ok - lets try starting with this. Wood is porous - we all know that. But to understand stabilization we need to characterize that in some manner. Most publications appear to want to divide "pore sizes" up in to 4-5 divisions. The Wood Database (hardwoods) uses four divisions:

where "micrometers" is the diameter of the pore in micrometers (microns). What this means is actually somewhat misleading - but I will clarify that in a bit.
Most academic / professional journal articles appear to want to describe the pores with a different range of sizes. for example, an article by Plotze from 2011 ("Porosity and pore size distribution of different wood types as determined by mercury intrusion porosimetry" in the European Journal of Wood and Wood Products. (volume 69 to be more exact) tops out at a smaller diameter and goes much smaller. Several other articles I have seen also report data in this smaller range, so for now lets go with Plotze's definitions:
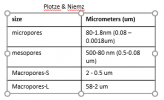
This is NOT meant to be absolute, but rather somewhat representative of the sizes and the range of sizes (of course, this will differ in detail from species to species and even tree to tree. Overall, Plotze's article gives some insightful data from a range of species, varying from Beech to Maple to Ebony).
For current purposes, lets use an "example" pore system that includes these four basic sizes of pores and their terminology (this is VERY simplified, as real pore systems are branched and tortuous - but this should be enough to make clear the basic important points:
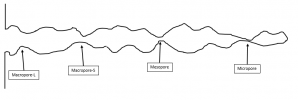
so - to generalize even more, we have some pores that are about 10 microns, some that are about 1 micron, some that are about 0.1 micron, and some that are 0.01 micron in diameter. Now,
and this is a very important point, you will note that I have indicated the "pores" to be the "pinch points" between larger areas (and not the "large" areas between "pinch points"). This is intentional because, as I will talk about later, it is these "pinch points" that control the ability of anything liquid (water, mercury (used in mercury porosimetry), acrylic resin, etc) to pass or "flow" into "deeper" regions of the pore system. The diameter of these "pinch points" also have a direct (i.e. quantitative and mathematical) relationship between the pressure applied to the wood and the ability of that pressure to "push" the resin past that pinch point. But again, I will describe that later.
What is "stabilization"? All of the professional and academic journal literature defines "stabilization" as filling this pore space with some sort of solid substance - so the pores end up looking like this:
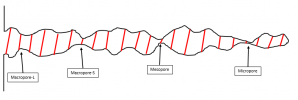
Where the red hashes indicate, in our case, the presence of acrylic resin of some sort in that location of the pore (sorry this is so messy - my powerpoint is not behaving the way it should for some reason). By filling the pore space with a rigid substance the overall block of wood is reinforced by a dense mesh/network that "protects" the wood throughout. That, and I am sure others here on the forum, is an absolute. Treatments that only cover the surface - well, they only stay on the surface. They do not "reinforce" the bulk of the wood block. I will talk later quantitatively about the "whys" of what aspects of a process will allow that deep penetration of the porespace.
I do not mean the above diagram of a "filled" pore to specify that the entire porespace needs to be filled (you can never get there anyway, even with commercial processes). You just need enough of the porespace filled and "reinforced" to create that hard "protective / reinforcing network". You also need to understand that even though the simple "pore example" shown above implies that "big" pores are near the surface, and "small" pores are deeper down,
that is not the case. Both big and small pores exist near the surface just as equally as they do down in the middle of the block. So, even if you just fill the "biggest" pores, you have still created a network of hard resin that permeates the block (again, more later on how you actually do that).
That is the source of my question of "how good is good enough"? If (and this is a big if) all you are after is a structural reinforcement sufficient to withstand the rigors a kitchen counter - maybe you do not have to fill the entire porespace?
Keeping in mind that "bigger pores are easier to get filled than small pores" - below is some select data on pore size distribution from Plotze's paper:
From this you can see that, for Maple for example, the biggest pores make up most of the porespace. By filling them you create a reinforcing resin network that, in addition to creating a web of hard resin throughout the block, also covers most of the porespace available. Somewhere in the middle is Oak, where the two biggest pore space categories make up something like 30% of the porespace. Again, seeing that if you fill those two categories, you will create a web that spans the physical dimensions of the block - is this enough to protect the handle from the rigors of use? In the kitchen, maybe. As a field knife - probably not. But it definitely will not be as "heavy" as if all (or most) of the pore categories were filled. gotta decide which of those "needs" is more important to you (and your customers). WAY on the other end of things is Ebony, were something like 75% of the porespace is made up of the absolute smallest (and hardest to fill) pores. Again, because there is a direct relationship between the higher pressure applied and the ability to "push" resin through those smallest pore "pinch points", this is the reason Ebony is so hard to stabilize. (oh, one other important point: because mercury porosimetry measures the ability of pressure to push liquid past and through a "pinch point" - even if there is a much larger space "behind" that pinch point, that larger space is not
accessible to the fluid, and so it "counts" as if it were all of that smallest pore size. The exact same thing is true when pushing resin into the pores - we are really dealing with "accessibility" of the pores, not directly their actual size. A great example of this is Cork - highly porous with really quite big pores (physically speaking), BUT the pores are "closed", with no connection to the outside world - the pores are not "accessible", and so would react under these processes as if they were extremely small....)
Very quickly, I am going to talk about Acrylic resins. Basically they consist of small molecules that (using heat and an "activator") start to chemically react with each other and form long chains of molecules. These chains of molecules are highly intertwined (as I said before, think highly, highly intertangled strands of thread). When the molecules stop "growing and lengthening", the result is a pretty hard, rigid solid. The stuff goes in as a liquid, and ends up a solid "molded" to the porespace of the wood The details (and differences) of the individual small molecules that are used to start with define the differences in the final "solid" result (more dense, less dense, harder, softer, etc). Some are mixtures of different types of small molecules. I would not sweat the differences between them too much (they are all of the same basic chemical family) - for marketing purposes some companies may scream "trade secret", or "proprietary mixture" ... but that is really mostly marketing. Again, I would not sweat the differences (except as i will talk about below regarding viscosity and surface tension). (one weird thing about Acrylic resins in general though is this: the vast majority of plastics have a specific gravity (density) less than 1.0 (that is, lighter than water). Acrylics as a family have a specific gravity of about 1.2 - which is unusual. Think about it: your plastic food storage containers float in water. Your plastic forks and spoons float in water. But your stabillized wood (filled with a plastic) sinks (mostly). Kinda weird
So .. enough for today I think. But the next obvious question(s) to ask is: what gets in the way of filling that porespace with resin? The answers, as far as I know (some of which many of you have spoken about) are: 1) water, 2) air, 3) particulate, 4) viscosity of the resin, 5) surface tension of the resin, and 6) time. The details about water and surface tension are really rather cool - but then again, I know I am a nerd

.
I will talk quantitatively about each of these in next postings.