ETA...
Some people could not see the original pics anymore, so I recreated the pics in the following posts
Now, first things first. You have to be safe. My pics may show things that do not look safe. They are only shown that way for the effect of the WIP pics. Please use eye protection, and secure your materials when drilling or using power tools on them.
I think Evan did a WIP where he did everything with hand tools. That is admirable and amazing, but I would never get anything done that way. That being said, with some exceptions, most of these steps can be completed with hand tools and hand labor.
You will need standard hand tools, like files, a hacksaw, punches, a hammer, etc. A drill is pretty important also. Hand sanding can get the job done, but a power sander is extremely handy. You don't have to spend a boatload of money on tools, the 1" x 30" belt sander from harbor freight is a great bargain.
Okay, so you have a knife that you want to mod, let's say this Imperial is the one.
Those Imperials are a prime example of quality steel in an economy package, and well worth doing something with. Do yourself a favor and tape off the blades. I use painters tape, it doesn't affect etches.
The shell handle knife covers are typically held in place by a tab at each end that is bent over to hold it in place.
Use a small screwdriver or similar implement to bend the tab up on one end.
Once that is done, you should be able to remove the shell cover. Repeat for the other side, and you should have something that looks like this.
The inner assembly should look something like this
Use a drill to drill out the 3 rivets.
You can also use a file to file down the heads, but be mindful not to mark up or file anything that will show after.
Once you drill out or file down the rivet heads, you can punch them out.
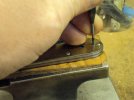