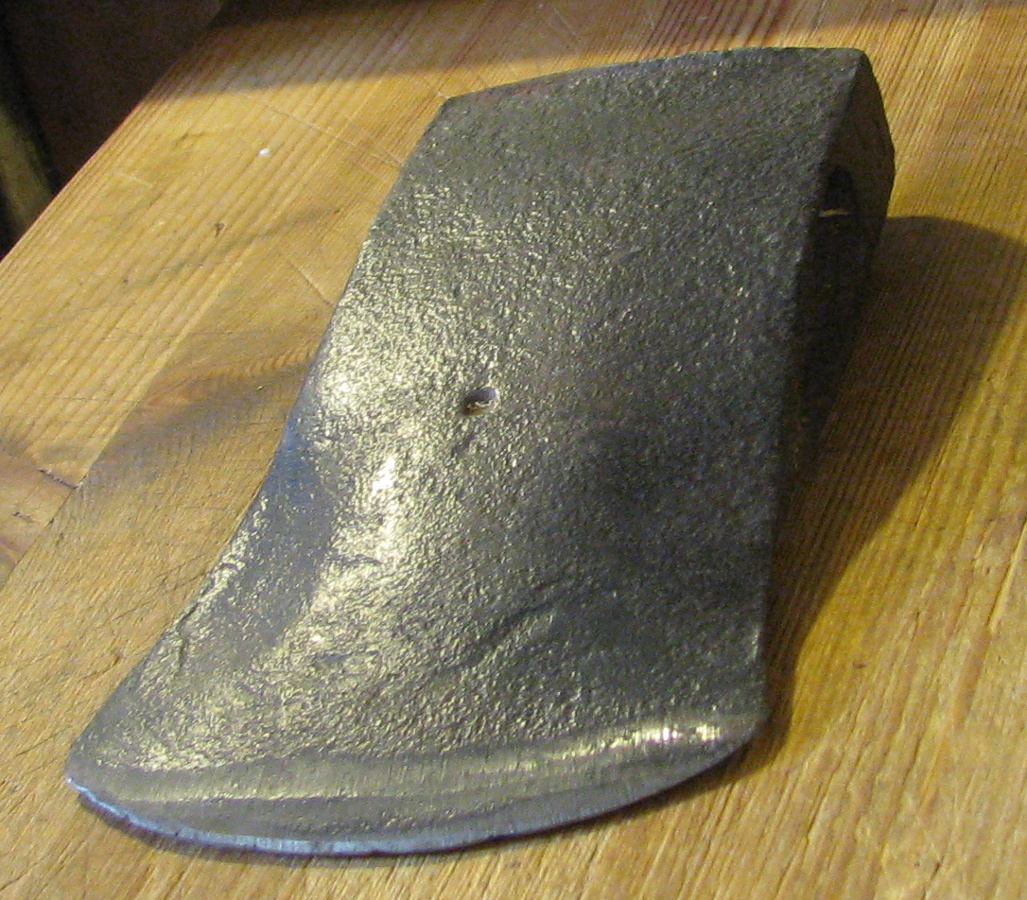
It's been hammered so thin that the top (most wear occurs at the toe) is thinned almost to a knife edge.

It's so thin it has warped! Several times I almost ground that thin bent edge off before I realized its importance! Glad I never did that.
Now have a look at a few worn old axes. Can you see that these old thick-cheeked axes could easily be repaired by the method I've described?

What do you guys think, especially those of you with some blacksmithing experience? I'm convinced this is how bevels began. Perhaps old logging camp journals will one day confirm this.