- Joined
- Jul 1, 2003
- Messages
- 270
Hey gents, it was about this time last year that I did the work-in-progress thread on the damascus camp knife. It's taken me until now to recuperate enough to give a WIP thread another go.
I'll be making a bowie with a laminated blade, damascus fittings and a micarta handle. The knife will also be a take-down.
I've been making laminated stainless / carbon blades for the last few years, and several people have asked how I get the stainless and the carbon to weld together, and a few people have even made some nice finished blades. Bill Burke, Bill Wiggins and Daniel Warren are three makers who come to mind who've made blades based at least in part on what I've learned. I thought I'd actually show some photos of how it's done for the rest of you. Though you may think it's hard, you'll see it's a lot simpler than you might have thought...
Here, three pieces of steel, (two 416 stainless and one 52100) are cleaned.
Some Loctite Professional super glue (not the civilian stuff, the Professional grade) is applied to each piece.
The pieces are clamped and left for at least 48 hours. If left for less than this, the molecular diffusion will not adequately take place.
After the diffusion is complete, the bar is ground down and etched to see the successfully welded core.
I'll be making a bowie with a laminated blade, damascus fittings and a micarta handle. The knife will also be a take-down.
I've been making laminated stainless / carbon blades for the last few years, and several people have asked how I get the stainless and the carbon to weld together, and a few people have even made some nice finished blades. Bill Burke, Bill Wiggins and Daniel Warren are three makers who come to mind who've made blades based at least in part on what I've learned. I thought I'd actually show some photos of how it's done for the rest of you. Though you may think it's hard, you'll see it's a lot simpler than you might have thought...
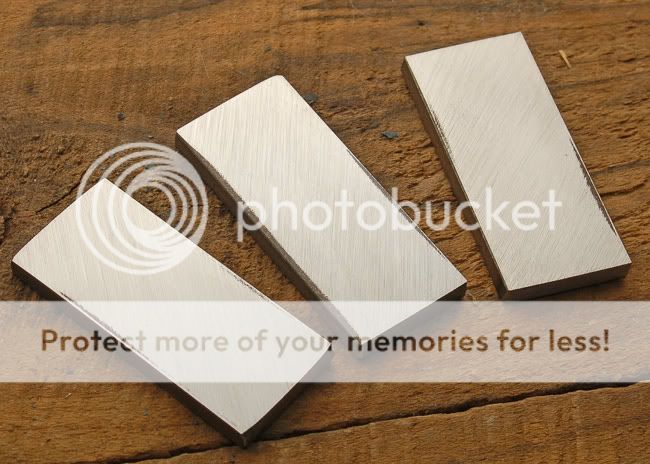
Here, three pieces of steel, (two 416 stainless and one 52100) are cleaned.

Some Loctite Professional super glue (not the civilian stuff, the Professional grade) is applied to each piece.

The pieces are clamped and left for at least 48 hours. If left for less than this, the molecular diffusion will not adequately take place.

After the diffusion is complete, the bar is ground down and etched to see the successfully welded core.