- Joined
- Nov 20, 2008
- Messages
- 1,855
Some organic things I've been working on.
A Study In Moose...
A hunter with moose scales.
A little folder I made tonight from a moose tine and a snapped HT 1084 blade.
A moose tine, waiting for another knife.
A couple of beams which I think will be going on a couple of vintage meat cleavers I am waiting for to come in the mail.
Lastly, a rescue, a knife my boss got from an estate, it says "Geneva Tempered Stainless USA" and has a glyph of two guys working on an anvil. It had a 1/8" chip that I ground out so it is kind of a recurve now but it takes and holds a good edge so I thought it worthy of replacing the badly damaged handle.
A Study In Moose...
A hunter with moose scales.
A little folder I made tonight from a moose tine and a snapped HT 1084 blade.
A moose tine, waiting for another knife.
A couple of beams which I think will be going on a couple of vintage meat cleavers I am waiting for to come in the mail.
Lastly, a rescue, a knife my boss got from an estate, it says "Geneva Tempered Stainless USA" and has a glyph of two guys working on an anvil. It had a 1/8" chip that I ground out so it is kind of a recurve now but it takes and holds a good edge so I thought it worthy of replacing the badly damaged handle.
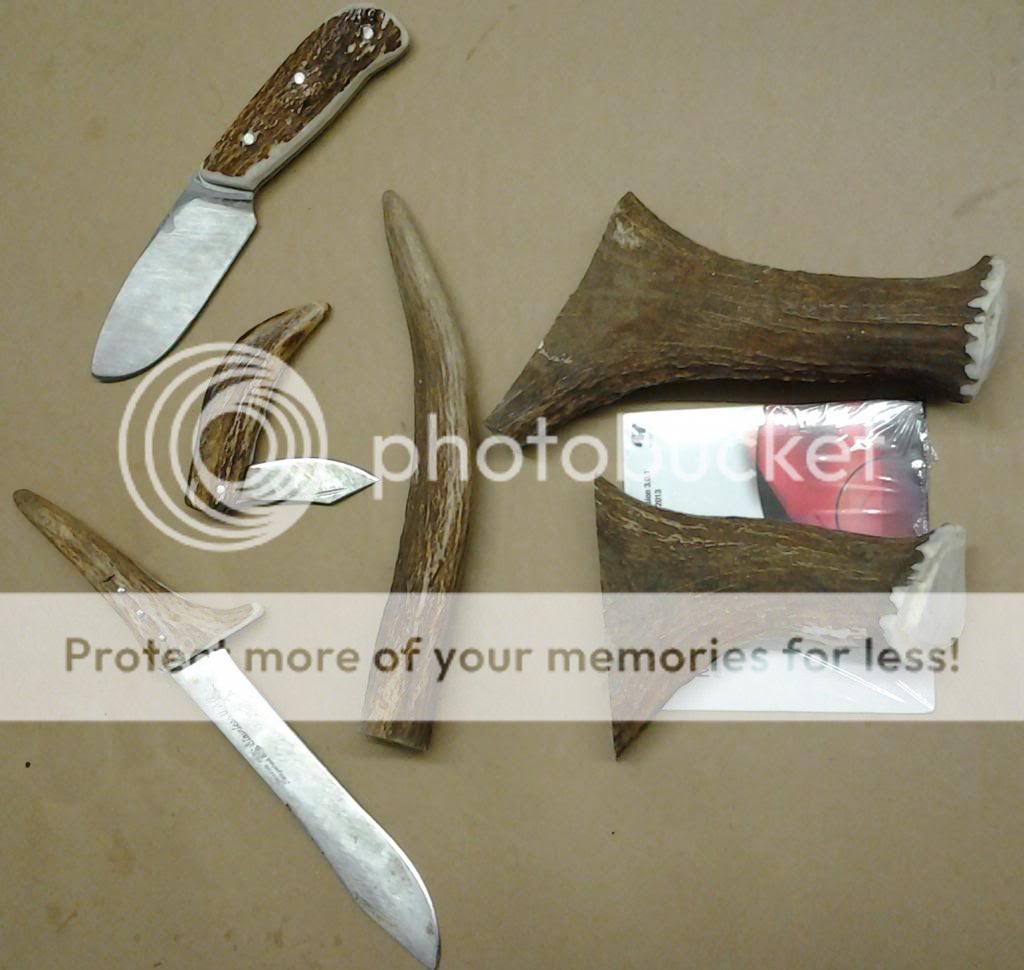