Some of you are already familiar with "the pile" as I call it, of no-longer-fresh grinding belts. The ceramic belts I use cut extremely fast for the first several ounces of stock removal, and the progress on blades is quick. But they slow down to a working level of sharpness before too long. They'll still remove stock, but at a steadily decreasing rate, and as they smooth over, friction increases, and thus heat. The unconventional way I grind allows me to comfortably keep my fingers splayed out over the length of the blade so that I can instantly feel and react appropriately to any degree of heat increase. By the end of the working sharp phase, when belts become a blade burning liability, I either toss them out, or relegate them to jobs like profile hogging, or and handle shaping, where they cannot do any damage. It's at this point they collectively become known as "the pile". Here was the pile at the start of my time in the shop this afternoon/evening:
You can see handle material and steel embedded in them. These ones are at varying degrees of sharpness, but none of them is suitable any more for coarse grinding the geometry, at least not efficiently. The worn scotchbrite belts still work for finishing, but unlike with ceramics, actually take an order of magnitude longer to get a similar result, and require a dip on every pass so as not to cause a mild surface discoloration on the blade bevels. Needless to say, I don't want to be grinding and finishing 30 hawkbill profiles on worn belts when I can get nice results much faster on fresh belts.
So now that the
New River Knife Works
job is the shop priority, the entire pile got moved out of the rotation and replaced with the belts I ordered for it, a handful of 120 grit belts I found stashed at the bottom of a box. These seem to the longest lasting grit for me, which is funny to me because I have learned I can skip the "recommended" step of 60 or 80 grit between my 36 and 120. Which in theory means my 120 grits work the hardest, since after that is 220, and then coarse, medium, fine scotchbrite for a slightly convex belt satin finish. I am sure you can visually see the difference between the fresh belts and the pile even in jusy the photos.
And of course I still have the pile because it comes in handy for all kinds of little jobs, too numerous to try and list. But handles, sheaths, makeshift tools, etc, can all benefit from the pile, which saves the fresh belts for blades. I still have the pile, I just shoved it off to the cluttered side of the garage for now that has some of my stuff but mostly Chris' family's stuff.
The aluminum platen that came with the grinder is not perfectly flat, which can make grinding precision much more challenging. So I removed the paint on the platen, roughed up the surface with a diamond plate, and began using pyrocermaic glass platens a couple years ago.
My platen changes have sometimes been difficult for a variety of reasons, but I am pleased to say that my platen change process went off without a hitch today. You can see the old platen has some chips out of it, most notably along the left edge (bottom in pic). I used to think that the chips were actually problematic to getting a good finish, but they don't give me a problem any more. I can't say exactly what in my grinding technique has changed, but perhaps it's just my general grinding awareness that continues to improve.
I took it off the grinder, turned it upside down, and poured a few drops of acetone into each of the two holes I drilled in the aluminum platen. I wish I had thought to do this from the start, but alas, I did not. I have had platens glue on there so securely that I literally had to grind the little shattered bits off with a diamond plate. That was not fun. But this time (and the last) the plate came off with a quick pry underneath with my indispensable shop tool, the humble putty knife. Which I then used to quickly scrape away most of the glue so I could start again and install this new platen:
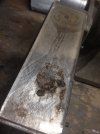