Nothing very interesting to report for yesterday.I'll run through it quick-like in case someone may use any of the info in their own thinking/planning.
Starting stock,10" of 2" wide strap,1/2",A36.
The end that'll form the blade is pre-bent,exactly 2" of it.
(Again,the idea here is to come up with a set of data that can later be modified;so to make it easier to remember and extrapolate later keeping numbers to even,round ones).
The reason for that bend is that the thinner and taller any material is the harder it is to bend in that dimension.
Since the Attitude,the angle of an axe blade to the eye/poll is critical,that angle needs to happen at the stage as early as possible,as the stock is closest to the sq.section now,and will only get further away from it into more tall and flat.
So the blade, pre-bent, straightens by peining to form the top of the axe.In reality it possibly need to be bent even more,for it to become straight only at the very end of process,but i'm not smart/skilled enough to anticipate things that far...
The other end of pre-form treated equally to keep things symmetrical.
A quick note:One side of each of these halves of future blade will of course be welded.That side needs to be as Flat as possible.So this time around i remember to work with that side Down to the flat and polished anvil-face.
If i was better at the trade i'd also work Cleaner,i.e. i'd brush crap and scale off that side before it goes down on the anvil(or brush the anvil with water to explode it off with steam).
It'd actually make a difference later in welding.
Anyway,the pre-form has central symmetry,and center is marked.That mark is used for further layout.Here the parts comprising the poll are laid off from that mark each way,1 1/2" from center,with soapstone and punch-marks as well:
Each of those marks is fullered to delineate what will be the back of the eye.
The mass between that fuller and the blade is peined across the length of stock to displace mass in order to make room for the eye.
That displaced mass is what makes the lugs.Obviously,for a conventional,hour-glass eye the mass needs to be displaced equally top and bottom.
What happens to the top lug in later American axes is a mystery.According to my archaeologist friend it was commonly trimmed,chiseled off.
If that mass was left in place however,or displaced less than bottom,the resulting axe would either have a radically Open configuration(think GB "Swedish carving axe"),or have an eye that'd have the section of an inverse cone,like Kirves et c.
Here we're dealing with axes that are a Transition between the two cultural styles of hafting,and from what i can see so far they varied between these two systems...
Anyway,the peining out of eye-cavity :
The forging here as well needs to be done with the inside of eye down to the anvil-face,for better hafting the eye needs to be maximally smooth.
If you look close at that last photo you'll see how my forging wonders off the original fuller towards top of photo.That is bad and wrong,and i can blame it on the ruined edges of my poor old anvil,but in reality it means that i've overworked my time at this task,and must quit before i screw things up further.
Errant blows are NOT acceptable.With proper mensuration,one can maintain equal amounts of mass that go into each half of a symmetrical(hopefully)tool.However,how this mass is Distributed is a different issue,and is up to one's skill and common sense.
(i was taught by my old man to use an axe when i was 5,and the first lesson was that the moment you're too tired to hit Exactly where intended-you take a break Right there).
So i must switch tasks,of which there's an endless multitude anyway...

...
I wanted to show you guys a picture of my old LG...Normally it is covered with a really ugly guard,as that coil-spring front and center is directly in front of your face when in use.
(the owner of this hammer but last from previous ended up loosing an eye,and a part of his face,et c.,and the next guy to own it built the guard(i did have a spring shrapnelise on me couple years back,and really need to re-order one...).This note is particularly for folks that like to moan about OSHA laws...This is what it was like before OSHA...).
So yes,it warmed up enough to use the hammer yesterday,just above zero...Throttle still wild,but thankfully worked good enough for me to bang a fat chunk of leaf-spring into required 1/4" or so...Would've been a real bear by hand...
Alas,till i can get some 10xx edge steel we're back to 5160 for now(this spring is old enough to where i'm Reasonably sure that's what it is)....In a week or a bit more,hopefully,that steel should be here.
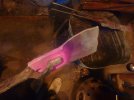