Joshua Fisher
Knifemaker / Craftsman / Service Provider
- Joined
- Mar 27, 2018
- Messages
- 1,508
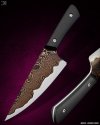
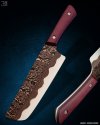
Excited to share photos of this project with Baker Forge in NC. I approached them at the beginning of the year about making some stainless core Copper Mai material and they jumped right on the idea and knocked it out of the park. These are the final samples after several test bars, the first blade is a nitro-v core and the second is aeb-l core. I believe their first production run of these materials will be released next week.