- Joined
- Dec 23, 2006
- Messages
- 14,827


This is a project that I am truly excited about
Many of you will remember from one of my Blade Show videos featuring my dear friend David Mirabile where we spoke of a high performance Tanto that he had forged for me.
Go to the 3:30 mark
[video=youtube_share;SCAIH9v6aqM]https://youtu.be/SCAIH9v6aqM[/VIDEO]
To step back a second let us discuss the Japanese Tanto.
Today there seems to be a resurgence in interest in this wonderful genre of blades. I find it funny that most blades that are called Tantos are not Tantos but really Kwaikens, etc
This is not the fault of today's makers. Lynn Thompson of Cold Steel was the first to out right call his small westernized adaptation of a Kwaiken a Tanto and the name just stuck.
Not to knock any makers but it is one of my pet peeves to see these small utility blades referred to as Tanto
__________________________________________________ __________________________
Definition of Tanto;
From WIKi
The tantō is commonly referred to as a knife or dagger. The blade is single or double edged with a length between 15 and 30 cm (612 inches, in Japanese 1 shaku). The tantō was designed primarily as a stabbing weapon, but the edge can be used for slashing as well. Tantō are generally forged in hira-zukuri style (without ridgeline),[1][6] meaning that their sides have no ridge line and are nearly flat, unlike the shinogi-zukuri structure of a katana. Some tantō have particularly thick cross-sections for armor-piercing duty, and are called yoroi toshi. Tantō were mostly carried by samurai, as commoners did not generally wear them. Women sometimes carried a small tantō called a kaiken[7] in their obi primarily for self-defense. Tantō were sometimes worn as the shōtō in place of a wakizashi in a daishō,[8][9] especially on the battlefield. Before the advent of the wakizashi/tantō combination, it was common for a samurai to carry a tachi and a tantō as opposed to a katana and a wakizashi.[8]
It has been noted that the tachi would be paired with a tantō and later the uchigatana would be paired with another shorter uchigatana. With the advent of the katana, the wakizashi eventually was chosen by samurai as the short sword over the tantō. Kanzan Satō in his book The Japanese sword notes that there did not seem to be any particular need for the wakizashi and suggests that the wakizashi may have become more popular than the tantō due to the wakizashi being more suited for indoor fighting. He mentions the custom of leaving the katana at the door of a castle or palace when entering while continuing to wear the wakizashi inside.[10]
__________________________________________________ __________________________
So as you see the Tanto was primarily a weapon that was carried by a Samurai along with his Tachi or Katana and it was eventually superseded by the WAKIZASHI
Now there is a fine line for me between a large battle oriented Tanto and a small WAKIZASHI
Both have a guard
Both can share similar ergonomics etc
For this conversation I will refer to this piece as a Battle Tanto but it also could be referred to as a SMALL WAKI
As a martial artist who at one time was heavily involved with the training of using edged weapons the Tanto and the Wakizashi were indeed my preferred tool
Take a Battle oriented Tanto and compare it with a like sized Bowie knife and I'm speaking of each piece being performance oriented not what most are today. The Tanto will out perform the Bowie in almost all tasks besides the back cut and believe it or not a proper Tanto will even back cut with authority
Add the art of draw cutting to the mix and the Tanto is truly a formidable weapon that has a proven combat lineage that is hard to even come close to by any other combat blade.
Now mind you it has to be set up in the proper sheath configuration (SAYA)
When I see a Tanto in a leather sheath or even Kydex IT FLAT OUT RUINS the whole setup
The Tanto must be worn edge up and to properly do that the sheath(SAYA) must be the correct width and shape to facilitate sash carry and blade orientation
The way the blade fits into the SAYA is also paramount
STeven Garsson speaks of the Importance of the Habaki on Japanese style blades and he is not mistaken
The Habaki is the collar that acts as a wedge that keeps the blade securely in the SAYA
With out the proper fit the whole package becomes dangerous and does not perform and function as it should
Now most modern Tanto makers do not imho put enough into their sheaths. They make a nice blade but they do not seem to understand the true importance of the sheath(SAYA)
This is because most consumers are not actually using these blades as they were Intended to be used
The sheath is an afterthought
The art of draw cutting is what these blades were designed for
You can not draw cut properly with a leather or soft sheath
To draw cut the blade needs to be carried sash style edge up ...... It's that simple
So to bring this conversation full circle
My dear friend David Mirabile is a master artisan and craftsman but more importantly he understands what makes a truly high performance Japanese style blade
David is an Alaskan Blade Smith who has a visceral organic style that truly stands out in a sea of blades
He specializes in incorporating the best of ancient and modern materials to make some truly incredible works of art
He mixes Ivory and Carbon Fiber like no one else in the industry
But more importantly he understands the ergonomics and design aspects of the high performance Japanese style blades like only a few makers out there
His blades are reminiscent of the blades that were carried at the the height of Japan's civil wars the most warring time in one of the greatest blade cultures violent past
He makes functional art that is truly deadly
Awhile back David sent me a Tanto to review and do some test cutting with
This piece was beautiful and featured in this video
[video=youtube_share;ZkjNA_5nMqk]https://youtu.be/ZkjNA_5nMqk[/VIDEO]
Now the beauty of this blade was obvious but what amazed me was the way it performed
It literally cut like a laser and of all the Tantos I have cut with it was one of the top performers only being equaled by a Tanto made by the late great Phill Hartsfield
What was even more amazing was that its beautiful laminated blade showed no wear after blowing thru multiple mats etc
In fact it went off for pro photos to our own Jim Cooper and than on to its new owner one of our fellow forumites Mike
This is the blade that got David and I talking
This blade was exquisite
Adorned with ivory fittings and a spectacular laminated blade it was a bargain at its price which was thousands of dollars but admittedly a rather expensive blade for a Martial Artists hard use blade
So I asked David if he would consider making me a hard use piece that would be priced at a point that would make his incredible work available to martialist looking for a high performance Battle Tanto
Being that he is my brother
Now in a sea of performance blades being made from modern powdered steels etc this blade was not forged from any of the new modern steels it was forged from an axle
Future versions of this will be from W 2
It's all in the heat treat
Quenching this blade
[video=youtube_share;eb9ZCyvf8uQ]http://youtu.be/eb9ZCyvf8uQ[/VIDEO]
So this blade is 15 inches long and exhibits some wonderful Sori (curvature)
Before BoHi (fuller) was carved in
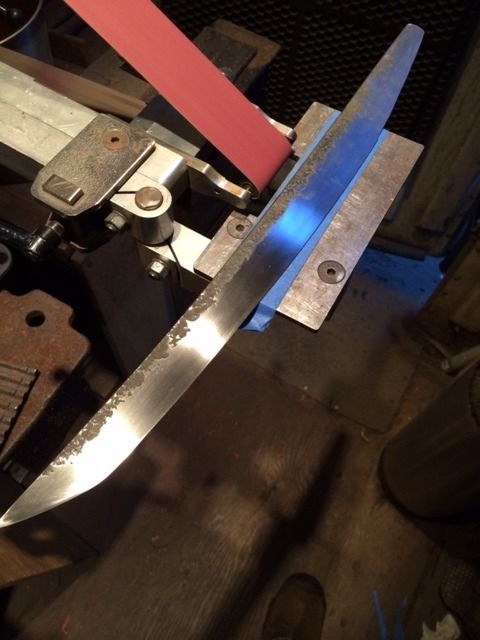
After BoHi (fuller)
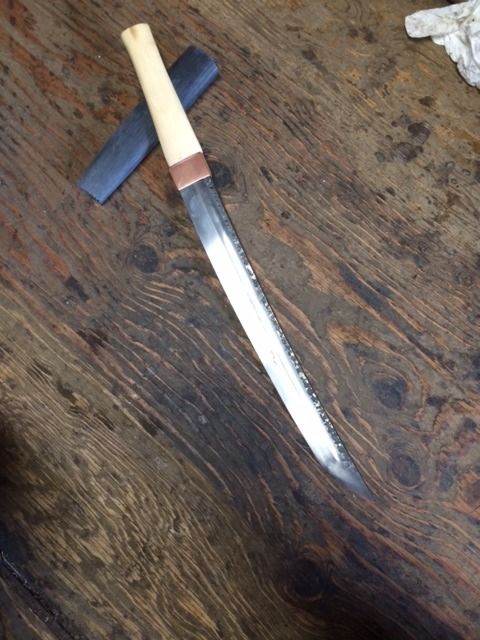
Now a lot of people truly do not understand what a fuller (BoHi) is for and I've even heard some on here refer to it as something cosmetic
A fuller is not a blood groove
It is a way to lighten and adjust balance of a blade
Yes when done well they can look very cool
Weight saving after BoHi

The blade was left with rough forge marks in it to keep cost lower and to emphasize its utilitarian or battle field purpose
The tip is Shobu Zukuri : Which loosely translates to Iris leaf shape. What is most notable is the absense of a yokote (border line between the tip and the cutting edge) and a graceful, curved slicing tip that was used to great effect against the Mongol leather armor during their attempted invasions in the 13th century AD.
This tip style is one of my favorites and makes for a beautiful sweeping tip
Now David would not skimp on his craftsmanship of this piece
Although it has a mono steel blade the SAYA (sheath) will be his classic blend of the best of modern materials blended with classic design. The SAYA will be yellow cedar wrapped in carbon
fiber.
The Koiguchi (mouth of SAYA (scabbard) will be of carbon fiber
The Kojiri (butt of SAYA) carbon fiber
Being that the intent of this blade is a high performance user piece and draw cutting will be heavily emphasized we are going to reenforce the mouth of the SAYA with a band of iron or titanium
The Kurigata will be carbon fiber
The Tsuka (handle) will be yellow cedar wrapped in carbon and than done in a carbon fiber Ito

Wrapped in carbon

The Kashira (butt of handle) will be carbon fiber
The Mekugi will be titanium
The Tsuba (guard) will be iron
The Habaki copper

The Seppa copper
The Tsuka (handle) is a study in function
The traditional Japanese handle is hour glass shaped and that is for a reason
It gives fantastic purchase
For this handle David took it to extremes and shaped the handle in the classic hour glass shape but with some design changes. He left the front fuller to facilitate pivoting and gave it a slightly longer taper to the butt
The flare of the butt will be exaggerated when the Kashira is added

The SAYA is such a critical part of this package and David puts a huge amount of time in it construction emphasizing fit and finish
I have always admired David's attention to detail in this aspect
In a world of makers that do not put near the attention they should in the sheath it is refreshing to see as much attention given in this area as to the rest of the package
Remember this blade is designed to be utilized in draw cutting etc and the SAYA is a detail that can not be ignored
Again no proper Tanto can ride in leather
The SAYA needs to be rigid and be able to withstand thousands of draw cuts and do it is a safe manner
There are many reasons for this project
First and foremost is that I really wanted to get back into the blade arts and I was looking for a high performance battle Tanto
With the resurgence of this style of blade I wanted to let the world see what I consider to be a proper battlefield Tanto
There really is not anything out there at the price point we are targeting
I wanted people to see that are marketing their blades as Tantos what I believe is a true Tanto
I plan on posting pics of this project as David completes it and than I plan on doing a lot or articles and videos on its use.
I would really like to document the design of this piece and how it translates to what I believe will be a truly high performance Battlefield Blade
A lot more to come
As I get back up to speed on my cutting I will video my progress
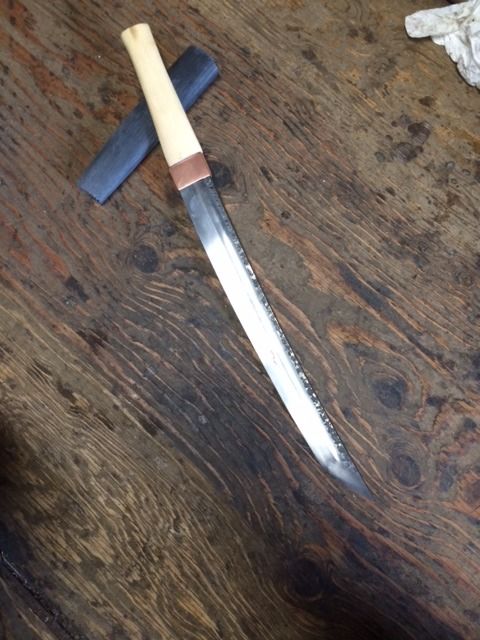

Help with terminology
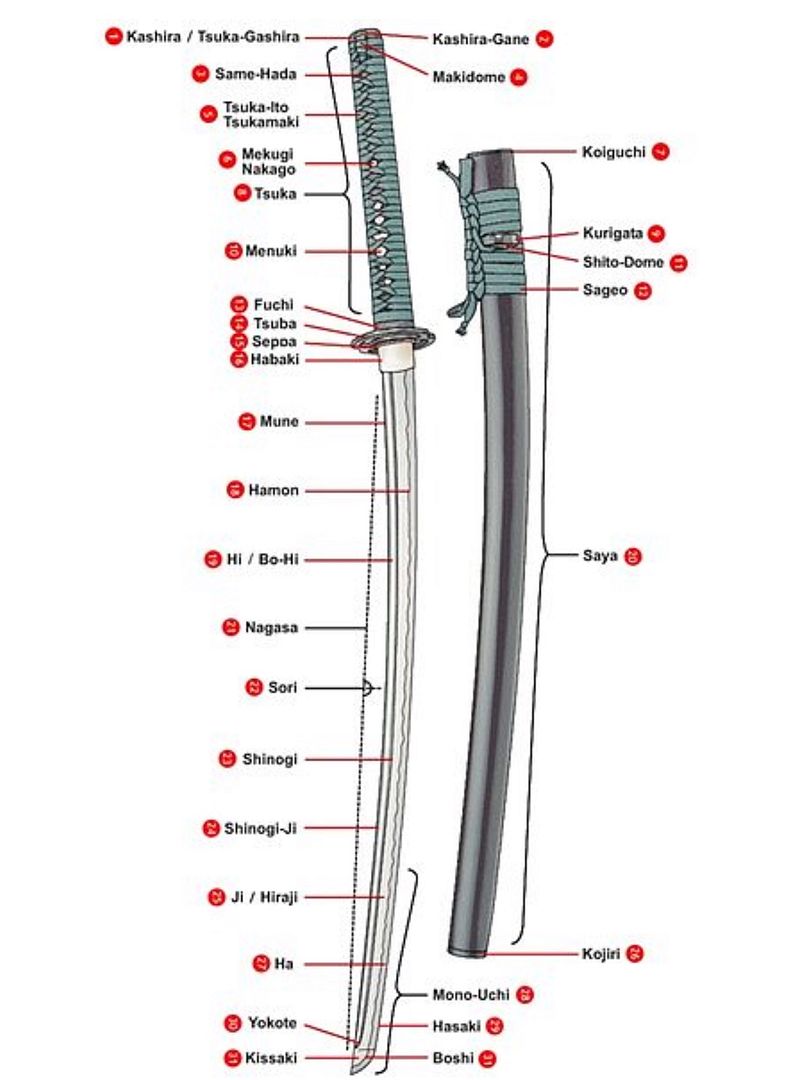
EDITED TO ADD FINISHED PICS



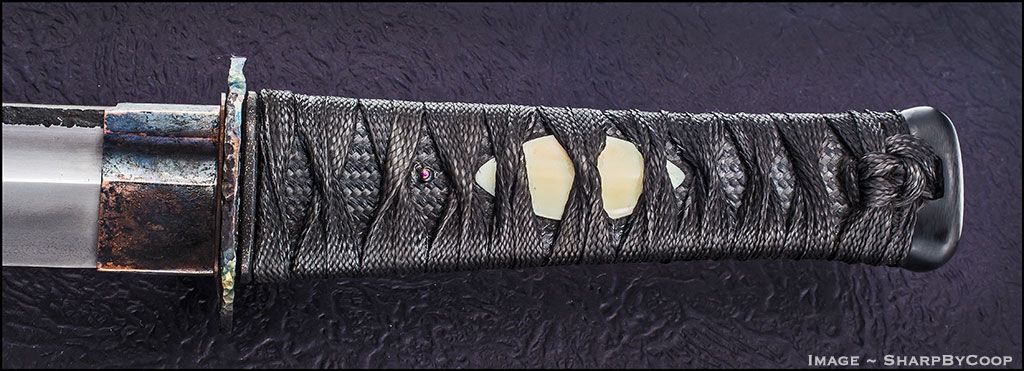
I will link all future videos here
UNBOXING VIDEO PAGE 17
https://www.youtube.com/watch?v=CSz0vEFhXIE
VIDEO 2 DESIGN ELEMENTS AND DROP CUT PAGE 18
https://www.youtube.com/watch?v=r1IwzPPrS1s
JUST DROP CUT VIDEO
https://www.youtube.com/watch?v=6C2wPgAbfPQ
VIDEO 3 TAMESHIGIRI
https://www.youtube.com/watch?v=RdNHmToC0Uk
VIDEO 4 CUTTING ROLLED PAPER
https://www.youtube.com/watch?v=Mevm97FtfCw
Last edited: