Ok,gents,it's been a while Again...

...This time besides my regular excuses i'm also sicker'n a dawg...
I need to finish one of these axes for my friend,and having offered him the choice,being a very old experienced hand he chose that latest one...Good enough for me,i think it's decent enough forging,and i'd like to see it become a tool and get some feedback from him.
(in any case my head is wedged way too firmly right now to undertake the next attempt).
I scrubbed the forging down in a preliminary manner.Here's about what it looked like then:
And top;then bottom views:
So then back to the hot-work.First order of business is to straighten and align the blade with the other parts.I find it very challenging.My drifts are all short;the axe itself is ill-suited for sighting down it's own lines....This time i experiment with a busted old handle that i shaped roughly to fit the eye.I jab it in in spite of forging being hot,and cough and hack and squint through the smoke trying to gauge the alignment.
When done with that whole circus,it's time to normalize the hardenable parts of that head.
I do three Normalization cycles,at descending heat,allowing it to cool to black in still air each time.
What it's handy for(other than the main purpose-to reduce the grain-size)is as a practice run at heating this particular forging.Also time to collect oneself mentally,to go through the following stages,so as not to forget something when one'll need to move fast,at quench-time.
Here it is slowly cooling from one of n. cycles:
So since i've just heated this thing three times in identical fashion,by now i know pretty well just how and where to place it in the fire.
In this next photo you can see the blade facing you in the fire;the concentric "hot-spot" of my firepot is centered about the eye area.I can see the heat penetrate the forging,and can adjust things so that the heat penetrates the blade evenly,and at the rate that i like.
The clinker breaker-ball at the bottom of my pot is so old and burned,and leaks so much air,that i hardly need to add any with the blower,i barely spin that handle,it's all happening very slow and meditative-like(hectic mode is not great for HT).
I'll run sufficient heat right up to that edge,and hold it there for a minute and a half by the clock.
The butt-plate is on the other side of hot-spot,and again,in my norm.trials i know that it'll be to heat as well.
Then into my bucket of filthiest waste oil west and north of the Rockies...I have a handy hanger bent out of 9-wire that i insert into the axe-head at the last moment,and which hangs on the wire stretched across the bucket,with forging suspended in oil.
(I pre-heat the oil to about 200F,and i'm not a proponent of agitating things in the quench).
The wire hanger allows me to step outside,and not stand there holding the tongs as i'm trying not to breathe the smoke coming off that oil(instead i go outside and smoke tobacco...not sure which is the fouler of the two actually).
But the main reason is that i can slam that lid on if oil starts burning and won't quit,as it does sometimes.If it happens sooner,and gets bad,it can cause me to have to re-do the entire sequence,a pain in the neck,that.
Out of the oil,wiped,and quickly scrubbed to shiny where i need to see oxide colors,it goes into my fancy toaster oven.It's a lovely Black&DEcker one i got out of a local dumpster...one of the legs was broken...I was extremely happy to've found this,have been without electric tempering means for a few years,and tempering a double-ended forging such as this,where the blade and butt-plate both need tempering,is a goat-rope with charcoal and/or torch...
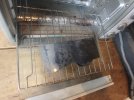