Phillip Patton
Knifemaker / Craftsman / Service Provider
- Joined
- Jul 25, 2005
- Messages
- 5,342
Thanks for all the comments, folks!
I didn't work on it over the weekend, because I got bit by the shop cleaning bug, and that's rare enough that I know not to resist it. ;-)
But today I did regrind it. The hamon looks interesting, and the blade is still straight.

Just like the first grind, I pre-bevel the edges:
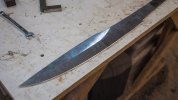
Then I grind down to the edge, checking frequently with a ruler to make sure the grinds are the same on both sides.
The balance point is right at my mark:
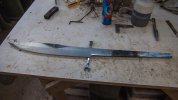
Next, I rounded off the butt end of the tang, using a washer as a template:
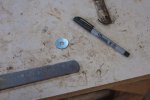
and I also drilled a 3/8" hole:
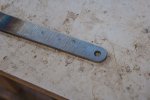
I didn't work on it over the weekend, because I got bit by the shop cleaning bug, and that's rare enough that I know not to resist it. ;-)
But today I did regrind it. The hamon looks interesting, and the blade is still straight.


Just like the first grind, I pre-bevel the edges:
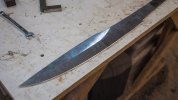
Then I grind down to the edge, checking frequently with a ruler to make sure the grinds are the same on both sides.
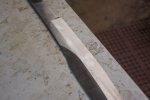
The balance point is right at my mark:
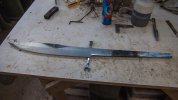
Next, I rounded off the butt end of the tang, using a washer as a template:
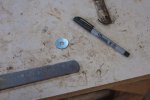
and I also drilled a 3/8" hole:
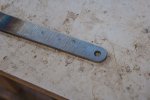