- Joined
- Dec 10, 2006
- Messages
- 5,955
..........................
Again, NOT ABRASIVE USE of those steels, tests showing strength and impact resistance that S110V and others might perform just as well in, except that the high-wear steels would be painful to grind to such fashion and those aren't high-wear uses, so why bother? Did the CPM-3V and AEB-L experience no edge damage? I see damage, i.e. fine edge gone. Now show me the damage on S110V. Make me a believer.
Though I have enjoyed our back and forth this will be my last post in this regard as I feel I have given enough resources in my posts as I will in this one and truthfully....you have not which I can read and form an opinion on (use to educate myself) and I do not want to 'make you a believer' in anything.
One cannot go on Charpy tests data given in datasheets alone IMO. Why? Because there is a lot of data not given. Here is a post I did:
Unfortunately in most steel data sheets available to us there is no specifications by many manufacturers and one is left with a few questions.
Here is an article about fracture toughness and orientation:
EducationResources, Community College, Materials, Mechanical, Fracture Toughness
Orientation
The fracture toughness of a material commonly varies with grain direction. Therefore, it is customary to specify specimen and crack orientations by an ordered pair of grain direction symbols. The first letter designates the grain direction normal to the crack plane. The second letter designates the grain direction parallel to the fracture plane. For flat sections of various products, e.g., plate, extrusions, forgings, etc., in which the three grain directions are designated (L) longitudinal, (T) transverse, and (S) short transverse, the six principal fracture path directions are: L-T, L-S, T-L, T-S, S-L and S-T.
From the book:
Metallurgy of Steel for Bladesmiths & Others who Heat Treat and Forge Steel - By John D. Verhoeven (2005)
On Page 53
"The orientations of two Charpy impact bars are also shown.
Notice that in the transverse bar the elongated inclusions will run parallel to the base of
the V-notch while in the longitudinal bars they will run at right angles to the base of the
V-notch. Brittle failure occurs by cracks being opened up by the triaxial stresses
generated at the base of the V-notch. Now consider the
effects of the elongated inclusions. When the inclusions
lie parallel to the V-notch baseit is possible to have an
inclusion lying along the entire base of the V-notch. But
when the inclusions lie at rightangles to the base of the
V-notch an inclusion will pass the base of the notch at
only one point. Hence, the inclusions will enhance crack
formation much more effectively for the transverse bar
orientations where they lie parallel to the base of the V-
notch. Charpy data on rolled sheet containing
elongated sulfide inclusions give impact energies of
around 44 ft-lbs for longitudinal bars and only 15 ftlbs for transverse bars. The data provide dramatic
evidence illustrating how elongated inclusions
reduce the transverse toughness of wrought steels."
Another that seems to discuss orientation:
Suranaree University of Technology
• Longitudinal (B)
shows the
best energy absorption because
the crack propagation is across
the fibre alignment.
• Transverse (C)
gives the worst
energy absorption because the
crack propagates parallel to the
rolling direction
END.
It is also important to remember that one cannot just compare different steel categories to each other. Even similar steel categories such as in the Shock-resisting steels can have different values because of the variables I mentioned above and different heat treatment.
Now, as I posted earlier:
Grain size and its affects on strength
http://materion.com/~/media/Files/PD...ial Strength
http://www.escholarship.org/uc/item/88g8n6f8
The same holds true for primary carbides:
"In addition to the main requirements, like high strength and wear re-sistance, tool steels should also possess sufficient toughness to avoid tool failure by cracking or chipping. These failure mechanisms are controlled by the propagation of intrinsic microcracks. The resistance of the mate-rial against growth of an existing crack can be measured conveniently by plane strain fracture toughness tests. Contrary to the bending rupture test,which takes into account both crack initiation and crack growth, plane strain
fracture toughness tests only consider the latter. Crack growth is governed mainly by the content, size and distribution of the primary carbides and the mechanical properties of the matrix. The content of primary carbides is determined by the amount of carbon and carbide forming elements like chromium, molybdenum, vanadium, tungsten and niobium. These elements improve wear resistance and hardness of the material but impair toughness,because of their strong tendency to segregate during solidification." (J. Blaha, C. Krempaszky, E.A. Werner and W. Liebfahrt (2006). CARBIDE DISTRIBUTION EFFECTS IN COLD WORK TOOL STEELS. 6TH INTERNATIONAL TOOLING CONFERENCE. Page 290)
CARBIDE DISTRIBUTION EFFECTS IN COLD WORK TOOL STEELS
Vanadium affects described in patent information:
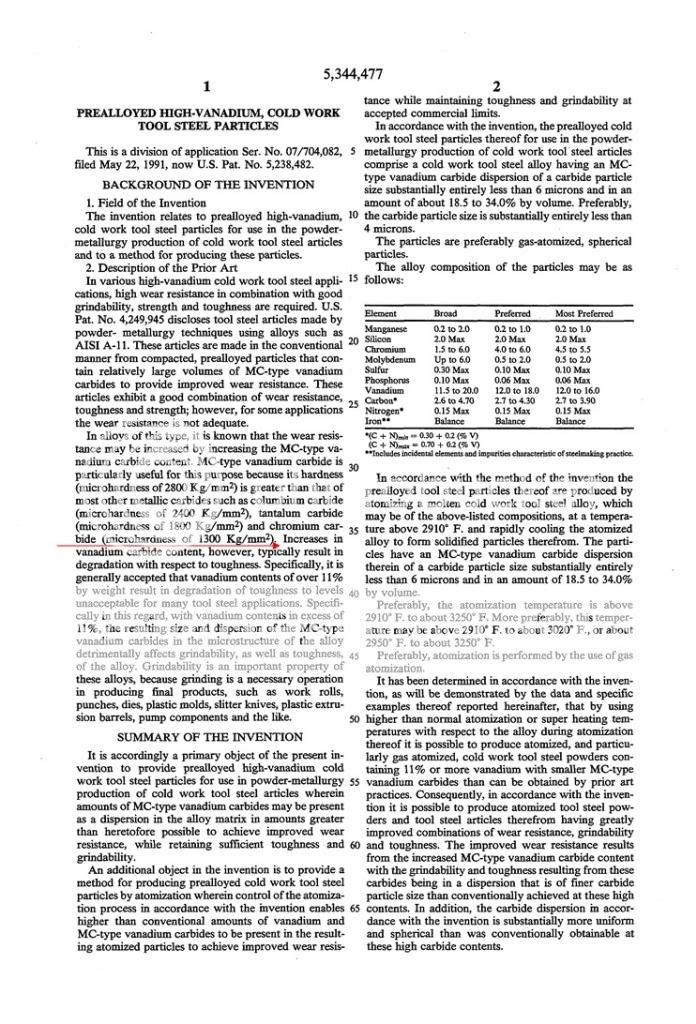
IMO if there is too large primary carbides you wont have the same strength and toughness you can have in a high strength low alloy steel. If what you want is wear resistance then IMO buy a knife with the properties and heat treat for high wear resistance, but from everything I have read my opinion is that you cannot expect a high wear resistant steel to have the same resistance to impact or deformation as lower alloy, fine grained and small carbide steels.
One final note, now without references. In my uses I have not seen any advantage of high wear resistant steels on the farm. Why? Because I cut very dirty material with a lot of sand, debris such as oil, plastic webbing etc in them. The edge is dull no matter the angle or steel. A simple test: Take a glass plate and do a draw cut on it with some significant force (say 15 lbs). It will dull no matter the steel. I am personally happy with steels such as M390, CPM-M4, Nitrobe-77, H-1, 1055, 1095, 12C27, INFI, S30V, S35VN, RWL-34 and the others in my collection. I would rather have my edges role than chip, hence I sharpen them appropriately and use them appropriately, though I have run into some personal face palms. I am in favor of steels with low edge angles and ground thin. I have no issue with other people wanting different properties.