- Joined
- Oct 24, 2013
- Messages
- 906
My spoils of war wrapping up the week... Far from complete, but it's starting too look like something mechanical rather than an inanimate jumble of steel.
Counterclockwise, starting from the top;
gib bar assembly; Tacked and ready to drill out the bolt holes...
beginnings of a quick change die holder for the slide;
Back/Slidesplates; Frame > Slide - 4140 barstock.... Slide > Gib Bar - RailRoad track (sans webbing)... This should work out well in regards to wear. While I could have gotten away with mild steel, I had the stock laying around and thought it fit the bill...
Slide block mount/assembly... almost there...
And finally, a cross-section of what my rear adjustment assembly... Telling and showing are two different monsters. I drew out the I beam in soapstone, and hopefully you guys/gals get the drift... Remember the gib bar is still lacking the adjustment hardware. That's next on the to-do list... Basically its function/purpose is pinching in the back of the slide so it's snug against the frame/backing plate.
Bolt holes that are drilled perpendicular to the web of the beam will intentionally be drill to 1/2" +/- (oversized) to create adjustment slack ; 3/8" Gr. 5 or Gr. 8 bolts...
Bolts that are parallel to the web of the beam will be be drilled and tapped 1/2 Gr. 8... these will adjust the pinch to the back of the slide block, snugging it up...
Here you can also see the 4140/RailRoad track sammiching angle stock... 4140 will ride against the frame while the track will ride against the gib bar...
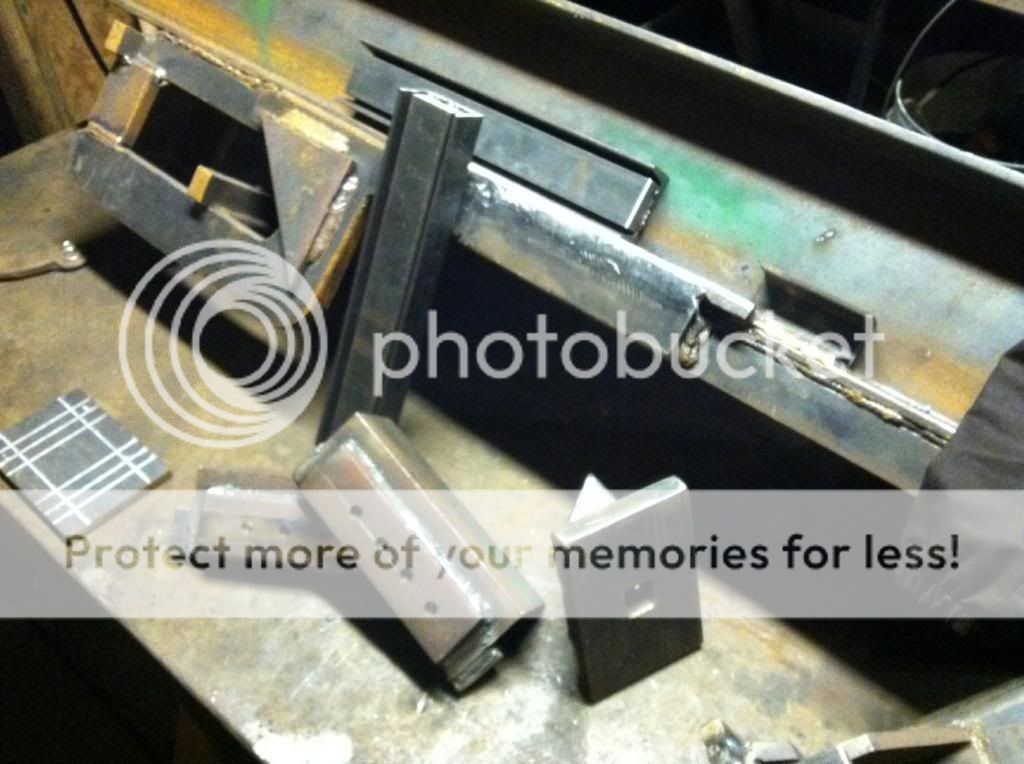
Counterclockwise, starting from the top;
gib bar assembly; Tacked and ready to drill out the bolt holes...
beginnings of a quick change die holder for the slide;
Back/Slidesplates; Frame > Slide - 4140 barstock.... Slide > Gib Bar - RailRoad track (sans webbing)... This should work out well in regards to wear. While I could have gotten away with mild steel, I had the stock laying around and thought it fit the bill...
Slide block mount/assembly... almost there...

And finally, a cross-section of what my rear adjustment assembly... Telling and showing are two different monsters. I drew out the I beam in soapstone, and hopefully you guys/gals get the drift... Remember the gib bar is still lacking the adjustment hardware. That's next on the to-do list... Basically its function/purpose is pinching in the back of the slide so it's snug against the frame/backing plate.

Bolt holes that are drilled perpendicular to the web of the beam will intentionally be drill to 1/2" +/- (oversized) to create adjustment slack ; 3/8" Gr. 5 or Gr. 8 bolts...
Bolts that are parallel to the web of the beam will be be drilled and tapped 1/2 Gr. 8... these will adjust the pinch to the back of the slide block, snugging it up...
Here you can also see the 4140/RailRoad track sammiching angle stock... 4140 will ride against the frame while the track will ride against the gib bar...